-
- News
- Books
Featured Books
- pcb007 Magazine
Latest Issues
Current IssueInventing the Future with SEL
Two years after launching its state-of-the-art PCB facility, SEL shares lessons in vision, execution, and innovation, plus insights from industry icons and technology leaders shaping the future of PCB fabrication.
Sales: From Pitch to PO
From the first cold call to finally receiving that first purchase order, the July PCB007 Magazine breaks down some critical parts of the sales stack. To up your sales game, read on!
The Hole Truth: Via Integrity in an HDI World
From the drilled hole to registration across multiple sequential lamination cycles, to the quality of your copper plating, via reliability in an HDI world is becoming an ever-greater challenge. This month we look at “The Hole Truth,” from creating the “perfect” via to how you can assure via quality and reliability, the first time, every time.
- Articles
- Columns
- Links
- Media kit
||| MENU - pcb007 Magazine
Estimated reading time: 1 minute
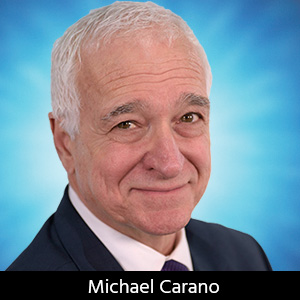
Contact Columnist Form
Oxide vs. Oxide Alternative Chemistry for High-Performance Resin Systems, Part 1
Introduction
By now a good percentage of the PCB fabrication world has graduated to the use of oxide alternative as a means for enhancing the inter-laminar bond strength between copper circuitry and the resin system. However, conventional brown or black oxide systems, as these are commonly called, have continued to serve the industry well. Indeed, frequent visits to Asia have shown me that oxide chemistry is alive and well. So before dedicating the next few columns to oxide alternative chemistry, it would be appropriate to present the current state of conventional oxide. I can honestly say that the death of conventional-reduced oxide has been greatly exaggerated.
Oxide vs. Oxide Alternative
Anyone involved in PCB fabrication during the last 25 years should understand that standard oxide treatment of innerlayers to enhance bond strength between the copper and resin has served the industry well. Oxidation of the copper surfaces for multilayer board fabrication was borrowed from the general metal finishing industry. Basically, it is a simple process best characterized as the controlled anodic oxidation of copper in an alkaline medium. To refresh the memory, the purpose of the oxidation step serves a two-fold purpose: 1) passivation of the copper surface and 2) enhancement of bond strength between the resin and copper. Look at this as the copper oxide crystals providing a high surface area on the copper so that the resin can flow through oxide crystals and provide a heat-resistant bond. With respect to passivation, the concern is that when B-stage resins and unpassivated copper surfaces are bonded together under high heat and pressure conditions, water can be a by-product of this reaction. With moisture now in the bond line, the water can vaporize, thus weakening the bond significantly. A properly passivated copper surface will resist water formation, thus eliminating delamination from occurring (with respect to moisture). Note this warning: A properly passivated copper surface is very important. In a future column, I will discuss this subject in more detail, including what constitutes a poorly passivated copper surface.
Read the full column here.
Editor's Note: This column originally appeared in the February 2014 issue of The PCB Magazine.
More Columns from Trouble in Your Tank
Trouble in Your Tank: Metallizing Flexible Circuit Materials—Mitigating Deposit StressTrouble in Your Tank: Can You Drill the Perfect Hole?
Trouble in Your Tank: Yield Improvement and Reliability
Trouble in Your Tank: Causes of Plating Voids, Pre-electroless Copper
Trouble in Your Tank: Organic Addition Agents in Electrolytic Copper Plating
Trouble in Your Tank: Interconnect Defect—The Three Degrees of Separation
Trouble in Your Tank: Things You Can Do for Better Wet Process Control
Trouble in Your Tank: Processes to Support IC Substrates and Advanced Packaging, Part 5