Understanding Depreciation for Electronic Manufacturers
December 4, 2024 | Doug Palladino, ASC Sunstone CircuitsEstimated reading time: 1 minute
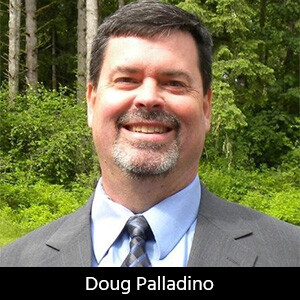
As a PCB design engineer, your focus is on creating innovative, cost-effective designs. However, the financial aspects behind your designs—such as depreciation—play a significant role in the overall business. While depreciation may sound like "accounting speak," understanding it can help you make better decisions for your projects, especially when dealing with equipment, machinery, or even intangible assets like software licenses. Most people don’t fully understand the meaning of depreciation, especially young engineers and designers entering the field, yet when it comes to calculating the total cost to manufacture or the total cost to operate, it is an important financial piece of the total manufacturing cost algorithm.
Here’s a breakdown of depreciation from a financial controller’s perspective, aimed at those less familiar with accounting.
Defining Depreciation
Depreciation is the process of allocating the cost of a tangible asset over its useful life. In other words, instead of recognizing the full equipment cost as an expense when purchased (e.g., a piece of equipment, a tool, or a machine), the expense is spread out over multiple years based on its expected useful life. This helps the financial reporting by preventing a large spike in expenses in the month the equipment was purchased.
For instance, if your company buys an $80,000 pick-and-place machine for PCB assembly that’s expected to last 10 years, you wouldn’t account for the entire $80,000 in the first year. Instead, you would record an expense of $8,000 each year over 10 years. This reflects how the machine is used to generate revenue over time.
To read this entire article, which appeared in the November 2024 issue of PCB007 Magazine, click here.
Suggested Items
WellPCB, OurPCB Launch Low-Cost PCB Assembly and Custom Cable Assembly Solutions
05/29/2025 | ACCESSWIREWellPCB and OurPCB, world leading PCB manufacturing service providers, announced today that they have officially launched new Low-Cost PCB Assembly Solutions and Custom Cable Assembly services to meet the needs of the electronics manufacturing industry for high cost performance and flexible customization.
Electronics Industry Demand Holds Steady Amid Tariff Turbulence
05/22/2025 | IPCElectronics manufacturers are bracing for higher costs as profit pressures deepen according to IPC’s May Sentiment of the Global Electronics Manufacturing Supply Chain Report.
LitePoint, Pegatron 5G Successfully Launch Volume Manufacturing of 5G O-RAN Radio Units to Power Private 5G Networks
05/21/2025 | BUSINESS WIRELitePoint, a leading provider of wireless test solutions, and Pegatron 5G, a leading provider of end-to-end 5G product solutions, have jointly announced a milestone in their collaboration; the start of high-volume manufacturing for 5G O-RAN radio units.
Fresh PCB Concepts: The Power of a Lunch & Learn for PCB Professionals
05/15/2025 | Team NCAB -- Column: Fresh PCB ConceptsIn the electronics industry, innovation isn’t simply a competitive edge, it’s a survival strategy. For those working in printed circuit board (PCB) design, engineering, procurement, and quality control, staying informed and connected is key to creating high-performance, cost-effective, and manufacturable products. Enter the Lunch & Learn—a simple yet highly effective format for professional development offering technical insights in short, informal sessions (served with lunch).
Localized Automation Becomes a Tariff Storm Safe Haven, but U.S. Smart Factory Build-Out Costs Far Exceed China’s
05/09/2025 | TrendForceTrendForce’s latest “Human-Machine Technology Report” points out that although the 90-day delay on the U.S. reciprocal tariffs announced by the Trump administration in early April 2025 offers temporary relief, it has already triggered lasting shifts in global manufacturing and supply chain strategies.