Has the Time Finally Come for Tin-nickel Plating?
December 9, 2024 | Marcy LaRont, PCB007 MagazineEstimated reading time: 1 minute
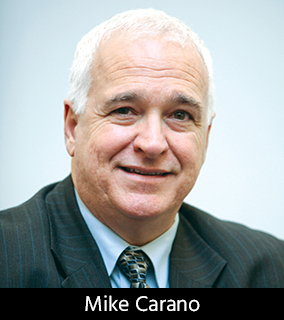
In the 1980s, Electrochemicals, Inc. (now Electrochemical Products) made a significant shift from furniture and industrial goods to electronics and manufacturing. During this journey, a tin-nickel plating alloy was developed. In 1984, Mike Carano, a young engineer, published a paper on tin-nickel plating alloy, but after some initial attention, the plating solution fell into obscurity.
Today, PCB fabrication looks largely the same, yet changes are afoot, chiefly due to the demands for very fine feature capability on printed circuit boards, as well as environmental sustainability. So, in this fascinating conversation with Mike Carano and Happy Holden, we take another look at tin-nickel and its advantages in both performance and sustainability.
Marcy LaRont: Mike, please explain the unique metal properties of the tin-nickel alloy and why fabricators should consider this as a surface finish solution today.
Mike Carano: Tin-nickel is a metastable alloy. It is monatomic, meaning that no matter what you do with the chemistry or how you manipulate the grams per liter of one metal or the other (or the amps per square foot), it always comes out as 65% of one metal and 35% of the other. I’m not aware this is true with any other combination of metals.
Typically, if your chemistry is out of balance—if you have more tin in the solution than you have lead—you will plate more tin. It’s precisely why there are so many alloys out there. In that respect, tin-nickel is pretty amazing.
Happy Holden: When I was at Hewlett-Packard, Dr. Morton Adler from Bell Labs called me and said he wanted us to fab his boards using tin-nickel, because he knew we were using it. I plated the boards with tin-nickel and added a gold strike. This thin gold was cobalt-hardened and the final thickness was still only 3–5 microinches when we finished. About a month after I sent them back to Adler, I got another call. He said, “What the hell did you send me? We’ve completed our reliability testing and your 3–5 microinches on tin-nickel outperforms our 120 microinches of sulfamate nickel on our contacts and other relays.”
Continue reading this conversation in the November 2024 issue of PCB007 Magazine.
Testimonial
"We’re proud to call I-Connect007 a trusted partner. Their innovative approach and industry insight made our podcast collaboration a success by connecting us with the right audience and delivering real results."
Julia McCaffrey - NCAB GroupSuggested Items
Lockheed Martin Awarded $720 Million Contract for JAGM, HELLFIRE Production
08/22/2025 | Lockheed MartinThe U.S. Army has awarded Lockheed Martin a $720 million contract for the production of Joint Air-to-Ground Missiles (JAGM) and HELLFIRE missiles, marking the fourth and final follow-on award as part of its current multiple-year contract.
I-Connect007 Editor's Choice: Five Must-Reads for the Week
08/22/2025 | Andy Shaughnessy, I-Connect007In this week’s roundup, we have a variety of articles covering design, manufacturing, sustainability, and, of course, tariff negotiations. We have a milestone anniversary to celebrate as well, with Dan Beaulieu about to publish his 1,000th column. When does Dan even sleep? Here’s to hoping that we have 1,000 more weeks of "It’s Only Common Sense."
Ta Yang Group Holdings Limited Announcing AI Transformation Blueprint
08/21/2025 | ACN NewswireTa Yang Group Holdings Limited, a well-established Hong Kong-listed company with nearly two decades of market presence, plans to further advance comprehensively into the Web 4.0 field and artificial intelligence (AI) industry.
Lessons From a Thousand Columns: Dan Beaulieu on Writing, Selling, and Staying the Course
08/21/2025 | Michelle Te, I-Connect007For 20 years, Dan Beaulieu has been a steady voice in sales and marketing, offering weekly columns that challenge, inspire, and guide professionals in the electronics industry and beyond. Soon, he will reach a remarkable milestone—his 1,000th It’s Only Common Sense weekly column. In this Q&A, we look behind the scenes of Dan’s writing journey, exploring what has kept him motivated, the lessons he’s learned along the way, and how two decades of weekly columns have shaped his career and the industry conversation.
Haylo Labs Acquires Plessey Semiconductors
08/20/2025 | Haylo LabsHaylo Labs has acquired Plessey Semiconductors, the UK’s leading innovator in microLED display technology.