-
- News
- Books
Featured Books
- pcb007 Magazine
Latest Issues
Current IssueInventing the Future with SEL
Two years after launching its state-of-the-art PCB facility, SEL shares lessons in vision, execution, and innovation, plus insights from industry icons and technology leaders shaping the future of PCB fabrication.
Sales: From Pitch to PO
From the first cold call to finally receiving that first purchase order, the July PCB007 Magazine breaks down some critical parts of the sales stack. To up your sales game, read on!
The Hole Truth: Via Integrity in an HDI World
From the drilled hole to registration across multiple sequential lamination cycles, to the quality of your copper plating, via reliability in an HDI world is becoming an ever-greater challenge. This month we look at “The Hole Truth,” from creating the “perfect” via to how you can assure via quality and reliability, the first time, every time.
- Articles
- Columns
- Links
- Media kit
||| MENU - pcb007 Magazine
Estimated reading time: 1 minute
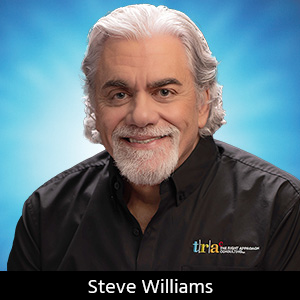
Best Practices 101, Part 2
A few months ago, Best Practices 101, Part 1 (May, 2014) was rolled out, focusing on process analysis as the first step in this process. This issue will discuss another powerful tool at our disposal: Value stream mapping.
“But we already made a process flowchart--isn’t that good enough?”
In a word, no. Process flow diagrams are a great first step, but they don’t tell the entire story. Value stream maps add one critical ingredient that standard process flowcharts don’t have: Time. Process flowcharts, whether drawn by hand or electronically, do not capture this important element. They simply present a snapshot of the sequence of steps in the process. Time is essential to understanding how one operation affects another and where your resources are being spent.
Value Stream Mapping
A value stream map (VSM) takes the basic flowchart to the next level, kind of like a process flowchart on steroids. In addition to the basic action boxes with arrows showing the flow of work, a lot of other information is added, including material and information flow, operating parameters, process lead-times, inventory, a timeline depicting value-added time relative to non-value added time, and so on. Value stream mapping is the single most effective major process analysis step to identify the value stream, and conversely, the non-value waste in your processes. The value stream is the set of all of the specific actions and activities required from the beginning of a process to the end of a process. Imagine a long and winding deep blue stream flowing through cities, counties, and states. Next, visualize all the things that the river carries within it: water, fish, minerals, plants, and a thousand other elements that combine to form the stream. Processes are very much like a stream; they flow in a natural direction and carry materials and information within them from one point to another.
Editor's Note: This column originally appeared in the September 2014 issue of The PCB Magazine.
More Columns from The Right Approach
The Right Approach: ‘Twas the Night Before Christmas (Harley-style)The Right Approach: I Hear the Train A Comin'
The Right Approach: Culture Change is Key to a QMS
The Right Approach: Leadership 101—Be a Heretic, Not a Sheep
The Right Approach: Leadership 101—The Law of Legacy
The Right Approach: Leadership 101: The Law of Explosive Growth
The Right Approach: Leadership 101—The Law of Timing
The Right Approach: The Law of Sacrifice