-
- News
- Books
Featured Books
- pcb007 Magazine
Latest Issues
Current IssueInventing the Future with SEL
Two years after launching its state-of-the-art PCB facility, SEL shares lessons in vision, execution, and innovation, plus insights from industry icons and technology leaders shaping the future of PCB fabrication.
Sales: From Pitch to PO
From the first cold call to finally receiving that first purchase order, the July PCB007 Magazine breaks down some critical parts of the sales stack. To up your sales game, read on!
The Hole Truth: Via Integrity in an HDI World
From the drilled hole to registration across multiple sequential lamination cycles, to the quality of your copper plating, via reliability in an HDI world is becoming an ever-greater challenge. This month we look at “The Hole Truth,” from creating the “perfect” via to how you can assure via quality and reliability, the first time, every time.
- Articles
- Columns
- Links
- Media kit
||| MENU - pcb007 Magazine
Process Yield Statistics and Distributions
November 25, 2024 | Dr. Pat Valentine, UyemuraEstimated reading time: 1 minute
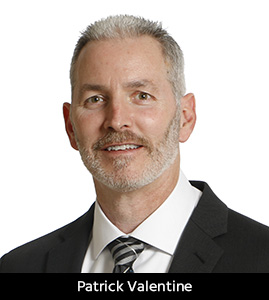
The costs of poor quality include all expenses incurred for not making or providing a perfect product the first time, including scrap, rework, re-purchasing raw materials, labor, and inventory1. Companies operating at a three-sigma quality level can spend about 25% of their annual sales remediating poor quality costs2. Other estimates put the costs of poor quality in the range of 25–40%3. Poor quality can destroy a company.
Unexpected product failures significantly increase sales, general, and administrative (SG&A) costs and lead to increases in inventories and fixed assets required to support operations. These indirect costs erode profitability more than those directly attributable to warranty claims processes. Product recalls negatively impact businesses financially and result in adverse publicity. Customers expect printed circuit boards to meet their specifications.
An internal Motorola study found that units reworked in production often encountered problems during early customer use, even though the defects identified were corrected during production. Rework can frequently stress a unit non-standardly and predispose a product to early failure4. Denson found a similar occurrence in semiconductor manufacturing, where the reliability of computer chips was statistically correlated with the die yield5. These studies suggest that circumstances in detecting and reworking defects in some units may produce undetected damage on other units. When delivered to customers, these weaknesses often contribute to early failures.
Defects are any items that exhibit a departure from specifications. A defect does not necessarily mean that the product cannot be used; it only indicates that the product result is not as intended. In essence, defects refer to quality characteristics. Generally, the count of defects is assumed to follow a Poisson distribution.
Defectives are units that are considered completely unacceptable for use. Each unit is deemed defective or not—there are only two choices. In essence, a defective unit refers to the overall product. Generally, the count of defective units is assumed to follow a binomial distribution.
To read this entire article, which appeared in the November 2024 issue of PCB007 Magazine, click here.
Testimonial
"In a year when every marketing dollar mattered, I chose to keep I-Connect007 in our 2025 plan. Their commitment to high-quality, insightful content aligns with Koh Young’s values and helps readers navigate a changing industry. "
Brent Fischthal - Koh YoungSuggested Items
Koh Young Highlights the Market Driven Nova Series and Smart Factory Solutions at Productronica India 2025
09/02/2025 | Koh YoungKoh Young, the global leader in True 3D measurement‑based inspection and smart factory platforms, is poised to highlight its cutting‑edge technologies at Productronica India 2025, running from September 17–19 at the Bangalore International Exhibition Centre (BIEC).
Defense Speak Interpreted: If CHIPS Cuts Back, What Happens to Electronics Packaging Funds?
09/02/2025 | Dennis Fritz -- Column: Defense Speak InterpretedIn my May column, I examined the topic of the CHIPS Act and its current status as a U.S. government program. I found that CHIPS activities continue, but some corporations have delayed or canceled them because of budget cuts or corporation-specific problems. However, CHIPS integrated circuits—mostly administered by the Department of Commerce—don’t fully drive the electronics interconnection activity being funded by the government. Let’s cover the progress/status of other programs:
Kopin Announces $9 Million Follow-On Contract for Defense Thermal Imaging Assembly
08/14/2025 | BUSINESS WIREKopin Corporation, a leading provider of application-specific optical systems and high-performance microdisplays for defense, training, industrial, consumer and medical products, today announced the award of an approximate $9 million follow-on production contract in support of a custom thermal imaging assembly build for a major U.S. defense prime contractor.
Facing the Future: Challenges and Opportunities in Reshoring PCB Manufacturing
08/12/2025 | Prashant Patel -- Column: Facing the FutureFor decades, offshore manufacturing dominated the global electronics industry. The pursuit of cost efficiency, scalability, and access to vast labor markets made countries like China, Taiwan, and Vietnam attractive destinations for printed circuit board (PCB) production. But a seismic shift is underway, from geopolitical instability and supply chain disruptions to rising labor costs and national security concerns.
Automated Production Equipment and Manncorp Announce Strategic Partnership to Expand SMT Solutions for U.S. Electronics Manufacturers
08/06/2025 | Automated Production EquipmentAutomated Production Equipment (APE), a trusted supplier of high-performance soldering and rework systems, proudly announces a strategic partnership with Manncorp, a leading provider of Surface Mount Technology (SMT) production equipment. This collaboration brings together two industry leaders to deliver expanded, end-to-end SMT solutions to electronics manufacturers across North America.