Estimated reading time: 5 minutes
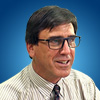
The Sales Cycle: China; From the Inside
Editor's Note: This column originally appeared in the June 2012 issue of The PCB Magazine.In past columns I have written about the economic war with China and the trap we have set for ourselves. But the battle isn't just for low-cost products being produced and shipped back to America, but also for access to the very large and fast-growing domestic market in China. As suppliers to PCB fabricators and assemblers worked to gain market share in China, they faced many challenges, including cultural issues, infrastructure, employees, language, kickbacks, corruption, and others. The most common approach to overcoming these challenges was to ink a deal with a large distributor. One well-known distributor is WKK Distribution (WKKD).
WKKD is part of Wong's Kong King Group (WKK), which has been serving the global market for nearly 35 years. WKKD distributes many products to the PCB fabrication and assembly markets from suppliers around the world. Products include consumables and equipment. If you have ever visited the WKKD booth at an industry trade show in China, you understand the company’s depth of coverage. One thing that has changed, due to market demands in recent years, is WKKD’s approach to the distribution market. Not only is the company representing and selling the equipment of its principals, but WKKD is now manufacturing several lines for its principals as well.
One issue debated over the years is the ability of the Chinese to produce high-quality equipment. Hamed El-Abd, president of WKKD, will be the first to explain that they—the Chinese—can, and WKKD now offers several lines to prove that fact. That being said, we all know the high-quality standard the Japanese demand, and to now see some of Yamaha’s equipment being produced by WKK Donguang Manufacturing certainly speaks to the capabilities of the Chinese and WKK.
The other side of Chinese manufacturing so often called into question is working conditions. During a recent visit I sat down for an in-depth interview about China with Hamed, and when I broached this issue he invited me to tour his company’s factory in Guangdong. With all of the ongoing news coverage of working conditions at other EMS companies in that region, I decided to go have a look at what was going on at WKK.
Though WKK is small in comparison to Foxconn, the company’s facility is still much like a small city, with an infrastructure that includes a power-generation facility, fire station, health clinic, barber shop, food store, library, and a restaurant that feeds more than 5,000 employees daily. Aside from that, recreation facilities include basketball courts, roller rinks, a movie theater, and other amenities for employees’ comfort. Granted, this is not a resort, but for many employees it is a very comfortable environment compared to their lives before WKK. WKK employs thousands of people and also offers dormitories that house nearly 5,000 of those workers.
Upon our arrival, we were first taken to a special security area where we signed in and were asked to wash our hands. This procedure was first implemented when SARS was rampant in China several years ago. A factory could easily be brought to its knees if a contagious disease such as SARS were introduced into the workforce. After the sign-in process, we made our way into the main lobby for a very warm welcome.
The tour began with a walk though the engineering, quality, and admin offices—all what you would expect: People at desks working at their computers and such. From there we moved into the manufacturing areas, though some areas were off-limits due to confidentiality agreements. The areas we were able to tour included plastics fabrication, dry film processing, some assembly, extruding processing, and the equipment manufacturing area. In each area, the manager greeted us and gave us detailed explanations of their processes and answered our questions. The pride of each person was very apparent.
I asked our tour guides Stephen To, general manager of New Product Development, and Johnson Fok, general manager of WKK Donguang Manufacturing, about the employees’ work hours and compensation. They explained that a typical day is comparable to the work schedule in America. The worker is paid at least the minimum wage, which is set by the local government; I think it is approximately RMB 1,800 or US $250 per month. That doesn’t sound like much, and by our standard it isn’t, but in that region of the world it seems to be a competitive wage. If an employee works overtime, he can earn time and a half.
One thing I kept hearing throughout the tour is how committed Senta Wong, chairman and CEO of Wong Kong King Group, is to the employees. His goal is to take great care of the people and make sure they are happy in their jobs; this substantially reduces employee turnover, which improves overall product quality. Perhaps this is a unique approach in China, but as we toured the factory, there was evidence of this philosophy everywhere. During our tour we were invited to lunch at the company's dining facility and I was quite impressed with the quality of the food.
To help keep meal costs down, not all of the food is purchased from local suppliers. Some is actually produced in-house, such as the tofu. We toured the bean curd processing area. Here the soy beans are processed into tofu. Not only does this help keep costs down, but it also increases the quality of the food served. Food costs can easily get out of control when you are feeding 5,000+ people daily. Another measure to help reduce costs can be found in the food serving process. Three lines are available to employees, based on how hungry they are—from “not too hungry” to “very hungry.” By controlling portions based on appetite, waste is reduced.
As the pressures to increase human standards in China continue, it looks like WKK is well ahead of the curve and may be a model for others. I do realize there are other companies in China that are the polar opposite of what WKK has created and that is the image the news media paints for the world. It’s just nice to know that there are companies in China that do understand the value of their employees and work to provide an exceptional working environment. It may not be perfect, but at least they’re trying.