-
- News
- Books
Featured Books
- pcb007 Magazine
Latest Issues
Current IssueInventing the Future with SEL
Two years after launching its state-of-the-art PCB facility, SEL shares lessons in vision, execution, and innovation, plus insights from industry icons and technology leaders shaping the future of PCB fabrication.
Sales: From Pitch to PO
From the first cold call to finally receiving that first purchase order, the July PCB007 Magazine breaks down some critical parts of the sales stack. To up your sales game, read on!
The Hole Truth: Via Integrity in an HDI World
From the drilled hole to registration across multiple sequential lamination cycles, to the quality of your copper plating, via reliability in an HDI world is becoming an ever-greater challenge. This month we look at “The Hole Truth,” from creating the “perfect” via to how you can assure via quality and reliability, the first time, every time.
- Articles
- Columns
- Links
- Media kit
||| MENU - pcb007 Magazine
Estimated reading time: 1 minute
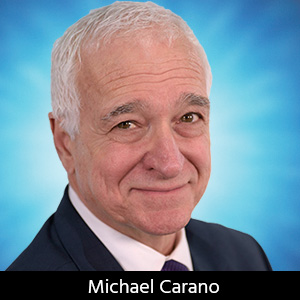
Contact Columnist Form
Controlling the ENIG Process for Optimum Efficiency and Performance
Introduction
In last month’s Trouble in Your Tank, different levels of corrosion in the nickel deposit were presented. In addition, the suggestion was made that mid-phosphorous content EN process was more beneficial with respect to solderability, as opposed to a high phos content nickel deposit. Certainly, concerns with corrosion of the nickel (with lower phos) were allayed as long as the proper process controls were in place. Ideally, the ENIG process must provide the optimum in solder joint reliability while operating at the highest level of cost efficiency. All too often, process parameters that have the most influence on these critical attributes are poorly understood. An example of poor control is shown in Figure 1. The gold deposit has been removed in order to expose the electroless nickel surface.
It is very difficult to discern any anomalies in the nickel deposit without removing the gold. It is clear from the SEMs in Figure 1 that there is significant corrosion on the electroless nickel surface. Obviously, this is an unacceptable situation, and in order to prevent it one must work harder to optimize and control the electroless nickel-immersion gold process. Some of these factors will now be presented in detail.
Critical Electroless Nickel Features:
- Phosphorous content control in the electroless nickel deposit. Don’t underestimate this important parameter.
- Stabilizers in the EN solution influence phosphorous content in the deposit.
- Phos content has strong influence on solderability, immersion gold deposit thickness and potential for hyper-corrosion.
Let’s look at these points in a little more detail.
As I have written in this monthly column on many occasions, operating the chemical processes within the process window is the key to consistent and predictable performance. After all, your customers should expect no less from you. So with respect to #1 above, it is recommended that the EN process be able to maintain a reasonably tight window with respect to phos content through five metal (MTOs) turnovers in the nickel solution.
Read the full column here.
Editor's Note: This column originally appeared in the August 2014 issue of The PCB Magazine.
More Columns from Trouble in Your Tank
Trouble in Your Tank: Metallizing Flexible Circuit Materials—Mitigating Deposit StressTrouble in Your Tank: Can You Drill the Perfect Hole?
Trouble in Your Tank: Yield Improvement and Reliability
Trouble in Your Tank: Causes of Plating Voids, Pre-electroless Copper
Trouble in Your Tank: Organic Addition Agents in Electrolytic Copper Plating
Trouble in Your Tank: Interconnect Defect—The Three Degrees of Separation
Trouble in Your Tank: Things You Can Do for Better Wet Process Control
Trouble in Your Tank: Processes to Support IC Substrates and Advanced Packaging, Part 5