-
- News
- Books
Featured Books
- pcb007 Magazine
Latest Issues
Current IssueInventing the Future with SEL
Two years after launching its state-of-the-art PCB facility, SEL shares lessons in vision, execution, and innovation, plus insights from industry icons and technology leaders shaping the future of PCB fabrication.
Sales: From Pitch to PO
From the first cold call to finally receiving that first purchase order, the July PCB007 Magazine breaks down some critical parts of the sales stack. To up your sales game, read on!
The Hole Truth: Via Integrity in an HDI World
From the drilled hole to registration across multiple sequential lamination cycles, to the quality of your copper plating, via reliability in an HDI world is becoming an ever-greater challenge. This month we look at “The Hole Truth,” from creating the “perfect” via to how you can assure via quality and reliability, the first time, every time.
- Articles
- Columns
- Links
- Media kit
||| MENU - pcb007 Magazine
Estimated reading time: Less than a minute
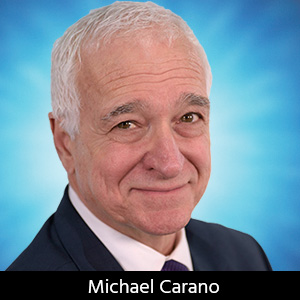
Contact Columnist Form
Trouble in Your Tank: PTH Voids: Getting to the Root Cause, Part 2
Introduction
While there are many causes for PTH voids, one should also consider poor drilling practices, multilayer lamination issues and the fact that higher performance resin materials are more difficult to desmear, all of which can lead to voids.
In Part 1 of this series, I approached the subject of PTH voids at the root cause as attributable to the difficulty of desmearing the more chemically resistant, high-performance laminate materials. In addition to the greater chemical resistance, these materials also present challenges with respect to drill debris that can lodge in the hole wall, and multilayer lamination challenges.
Debris
Debris remaining in the hole may become loosened later in the fabrication process, leading to a void within the via. Debris is typically caused by poor evacuation of drill chip particles. The vacuum on the drill machine is designed to remove debris from the through holes. Obviously, if the vacuum is insufficient, it is not uncommon for debris to remain. Proper selection of drilling feeds and speeds, drill retraction rates and sufficient vacuum will ensure reasonably clean vias.
Editor's Note: This article originally appeared in the July 2013 issue of The PCB Magazine.
More Columns from Trouble in Your Tank
Trouble in Your Tank: Metallizing Flexible Circuit Materials—Mitigating Deposit StressTrouble in Your Tank: Can You Drill the Perfect Hole?
Trouble in Your Tank: Yield Improvement and Reliability
Trouble in Your Tank: Causes of Plating Voids, Pre-electroless Copper
Trouble in Your Tank: Organic Addition Agents in Electrolytic Copper Plating
Trouble in Your Tank: Interconnect Defect—The Three Degrees of Separation
Trouble in Your Tank: Things You Can Do for Better Wet Process Control
Trouble in Your Tank: Processes to Support IC Substrates and Advanced Packaging, Part 5