-
- News
- Books
Featured Books
- pcb007 Magazine
Latest Issues
Current IssueInventing the Future with SEL
Two years after launching its state-of-the-art PCB facility, SEL shares lessons in vision, execution, and innovation, plus insights from industry icons and technology leaders shaping the future of PCB fabrication.
Sales: From Pitch to PO
From the first cold call to finally receiving that first purchase order, the July PCB007 Magazine breaks down some critical parts of the sales stack. To up your sales game, read on!
The Hole Truth: Via Integrity in an HDI World
From the drilled hole to registration across multiple sequential lamination cycles, to the quality of your copper plating, via reliability in an HDI world is becoming an ever-greater challenge. This month we look at “The Hole Truth,” from creating the “perfect” via to how you can assure via quality and reliability, the first time, every time.
- Articles
- Columns
- Links
- Media kit
||| MENU - pcb007 Magazine
Estimated reading time: 1 minute
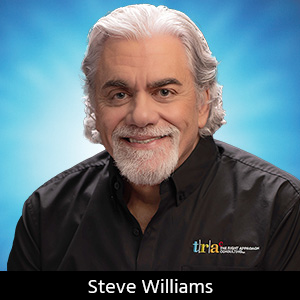
Customer Feedback: Perception is Reality
“Perception is reality.”
—Tom Peters, best-selling author
This quote from my favorite business author, Tom Peters, hangs in my office as a constant reminder. The title “world-class” rings hollow if you are the only one saying it about your organization.
Reality
How many times do we see a company promoting themselves as being a world-class manufacturer of PCBs, or as having been voted best-in-class at customer service? Who voted? Again, we are faced with the truth in advertising dilemma. It’s a Dilbert cartoon in the making: A group of senior managers get together and declare “you know, we do a pretty respectable job in our business, let’s begin calling ourselves world-class.”
What does it mean to be world-class? Breaking it down into a single bullet point, it means being on par with the top performers globally in your chosen craft. There are, of course, numerous quantitative metrics used to measure this, such as turnover, quality certifications, productivity, and the requisite financial ratios. But perhaps the most important metric is qualitative: How do your customers think you are doing?
The Facts
You may in fact be a world-class manufacturer, but if your customers don’t agree it doesn’t really matter. It is surprising to find the high percentage of PCB organizations that have not formally incorporated an annual benchmark survey into their continuous improvement process. True world-class companies are no longer guessing what satisfies their customers; they are actively soliciting feedback and listening to their customers’ expectations. A recent poll of over 2100 manufacturing respondents conducted by Industry Week Census supports this fact. It showed that 47% of respondents who say they’ve achieved a high level of world-class compliance use customer-satisfaction surveys extensively, while the proportion of peers claiming “no progress” in this area show only 6.4% as using them.
Read the full column here.
Editor's Note: This column originally appeared in the April 2014 issue of The PCB Magazine.
More Columns from The Right Approach
The Right Approach: ‘Twas the Night Before Christmas (Harley-style)The Right Approach: I Hear the Train A Comin'
The Right Approach: Culture Change is Key to a QMS
The Right Approach: Leadership 101—Be a Heretic, Not a Sheep
The Right Approach: Leadership 101—The Law of Legacy
The Right Approach: Leadership 101: The Law of Explosive Growth
The Right Approach: Leadership 101—The Law of Timing
The Right Approach: The Law of Sacrifice