-
- News
- Books
Featured Books
- pcb007 Magazine
Latest Issues
Current IssueInventing the Future with SEL
Two years after launching its state-of-the-art PCB facility, SEL shares lessons in vision, execution, and innovation, plus insights from industry icons and technology leaders shaping the future of PCB fabrication.
Sales: From Pitch to PO
From the first cold call to finally receiving that first purchase order, the July PCB007 Magazine breaks down some critical parts of the sales stack. To up your sales game, read on!
The Hole Truth: Via Integrity in an HDI World
From the drilled hole to registration across multiple sequential lamination cycles, to the quality of your copper plating, via reliability in an HDI world is becoming an ever-greater challenge. This month we look at “The Hole Truth,” from creating the “perfect” via to how you can assure via quality and reliability, the first time, every time.
- Articles
- Columns
- Links
- Media kit
||| MENU - pcb007 Magazine
Estimated reading time: 1 minute
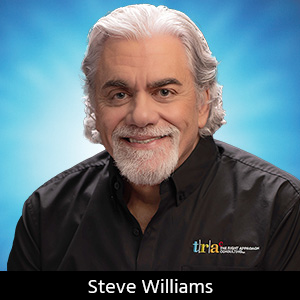
Time for a 'Lean Diet'
In the drive to continuous improvement, while Lean is one of the most powerful tools available to organizations, it is also one of the most underutilized. What follows is a primer for companies considering the Lean journey.
We strive to decide our own fate. We act with self-reliance, trusting in our own abilities. We accept responsibility for our conduct and for maintaining and improving the skills that enable us to produce added value.
—from Toyota Motor Corporation’s internal document, “Toyota Way.”
For whatever reason, PCB fabricators as a whole have yet to truly embrace the Lean manufacturing philosophy that has permeated OEM and EMS factories. My clients often push back; contending that Lean is just another “flavor of the month” quality initiative that will soon fall by the wayside. They ask, “If I am providing product on-time and of a high quality, why should I care about Lean?” My answer is simple: price and flexibility. The former is about dollars (and by the way, it’s always about the dollars). One way or another, your customers are paying for your process inefficiencies. The latter is about lead-time. In the highly dynamic environment that we all play in today, one of the major drivers is flexibility, and the biggest constraint on flexibility is lead-time.
The opening quote captures the values and ideals of Taiichi Ohno, one of the inventors of the Toyota Way that were tasked with transforming Toyota into the world-class manufacturing enterprise that it is today. This column is intended to provide an overview of Lean and the potential benefits of it as a differentiator.
Read the full column here.
Editor's Note: This column originally appeared in the January 2014 issue of The PCB Magazine.
More Columns from The Right Approach
The Right Approach: ‘Twas the Night Before Christmas (Harley-style)The Right Approach: I Hear the Train A Comin'
The Right Approach: Culture Change is Key to a QMS
The Right Approach: Leadership 101—Be a Heretic, Not a Sheep
The Right Approach: Leadership 101—The Law of Legacy
The Right Approach: Leadership 101: The Law of Explosive Growth
The Right Approach: Leadership 101—The Law of Timing
The Right Approach: The Law of Sacrifice