Key Insights on Photoresist for Defect Reduction
May 21, 2025 | I-Connect007 Editorial TeamEstimated reading time: 2 minutes
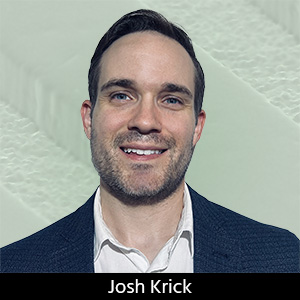
Feature Q&A with Josh Krick and Tim Blair, IEC
In PCB manufacturing, understanding the intricacies of the photoresist process is crucial for achieving high-quality results. Industry experts Josh Krick, a technical service engineer at IEC, and Tim Blair, a PCB imaging specialist at Tim Blair LLC, share their knowledge on the essential stages of photoresist application, highlight critical advancements in materials, and discuss common defects encountered during production. They share best practices and innovative solutions to enhance the manufacturing process, reduce defects, and ensure efficiency and reliability in high-tech applications.
What are the most critical steps in the photoresist process in PCB fabrication for ensuring high-quality results?
Josh Krick: When focusing on the photoimaging process, we will always work our way from the ground up: surface preparation, lamination, exposure, and then finish with developing. Certainly, if deemed necessary, we can also focus on the additional processes of stripping the photoresist, etching, and even plating applications. Each one of these steps is just as crucial as the next. All these processes should have daily checks and protocols to ensure consistency and repeatability. However, if I had to choose one process as the most critical, I would say that surface preparation is arguably the most critical process. Think of it in terms of building a house, where a good foundation is critical for success.
Tim Blair: During my imaging training sessions, I always stress that pre-cleaning is critical to the imaging process. Good pre-cleaning will Increase the latitude of the resist through the rest of the imaging process. But I always emphasize the importance of cleaning the resist-coated inner layer cores and outer layer panels at exposure. A direct image printer’s forgiveness for micro debris is zero. You will not burn out this micro debris on a DI printer like you could on a flood or point light source contact printer. Collimated DI printers are super sensitive to micro debris. Clean, clean, and clean some more.
What are some of the latest advancements in photoresist materials or processes that have significantly impacted PCB manufacturing?
Krick: The biggest advancements in the field are focused on high resolution, high adhesion, thin resists 1 mil thick (25) for IC substrates, and various higher technology needs. These resists will provide the capability to go less than 1:1 with resist height for high resolution and small feature sizes while still providing enough resist height for plating applications. We have customers with goals of finished product in the 12-20 μm range in terms of feature sizes after etching.
To read this entire conversation, which appeared in the May 2025 issue of PCB007 Magazine, click here.
Testimonial
"In a year when every marketing dollar mattered, I chose to keep I-Connect007 in our 2025 plan. Their commitment to high-quality, insightful content aligns with Koh Young’s values and helps readers navigate a changing industry. "
Brent Fischthal - Koh YoungSuggested Items
Global Dry Film Photoresist Market Set for Robust Growth with Expanding Semiconductor Ecosystem
06/24/2025 | PRNewswireIn 2024, the global market size of Dry Film Photoresist was estimated to be worth US$939 million and is forecast to reach approximately US$1191 million by 2031 with a CAGR of 3.5% during the forecast period 2025-2031.
2024 Global Semiconductor Materials Market Posts $67.5 Billion in Revenue
04/29/2025 | SEMIGlobal semiconductor materials market revenue increased 3.8% to $67.5 billion in 2024, SEMI, the global industry association representing the electronics design and manufacturing supply chain, reported in its Materials Market Data Subscription (MMDS).
DuPont to Discuss Development of EUV Photoresists at SPIE Advanced Lithography + Patterning Conference
02/13/2025 | DuPontDuPont today announced its participation in the 2025 SPIE Advanced Lithography + Patterning conference, taking place Feb. 24–28 in San Jose, California. DuPont will showcase its latest innovations through technical presentations focused on the development of photoresists for extreme ultraviolet (EUV) lithography and advancing sustainability in the design of lithographic materials.
Connect the Dots: Designing for Reality: Strip-Etch-Strip
12/05/2024 | Matt Stevenson -- Column: Connect the DotsIn the previous episode of I-Connect007’s On the Line with… podcast, we focused on pattern plating. At this point, we are close to completing our boards and ready for the strip-etch-strip (SES) process. By this stage of the manufacturing process, we have laminated all the internal layers together, drilled the through-holes, applied the image to the external layers through photoresist, plated the copper in those channels to beef up the copper thickness for traces, pads, and through-holes, added a layer of electrolytic tin over the top of that copper to protect it during subsequent stages of production.
DuPont Names Drew Chambers Global Business Director for Lithography Technologies
01/22/2024 | DuPontDuPont announced that Drew Chambers has been named global business director, Lithography Technologies business in DuPont Electronics & Industrial, effective Jan. 1. Chambers succeeds George Barclay, Ph.D., who has elected to retire after more than 25 years of service.