-
- News
- Books
Featured Books
- pcb007 Magazine
Latest Issues
Current IssueInventing the Future with SEL
Two years after launching its state-of-the-art PCB facility, SEL shares lessons in vision, execution, and innovation, plus insights from industry icons and technology leaders shaping the future of PCB fabrication.
Sales: From Pitch to PO
From the first cold call to finally receiving that first purchase order, the July PCB007 Magazine breaks down some critical parts of the sales stack. To up your sales game, read on!
The Hole Truth: Via Integrity in an HDI World
From the drilled hole to registration across multiple sequential lamination cycles, to the quality of your copper plating, via reliability in an HDI world is becoming an ever-greater challenge. This month we look at “The Hole Truth,” from creating the “perfect” via to how you can assure via quality and reliability, the first time, every time.
- Articles
- Columns
- Links
- Media kit
||| MENU - pcb007 Magazine
Estimated reading time: 5 minutes
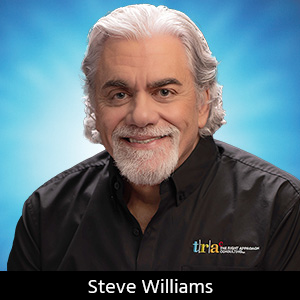
Point of View: RoHS: Six Years After
Editor's Note: This article originally appeared in the October 2012 issue of The PCB Magazine.
Background
By now, the definition of RoHS is probably not needed, but nonetheless, here it is: RoHS (Reduction of Hazardous Substances) is a European Directive on the restriction of certain hazardous substances in electrical and electronic equipment. The move to lead-free was driven by the Japanese, but the legislation was driven by the EU (European Union). Just who is the EU? For reference purposes, Table 1 shows the current member states that make up the EU. As of July 1, 2006, new electrical and electronic equipment entering the EU market cannot contain lead, mercury, cadmium, hexavalent chromium, polybrominated biphenyls (PBB) or polybrominated diphenyl ethers (PBDE), specifically Penta PBDE and Octa PBDE. “Restricted” substances are sometimes interpreted as “banned,” but this is not technically correct as minimal levels of some of these substances are actually allowed. Table 2 lists these substances and the maximum allowable limits for each.
Table 1: European Union membership.
Table 2: Restricted substances and limits.
PCB Impact I
The biggest area of confusion is with the flame-retardant used in the manufacture of raw PCB laminates. The leading flame-retardant used in laminate is Tetrabromobisphenol-A (TBBPA), which does not (currently) fall under the restrictions of RoHS and is not currently restricted in any country in the world. The reason I stress currently is that there is still industry concern that TBBPA may become included at some point as numerous factions outside the electronics industry continue to lobby for this, even though science has proven TBBPA to be safe for human health and the environment.
The WEEE Factor
As if this whole lead-free issue isn’t complicated enough, we have to factor in the WEEE (Waste of Electrical and Electronic Equipment) initiative. Simply put, this directive deals with manufacturers’ requirement to properly dispose of the waste from electrical and electronic equipment, the EEE of WEEE. Although originally restricting all BFRs (brominated flame-retardants), recent legislation has been revised to calibrate with RoHS, only prohibiting PBB and PBDE. Many companies now hold an annual E-waste day, where employees are encouraged to bring in their old and obsolete electronics for proper disposal. This is, of course, an offshoot of this legislation.
PCB Impact II
So if the flame-retardant used in PCB laminates is not restricted, there is no impact on us, right? Wrong! The lead-free initiative affects the entire supply chain, and the trickle-down effect means that PCB manufacturers cannot use surface finishes containing lead, and that EMS providers may no longer use lead solder for assembly. The old adage has never been so true: “Nothing solders like solder.” The new solder alloys require a much higher temperature, typically a 260°C peak, and raw PCBs must now withstand multiple thermal excursions at this elevated temperature. New laminates need to have improved thermal mechanical properties to survive lead-free processing, from the standpoint of both infant mortality and long-term reliability.
PCB Impact III
The final impact, starting with the PCB and continuing throughout the supply chain, is cost. Lead-free is anything but free! The hard costs will be in solder, PCBs (both from a laminate and process aspect), assembly, and final product. For example, new alloy solder costs will be anywhere from 2-3x the price of standard Sn63/Pb37 tin-lead. Soft costs will include retraining the entire industry on processing, and more importantly, inspection. Lead-free solders do not look or act the same. They are no longer “bright and shiny,” which has been the long standing visual rule of thumb for inspection. The solder does not flow, wick and cover as well, so what was once a defective solder joint may not be the case any longer. Extensive retraining costs are being incurred for process changes and inspection criteria, requiring inspection calibration sessions between suppliers and customers throughout the supply chain.
Companies are also reporting increased costs for staffing, legal, IT, and marketing (to spread the word of their RoHS-compliant products). There is also a significant cost to OEMs and EMS providers to scrub BOMs and identify RoHS-compliant alternatives for existing components.
Reliability Concerns
- Unproven RoHS alternatives: In many cases, electronic component manufacturers could not find proven RoHS alternatives for restricted materials, and while various manufacturers have been using different RoHS materials and strategies, few have proven better than non-RoHS components. Increasing this concern is the fact that Exemption 7c, which allows certain components to contain lead, expires December 31, 2012
- Effects of higher-temperature soldering: Elevated soldering temperature leads to component life reduction, thermal fatigue, plastic IC popcorn effect, delamination of multi-layer PCBs, etc
- Solder Joint Reliability: Reliability of solder joints becomes questionable, with many researchers finding the long-term solder joint reliability is less than tin/lead solder paste
- Tin Whiskers: A whisker can cause a PCB short, and this is a very serious issue because many component manufacturers are using pure tin as their preferred lead finish to reduce cost
- Environmental Impact: Some of the RoHS-compliant alternate materials and processing by-products are actually more harmful to the environment than the small level of lead they replaced would have been
Why Is RoHS Necessary?
What a great question! The position statement of the IPC Board of Directors states:
“The US electronic interconnection industry, represented by the IPC, uses less than 2% of the world's annual lead consumption. Furthermore, all available scientific evidence and US government reports indicate that the lead used in US printed circuit board (PCB) manufacturing and electronic assembly produces no significant environmental or health hazards.”
So, six years later we have to ask ourselves: “Has force-feeding RoHS to the electronics industry made a significant net-positive impact?” I would argue that it has not.
And while, from a big-picture perspective, eliminating lead is probably a good thing, but given the above statistics and other lead-intensive industries out there, are we getting the biggest bang for our buck by targeting the electronics industry?
From my point of view, the answer is no.
Steven Williams is a 35-year veteran in the electronics industry and an authority on manufacturing and management. He is currently the commodity manager for a large global EMS provider, a distinguished faculty member at several universities and author of the book Survival Is Not Mandatory: 10 Things Every CEO Should Know About Lean.
More Columns from The Right Approach
The Right Approach: ‘Twas the Night Before Christmas (Harley-style)The Right Approach: I Hear the Train A Comin'
The Right Approach: Culture Change is Key to a QMS
The Right Approach: Leadership 101—Be a Heretic, Not a Sheep
The Right Approach: Leadership 101—The Law of Legacy
The Right Approach: Leadership 101: The Law of Explosive Growth
The Right Approach: Leadership 101—The Law of Timing
The Right Approach: The Law of Sacrifice