Elephantech: For a Greener Tomorrow
April 16, 2025 | Marcy LaRont, PCB007 MagazineEstimated reading time: 3 minutes
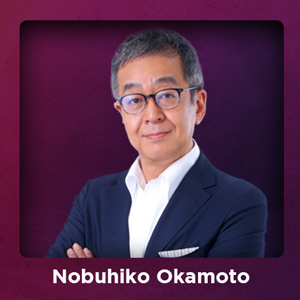
Nobuhiko Okamoto is the global sales and marketing manager for Elephantech Inc., a Japanese startup with a vision to make electronics more sustainable. The company is developing a metal inkjet technology that can print directly on the substrate and then give it a copper thickness by plating. In this interview, he discusses this novel technology's environmental advantages, as well as its potential benefits for the PCB manufacturing and semiconductor packaging segments.
Marcy LaRont: Nobu, can you explain this process of inkjet metallization?
Nobu Okamoto: We directly print on the substrate and then add the plating to reduce the etching and washing process for flexible printed circuit (FPC) production or rigid PCB production. We have already succeeded for three years in mass production and commercializing the single-layer FPC. I think this is a very rare case in printed electronics to have already been commercialized and succeeded.
At the end of last year, we successfully created a sample of multilayer FR-4. We are now looking for a partner to collaborate with on this project. Additionally, this technology can also be adapted for use with aluminum or glass substrates.
LaRont: So, is this for PCBs and some semiconductor packaging technology as well?
Okamoto: This is very fortunate because after we developed it for PCB manufacturing, we found that our printer, our ink, can print over glass, aluminum, or ceramics. Many customers are asking us, "Can you print on ceramic?” or "Can you print on glass?” because they are looking for many things, not just for the PCB. They are especially looking for semiconductor packaging or other applications. We are expanding our target customers and trying to solve the various customer requirements.
LaRont: What is the difference between copper, aluminum, and ceramic glass? Is there trouble with adhesion?
Okamoto: For the moment, the whole material complies with IPC standards. As I mentioned, we are trying to make electronics sustainable; that's why we are providing the solutions. We can develop different solutions for other requirements. This may include a different ink, printer, or primer.
LaRont: If a customer has a request, you want to partner with them to create a solution?
Okamoto: Yes, but we are a very small company, so we would like a real partner. For my part, I would appreciate some testing or something similar. It can be quite challenging, but if businesses are facing issues and would like to resolve them using our technology, we are always open to collaboration.
LaRont: That's really important. If you want to add value in electronics manufacturing today, you really have to be in that space where you'll partner with your customers on NPI and such.
Okamoto: Until today, it's been quite difficult because our biggest advantage is sustainability. Everybody says that sustainability is very important, but it's really tough to make decisions, especially in the FPC and PCB areas. We have already established a net-zero target internally, and the European side is expressing concerns about this. This is a good time to consider implementing this manufacturing method, which typically takes two to three years. It’s an excellent opportunity to aim for a target year of 2030 or 2035.
LaRont: I agree that everybody's talking about it but having trouble doing it. If you know anything about inkjet technology, you know there's a lot less waste and so much less copper. What are the sustainability benefits of your technology?
Okamoto: We don't have any washing and etching process so we can reduce water consumption by 95%. No etching means fewer chemical contaminants. As a result, we can reduce 75% CO2 emissions.
LaRont: That's quite a lot of green right there.
Okamoto: Also, many people consider green technology expensive, but copper and water are very expensive resources now. With our technology, you can reduce copper by 70%, so your manufacturing costs should be lower.
LaRont: We're approaching the point where it will be just as costly not to do it.
Okamoto: The advantage of our technology is we use 100% of the copper ink and the copper plating, so it can be possible to directly replace what our customers are using now. There's no compromise.
LaRont: Requalification is one thing, but there’s no need to redesign?
Okamoto: No need to redesign.
LaRont: Nobu, it sounds like exciting technology. Hopefully we'll hear more about it in the future.
Okamoto: Thank you very much.
Suggested Items
Zhen Ding Promotes Digital Transformation and Embraces AI Business Opportunities
06/06/2025 | Zhen Ding TechnologyOn May 27, 2025, General Manager Chen-Fu Chien of Zhen Ding Technology Group was invited to attend the "2025 Two Thousand Forum" held by The CommonWealth Magazine.
Leidos Using Quantum Technology to Thwart GPS Jamming
06/05/2025 | PRNewswireSusceptibility to jamming is a significant military vulnerability of the Global Positioning System (GPS) signal. Through a Defense Innovation Unit contract, Leidos is developing an alternative navigation technology that measures variations in the Earth's magnetic field and harnesses the quantum properties of nitrogen in diamonds.
Growing Demand for Mid-Size Displays Opens New Opportunities for FMM-Free OLED Technologies
06/05/2025 | TrendForceTrendForce’s latest report on the display industry reveals that OLED technology—valued for its self-emissive structure, high contrast ratio, and lightweight design—continues to expand its market presence, primarily in small-size applications such as smartphones.
Orbel Corporation Integrates Schmoll Direct Imaging
06/04/2025 | Schmoll AmericaOrbel Corporation in Easton, PA, proudly becomes the first PCM facility in the U.S. equipped with Schmoll’s MDI Direct Imaging system. This installation empowers Orbel to support customers with greater precision and quality.
BAE Systems Unveils Comprehensive Line of M-Code GPS Receivers at Joint Navigation Conference
06/04/2025 | PRNewswireBAE Systems unveiled a diverse line of M-Code Global Positioning System (GPS) receiver solutions at the Joint Navigation Conference in Cincinnati this week, rounding out an extensive line of products that ensure U.S. warfighters have the most dependable GPS systems available across sea, land, and air.