-
- News
- Books
Featured Books
- pcb007 Magazine
Latest Issues
Current IssueInventing the Future with SEL
Two years after launching its state-of-the-art PCB facility, SEL shares lessons in vision, execution, and innovation, plus insights from industry icons and technology leaders shaping the future of PCB fabrication.
Sales: From Pitch to PO
From the first cold call to finally receiving that first purchase order, the July PCB007 Magazine breaks down some critical parts of the sales stack. To up your sales game, read on!
The Hole Truth: Via Integrity in an HDI World
From the drilled hole to registration across multiple sequential lamination cycles, to the quality of your copper plating, via reliability in an HDI world is becoming an ever-greater challenge. This month we look at “The Hole Truth,” from creating the “perfect” via to how you can assure via quality and reliability, the first time, every time.
- Articles
- Columns
- Links
- Media kit
||| MENU - pcb007 Magazine
An Optical Update with TTM
April 16, 2015 | Barry Matties, I-Connect007Estimated reading time: 6 minutes
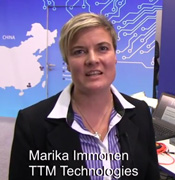
I recently met with Marika Immonen, manager of R&D optical interconnects at TTM Technologies. We last spoke one year ago. This time, we discussed the optical project that Marika's been leading, as well as the future of optical technology in the PCB industry.
Matties: Thanks for joining me today, Marika. Last year we had a chance to talk about the optical project you have been managing for TTM. Can you start by giving us a quick update on your progress?
Immonen: In the past year, we've managed to scale up the optical PCB fabrication from small scale to realistic form factors. We're currently running a pilot line, capable of handling 16- to 20-inch panels with optical layers. We have made significant developments to support various optical connectors, to pass light in and out of the board.
Matties: Tell us just a little bit about what the basic technology is and how it applies to a board fabricator.
Immonen: Obviously, we know that increasing data rates are pushing copper to extremes. We know 25 Gbps is coming and OEMs are considering even beyond that. Over the past months we've seen increasing interest from various customers to look at the optical alternative. Optical engine products have already pushed optics inside systems, but we develop the next step further and integrate optical layers as part of the PCB itself.
This is what we are showing this year with our partners FCI and Dow Corning: a fully built end-to-end optical link on standard multilayer PCB with 25 Gbps optical engines feeding embedded waveguides terminated by waveguide connectors on both ends. Customers are interested in the mixing of copper and optical technology involving embedded optical signal traces, and our integrated solution provides copper and optical all-in-one. This solution eliminates cables running on top of your card, which is what you see in current optical products and passive waveguide cables in the market.
The board fabricator obviously faces several new challenges in terms of material set, alignment accuracy requirements, compliance with processes and standard board materials, and new testing procedures. The process window in many critical steps is narrower than in standard steps. Yet, we want to utilize the current process infrastructure for cost and compliance. We have built capabilities to achieve this with our factory teams starting from day one, so scaling in volumes is a smaller step versus those who have started with specialized labs for optical parts.
Matties: What sort of advantage does that offer?
Immonen: We provide lower-loss channels, which is particularly an issue with the longer traces. There are no EMI problems with the optical channels nor issues with thermal management. You're able to have denser lines on your tracing layout, so you're able to reduce real estate on board by a factor of 4 to 6.
Matties: How fast can it go?
Immonen: Speed is only one metric; bandwidth density and aggregate throughput are the key factors for optics. Higher channel density and count within the same board space, even with 10, 25 or 40 Gbps per channel, gives you terabit capacity links. Multiplexing adds capacity even further. Also, reducing the layer count—if I had one optical layer, reduced from, say, six signal layers—will reduce your overall cost, thickness, and your materials.
Matties: Are there practical applications? Is this already being applied in the real world?
Immonen: Not yet. We're running multiple customer product programs and evaluating prototype programs, besides working through large consortium programs. Customers are coming from areas such as routing and switching applications, as well as storage applications. Supercomputing obviously uses a lot of optics, but that is a niche business.
Matties: You said reducing layer count from six to one is something you're shooting for, but what is the optimal right now, that you're really comfortable that people can rely on? Is six to one the target?
Immonen: That's realistic, because we can push much more data from that one pipe of optical channel and have many in parallel, less than 100 microns apart. Obviously, when you increase frequency, your copper transmission lines need to be wider apart and you need more space in the electrics, so optical is able to provide you densities that are easily 6x the standard copper traces.
Matties: I understand. What sort of customers are interested in this? Is it primarily telecommunications?
Immonen: Conventional telecommunications, yes, but more and more it is the exponential growth of cloud applications and huge data centers. These centers are extending in size and consume more power to run. The trend is towards distributed and disaggregated systems. That means your computing and memory are physically separated, for instance, in different racks. Then you need high-speed low-latency communication links between them that are only viable by optical means.
Matties: Are there any other competitors to this technology that you're aware of?
Immonen: There are some small, specialized companies, but regarding what TTM specifically focuses on – the high volumes – due to costs and constraints, you have less competition. The ultimate decision is made based on comparison costs to existing mature technology, so we need to be cost-competitive – and to be honest, in that regard there are not yet many, if any, high-volume PCB fabricators with optical PCB products.
Matties: Do you consider this a disruptive technology?
Immonen: It's definitely disruptive. What that means is that, to start with, you need robust technical building blocks including optical waveguides, supporting connectors and transceiver engines to build the functional link within a system. But besides that, designer needs EDA-compliant design tools readily available, design guidelines to easily understand how he can use the optics. The process team requires new testing infrastructures and qualification procedures in factory, and finally we have to provide long term reliability testing data to show evidence of robustness. Otherwise, the customer cannot validate decision of implementation.
Matties: So this is a high-end market application. Do you see it moving down over time?Page 1 of 2
Testimonial
"Our marketing partnership with I-Connect007 is already delivering. Just a day after our press release went live, we received a direct inquiry about our updated products!"
Rachael Temple - AlltematedSuggested Items
Trouble in Your Tank: Minimizing Small-via Defects for High-reliability PCBs
08/27/2025 | Michael Carano -- Column: Trouble in Your TankTo quote the comedian Stephen Wright, “If at first you don’t succeed, then skydiving is not for you.” That can be the battle cry when you find that only small-diameter vias are exhibiting voids. Why are small holes more prone to voids than larger vias when processed through electroless copper? There are several reasons.
The Government Circuit: Navigating New Trade Headwinds and New Partnerships
08/25/2025 | Chris Mitchell -- Column: The Government CircuitAs global trade winds continue to howl, the electronics manufacturing industry finds itself at a critical juncture. After months of warnings, the U.S. Government has implemented a broad array of tariff increases, with fresh duties hitting copper-based products, semiconductors, and imports from many nations. On the positive side, tentative trade agreements with Europe, China, Japan, and other nations are providing at least some clarity and counterbalance.
How Good Design Enables Sustainable PCBs
08/21/2025 | Gerry Partida, Summit InterconnectSustainability has become a key focus for PCB companies seeking to reduce waste, conserve energy, and optimize resources. While many discussions on sustainability center around materials or energy-efficient processes, PCB design is an often overlooked factor that lies at the heart of manufacturing. Good design practices, especially those based on established IPC standards, play a central role in enabling sustainable PCB production. By ensuring designs are manufacturable and reliable, engineers can significantly reduce the environmental impact of their products.
50% Copper Tariffs, 100% Chip Uncertainty, and a Truce
08/19/2025 | Andy Shaughnessy, I-Connect007If you’re like me, tariffs were not on your radar screen until a few months ago, but now political rhetoric has turned to presidential action. Tariffs are front-page news with major developments coming directly from the Oval Office. These are not typical times. President Donald Trump campaigned on tariff reform, and he’s now busy revamping America’s tariff policy.
Global PCB Connections: Understanding the General Fabrication Process—A Designer’s Hidden Advantage
08/14/2025 | Markus Voeltz -- Column: Global PCB ConnectionsDesigners don’t need to become fabricators, but understanding the basics of PCB fabrication can save you time, money, and frustration. The more you understand what’s happening on the shop floor, the better you’ll be able to prevent downstream issues. As you move into more advanced designs like HDI, flex circuits, stacked vias, and embedded components, this foundational knowledge becomes even more critical. Remember: the fabricator is your partner.