-
- News
- Books
Featured Books
- pcb007 Magazine
Latest Issues
Current IssueInventing the Future with SEL
Two years after launching its state-of-the-art PCB facility, SEL shares lessons in vision, execution, and innovation, plus insights from industry icons and technology leaders shaping the future of PCB fabrication.
Sales: From Pitch to PO
From the first cold call to finally receiving that first purchase order, the July PCB007 Magazine breaks down some critical parts of the sales stack. To up your sales game, read on!
The Hole Truth: Via Integrity in an HDI World
From the drilled hole to registration across multiple sequential lamination cycles, to the quality of your copper plating, via reliability in an HDI world is becoming an ever-greater challenge. This month we look at “The Hole Truth,” from creating the “perfect” via to how you can assure via quality and reliability, the first time, every time.
- Articles
- Columns
- Links
- Media kit
||| MENU - pcb007 Magazine
Estimated reading time: 4 minutes
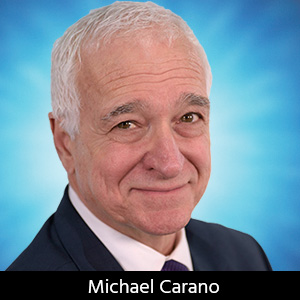
Contact Columnist Form
Trouble in Your Tank: Interconnect Defect (ICD): Getting to the Root Cause
Editor's Note: This article originally appeared in the September 2012 issue of The PCB Magazine.
Introduction
Circuit board fabricators and end-users are always concerned about innerplane separation, or innerconnect defect, which is a separation of the electroless copper deposit from the innerlayer copper face. Of course, there are other types of separation that can be encountered. It is well known that the electrolytic copper may separate from the electroless copper, but the electroless copper remains on the interconnect, referred to as type 2 ICD. Type 1 references the electroless copper separating from the innerconnect post or innerplane. There is a third type in which the electroless copper deposit actually separates from itself. This is more like a cohesive failure within the deposit. Type 3 is very difficult to detect and requires excellent microsectioning and polishing techniques to properly detect and trouble shoot.
Shown in Figure 1 is an example of an ICD.
Figure 1: Typical ICD or innerplane separation
Certainly, an ICD is not confined to just the interplane. Blind vias can also exhibit a separation of the plated copper from the capture pad. This will be investigated in a future column of Trouble in Your Tank.
First, what can one expect from this type of defect? What does it look like under the microscope?
Well, one can expect that innerconnect defect (IP separation or ICD) generally exhibits these underlying characteristics: [1]
- Occurs during the stress of thermal shocks such as soldering. This produces expansion in the Z-axis and places strain on the copper in the hole wall.
- Most often seen on the first innerlayer from either side of the board. (i.e., in a 12-layer board, the defect is seen on layers 2 and 11)
- The weakest bond breaks first.
- Under-cured boards are most susceptible.
- Affected by board construction, PWBs with more resin, less copper, lower Tg materials, tend to show more expansion in the Z-axis.
- ICDs are often accompanied by hole wall pull away, but not always.
Understand that innerplane separation has many causes. This is what makes this defect so difficult to pinpoint and eliminate. And to confuse the issue further, one must first determine which of the three types of IP separation it is.
Now, before we dive into this case study where you can test your troubleshooting diagnostic skills, we need to get a close look, in general terms, at what type 2 and type 3 ICD look like.
Figure 2: ICD type 1—electroless copper separates from the post, confirmed with etch.
Figure 3: ICD type 2—electrolytic copper separates from the electroless copper.
Figure 4: ICD type 3—cohesive failure of the electroless copper deposit.
Case Study
So it begins. The fabricator believes there are some issues with ICDs but he is not certain. No other diagnostic tests were performed as the boards in question (other than having solder float coupons) did not have any IST coupons that could be tested.
The boards in question were approximately 230-mil thick panel, 20-mil holes, ½ oz innerlayers.
An example of the microsection is shown below in Figure 5.
Figure 5: Note not only the ICD, but the torn-out glass fiber bundles as well.
What does the troubleshooter conclude from this, other than an innerplane separation?
Well, to begin with, one needs to perform additional analysis. The glass bundle issue raises some concern. Let’s look further.
Figure 6: Actual section (bottom) and EDAX scan (top).
The analysis focused on the gap or open area in the section above. The EDAX analysis gives a higher than normal level of silicon and aluminum. This is drill debris that has been embedded into the epoxy resin. Again, the clue was the glass fiber bundle issue noted on the cross section.
Figure 7: Another look at the separation-EDAX scan again shows a high level of silicon and aluminum in the defect area.
In Figure 7, there is evidence of nail heading. Again, this is further evidence that the defect in this case is related to the drilling operation.
Finally one more piece of evidence to consider. Look at the cross sections below:
Figure 8: Top shows severe plowing of the copper innerlayer (note copper folded over on itself) and bottom shows embedded glass fibers and drill debris.
Since the drilling operation generates significant heat as it is, it is not uncommon for drill debris to become embedded in the resin.
Summary
In this case, the cause of the ICD was clearly unrelated to the plating or desmear operation. Drilling problems as shown by the evidence here lead to the team optimizing the drilling parameters, including feeds and speeds, SFM, and being more vigilant with respect to drill-bit quality.
References:
1. IPC PE-740 Process Effects Guide.
Michael Carano is with OMG Electronic Chemicals (formerly Electrochemicals), a developer and provider of processes and materials for the electronics industry supply chain. He has been involved in the PWB, general metal finishing photovoltaic industries for nearly 30 years. Carano holds nine U.S. patents in topics including plating, metallization processes and PWB fabrication techniques.
More Columns from Trouble in Your Tank
Trouble in Your Tank: Metallizing Flexible Circuit Materials—Mitigating Deposit StressTrouble in Your Tank: Can You Drill the Perfect Hole?
Trouble in Your Tank: Yield Improvement and Reliability
Trouble in Your Tank: Causes of Plating Voids, Pre-electroless Copper
Trouble in Your Tank: Organic Addition Agents in Electrolytic Copper Plating
Trouble in Your Tank: Interconnect Defect—The Three Degrees of Separation
Trouble in Your Tank: Things You Can Do for Better Wet Process Control
Trouble in Your Tank: Processes to Support IC Substrates and Advanced Packaging, Part 5