-
- News
- Books
Featured Books
- pcb007 Magazine
Latest Issues
Current IssueInventing the Future with SEL
Two years after launching its state-of-the-art PCB facility, SEL shares lessons in vision, execution, and innovation, plus insights from industry icons and technology leaders shaping the future of PCB fabrication.
Sales: From Pitch to PO
From the first cold call to finally receiving that first purchase order, the July PCB007 Magazine breaks down some critical parts of the sales stack. To up your sales game, read on!
The Hole Truth: Via Integrity in an HDI World
From the drilled hole to registration across multiple sequential lamination cycles, to the quality of your copper plating, via reliability in an HDI world is becoming an ever-greater challenge. This month we look at “The Hole Truth,” from creating the “perfect” via to how you can assure via quality and reliability, the first time, every time.
- Articles
- Columns
- Links
- Media kit
||| MENU - pcb007 Magazine
AI-driven MES Rewriting the Rules of Manufacturing Transformation
July 23, 2025 | Francisco Almada Lobo, Critical ManufacturingEstimated reading time: 7 minutes
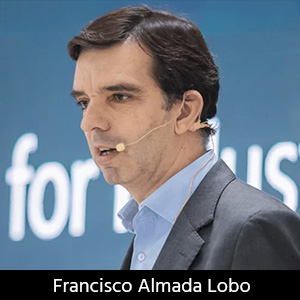
The Critical Manufacturing MES & Industry 4.0 International Summit, June 12–13, revealed a profound shift in how manufacturers approach digital transformation. AI-enabled execution systems are no longer a future ambition but are essential for navigating complexity and driving change.
The MESI 4.0 Summit in Porto did not deal with generalities. More than 600 attendees from 36 countries gathered at the Alfândega Congress Centre to address the challenging questions surrounding the digital future of manufacturing. The mood was pragmatic, at times confrontational, and increasingly aligned around one truth: AI is not a layer to add but a force to rebuild around.
Speakers cut through the noise of transformation theatre and exposed the structural gaps between ambition and implementation. At the centre of that discussion sat the manufacturing execution system, no longer a background actor in smart manufacturing but the primary stage upon which intelligent operations must now be built.
The MES Layer is No Longer Optional
I opened the summit with a challenge to legacy thinking. The traditional MES, built around static workflows and rigid hierarchies, has become a barrier to agility. In its place, I outlined a vision of execution software that can interpret context, reason autonomously, and adapt to changes in real time.
This shift reframes MES not as an execution tool but as an engine of intelligence. Yet, to power that intelligence, manufacturers need more than clean data; they need deeply integrated, contextualised information flowing across every layer of the stack. Without the right data foundation, your AI is just guessing.
The new architecture requires full integration among three core layers: the MES for orchestration, IoT platforms for data acquisition, and modern data platforms for scalable data transformation. Each must feed and respond to the others, forming a closed feedback loop that turns operational data into real-time decisions.
This evolving stack redefines how value is created on the factory floor. It is no longer enough to visualise what has happened or even predict what might happen. The system must be able to reason through scenarios, adapt to deviations, and act in timeframes that match the speed of production.
From Logic to Agency
The MESI summit marked a significant shift in how AI is perceived. Early projects focused on predictive analytics and dashboarding. The conversation has now shifted toward the embedded agency, where AI agents with goals, memory, and planning capabilities operate within the execution environment.
Instead of encoding every rule and exception into the software, manufacturers are now enabling systems to set goals and self-correct. The agent identifies a machine failure, queries historical data, adjusts schedules, and reallocates resources without predefined scripts. This is not hypothetical. New standards and protocols enable software agents to access MES APIs, interpret production context, and execute adaptive decisions. The result is a shift from deterministic automation to dynamic intelligence.
This progression can be described in three stages: rules-based automation, adaptive agents, and self-organising multi-agent ecosystems where each system’s function, maintenance, scheduling, and quality is delegated to a specialised learning agent. Where traditional MES systems struggle to scale across high-variance operations or complex supply networks, these new architectures offer a fundamentally more elastic response. They enable decisions that are decentralised yet coherent, accelerating responsiveness without losing governance.
Culture Remains the Constraint
While technology has advanced rapidly, the organisational pace has not kept up. Analyst Rick Franzosa brought a necessary skepticism to the event, urging manufacturers to stop romanticising AI and start building for it. The problem, he argued, is not that GenAI is immature but that manufacturers are deploying it on broken foundations. Most MES environments still depend on siloed data, undocumented workflows, and tribal knowledge buried in spreadsheets. Under those conditions, even the most potent model will fail.
Rather than focusing solely on platforms, Franzosa urged leaders to address workforce engagement and cognitive resistance. "People do not fear technology," he said. "They fear losing control." Real transformation, in his view, begins with shifting mindsets, not just codebases. He also questioned the narrative of complete autonomy. Most successful deployments today, he noted, still involve human-in-the-loop systems, where AI augments rather than replaces decision-making. Transparency, trust, and traceability must be built into the system from the outset, not added after a failed pilot.
Europe's Industrial Hesitancy Exposed
That hesitation to act came under sharp critique from Walker Reynolds, who warned that much of Europe's manufacturing base is still paralysed by outdated mindsets and fragmented digital strategies. He challenged the audience with a simple benchmark: Barely half the room raised their hand when asked if their factory was actively engaged in digital transformation. "If this were a safety meeting and only half followed protocol, it would be chaos," he said. "Yet we accept it when it comes to digital operations."
Reynolds's focus was architectural. Rather than chasing dashboards and disconnected pilots, he advocated for a unified namespace, a semantic, real-time digital backbone into which every system can publish and consume. The aim is not visibility but self-awareness. The plant should know what it is doing at any moment, across every layer, in every process. He warned that without this architecture AI adoption would be cosmetic at best. The factory becomes more visual but not more intelligent.
Intelligence at the Edge
Several sessions went beyond the theoretical and explored how these architectural shifts are playing out at the network edge. Hugo Rego of Red Hat outlined how manufacturers are pushing AI workloads closer to the source of data into controllers, IPCs, and edge nodes that operate independently of centralised infrastructure. This model is becoming critical for low-latency decision-making, especially in industries with disconnected or constrained environments. Rego explained how edge-based agents can execute logic locally while synchronising with central systems when connectivity allows.
The key is consistency. "You cannot compromise control just because a node is remote," he said. "The logic must hold, whether you are on the shop floor or 3,000 miles away." This distributed intelligence not only reduces latency but also increases resilience, enabling operations to adapt even when central systems are offline or bandwidth is restricted.
Resilience and Responsiveness in the Spotlight
That emphasis on operational resilience was echoed by Dr. Thomas Kaufmann of Infineon and Christoph Lettenbauer of ASMPT. Kaufmann described how the company has built synchronised MES infrastructures across multiple global sites to support fast responses to quality deviations and supply chain disruptions. When an issue is identified in one factory, affected material can be quarantined immediately across the entire production network.
Lettenbauer shared the challenge of managing complexity at scale. In one high-volume site, over 1.5 million significant events are generated daily across 20 SMT lines. "Data is no longer a by-product," he said. "It is the environment we operate in." Both speakers reinforced the shift from data collection to data orchestration, where the system sees and reacts. This capacity to simulate, benchmark, and intervene before failure is no longer nice to have. It is becoming the baseline for competitiveness.
The Human Operating System
For all the emphasis on systems and structure, the most persistent theme of the MESI Summit was human. As AI continues to reshape what MES can do, its long-term success will depend not just on algorithms but on alignment between people, processes, and purposes.
Leaders will be judged not by how fast they adopt AI but by how well they reshape their organisations around it. That includes building digital trust, prioritising explainability, and giving frontline teams the clarity to collaborate with intelligent systems rather than work around them.
I closed the summit with a final provocation: The tools now exist, the architecture is known, and the agents are already running. If you are still waiting for clarity, you are already behind.
MES is no longer a record of what happened, it is becoming how factories think. The question now is whether leaders can keep up with the systems they are about to deploy. It won’t be enough to simply withstand disruption, the organizations that shape what comes next will be the ones that lead it.
Access the Full MESI 4.0 Summit Sessions
All recordings of the keynote presentations and expert talks from the MESI 4.0 Summit 2025 are now available online. For those interested in revisiting the discussions or exploring sessions they may have missed, the full collection can be found here.
Francisco Almada Lobo is CEO and co-founder of Critical Manufacturing.
Testimonial
"Advertising in PCB007 Magazine has been a great way to showcase our bare board testers to the right audience. The I-Connect007 team makes the process smooth and professional. We’re proud to be featured in such a trusted publication."
Klaus Koziol - atgSuggested Items
Walt Custer: Making Data Interesting
09/03/2025 | Andy Shaughnessy, I-Connect007I just learned that IPC Hall of Famer Walt Custer has passed away at 81. I first met Walt about 20 years ago when I started covering the fabrication industry. Right away, he started telling me which companies to watch and which trends to follow. This was in the years following 9/11, and things were still pretty fluid.
Altus Supports Datalink Electronics with Advanced Selective Soldering Solution to Boost Manufacturing Efficiency
09/02/2025 | Altus GroupDatalink Electronics has partnered with Altus Group to integrate a cutting-edge automated soldering solution, enhancing its production capabilities and reinforcing its strategic focus on quality, automation, and scalability.
Wisdom From Data-center Power Pioneer Mike Mosman
09/02/2025 | Barry Matties, I-Connect007Few engineers have moved the levers of modern electronics more decisively than Mike Mosman. From the pre-email computer rooms of the 1980s to today’s hyperscale campuses cranking out AI cycles, the retired power engineer and co-founder of CCG Facilities Integration has spent four decades proving that uptime is a design discipline, not a hope.
HPE Accelerates Self-driving Network Operations with New Mist Agentic AI-native Innovations
08/26/2025 | BUSINESS WIREHPE announced major innovations to its HPE Juniper Networking portfolio, advancing its AI-native Mist platform to deliver agentic AIOps through more autonomous, intelligent and proactive network operations.
Macronix Introduces Cutting-Edge Secure-Boot NOR Flash Memory
08/08/2025 | PRNewswireMacronix International Co., Ltd., a leading integrated device manufacturer in the non-volatile memory (NVM) market, announced ArmorBoot MX76, a robust NOR flash memory combining in a single device, the essential performance and an array of security features that deliver rapid boot times and iron-clad data protection.