-
- News
- Books
Featured Books
- pcb007 Magazine
Latest Issues
Current IssueInventing the Future with SEL
Two years after launching its state-of-the-art PCB facility, SEL shares lessons in vision, execution, and innovation, plus insights from industry icons and technology leaders shaping the future of PCB fabrication.
Sales: From Pitch to PO
From the first cold call to finally receiving that first purchase order, the July PCB007 Magazine breaks down some critical parts of the sales stack. To up your sales game, read on!
The Hole Truth: Via Integrity in an HDI World
From the drilled hole to registration across multiple sequential lamination cycles, to the quality of your copper plating, via reliability in an HDI world is becoming an ever-greater challenge. This month we look at “The Hole Truth,” from creating the “perfect” via to how you can assure via quality and reliability, the first time, every time.
- Articles
- Columns
- Links
- Media kit
||| MENU - pcb007 Magazine
Estimated reading time: 3 minutes
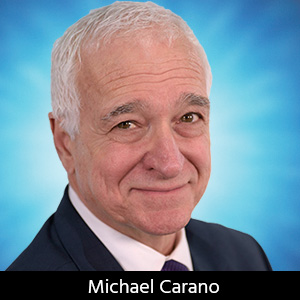
Contact Columnist Form
More Pesky Solder Mask Problems: Plugged Via Leading to Skip Plating
Many factors are in play when it comes to preventing ink from remaining in vias. Two factors are presented here, and include phototool quality, the concept of D-min and D-max and optimal set-up of the developing step. I am sure you have seen it, but may not have been sure of the root cause: solder not flowing in the vias and the lack of a plated solderable finish in the vias. Some of the vias have a final finish in them and others do not, and all of these happening on the same boards!
A closer examination yields solder mask ink remaining in the vias, resulting in what is essentially a plugged or partially plugged via. Some of the ink may also be present on the on the pads surrounding the vias. This is not a pleasant situation and there is never an obvious fix, though you may be inclined to think so. After all, there is ink in the holes and it is not supposed to be there! The key is to not leave it there in the first place. However, it is not that simple.
Getting to the Root Cause
It would be easy to just start pointing fingers either at the soldermask operation or the metallic etch resist process. Clearly something is preventing the deposition of the solderable finish into the via and on the pads.
There are several causes for the issue shown in Figure 1. As a troubleshooter, one must consider the following processes and properties:
• Viscosity and solids content of the LPI ink
• Excessive tack dry time and temperature
• Over exposure and/or under developing
• Phototool quality
Viscosity and solids content of the ink can be an issue with respect to ink remaining in the holes (especially smaller diameter vias). When adjusting the viscosity of the ink, ensure that a sufficient amount of solvent is added to the ink. Under-adding of the solvent will increase the solids content and adversely affect the viscosity.
If the material is too viscous, there will be excess ink in the vias, therefore increasing the difficulty of complete removal. Mask suppliers will provide a thinner to adjust the ink viscosity. Interestingly, there is a greater chance that holes can remain plugged with double-sided screen printing as opposed to either curtain coating or spray coating of the ink.
The principal of double-sided screen printing is embodied in the functional aspect of the screen printing equipment that allows for the coating of both sides of the printed circuit board simultaneously (Figure 2). The screens are fixed at the same distance from both sides of the board. There are also squeegees in the same noted with either spray or curtain coating of soldermasks.
While additional ink in the holes is a given with double-sided screen coating technology, excessive tack dry time and temperature is of equal concern. By over-drying, the ink has a much greater chance of solidifying in the via, making the ink plug more difficult to develop away.
Subsequently, that brings us to the issue of phototool quality and the exposure/developing process steps. The phototool has two particular features that should be evident. There is the clear area that allows UV light to pass through and the opaque or darkened areas designed to prevent the light from passing. Where the light is able to pass, the ink will undergo polymerization. And that’s where the concept of D min and D max show up: the optical density of the clear and opaque areas of the phototool.
The reader should also familiarize herself with the term densitometer. Proper mastery of this instrument will help to ensure optimum quality of the phototool. D-min is a measure of the tool to transmit light. The lower the number, the greater the transmission. And that is what the engineer wants, maximum transmission of the UV through clear area of the tool. Dmax, on the other hand, is a measure of image area on the tool and its ability to block the UV light. The densitometer, thus, is an instrument that is used to measure and track the D-min and D-max attributes of the phototool. This concept is introduced here for one reason; as the D-max decreases (or is not high enough from the beginning) there is a greater chance for UV light to penetrate the tool and cause partial or complete exposure of the ink. This would then cause difficulty when trying to develop out the ink from the holes. There is also the chance that some of the ink may be exposed on the pads, which can then lead to non-conformance.
Editor's Note: This article originally appeared in the March 2015 issue of The PCB Magazine
More Columns from Trouble in Your Tank
Trouble in Your Tank: Metallizing Flexible Circuit Materials—Mitigating Deposit StressTrouble in Your Tank: Can You Drill the Perfect Hole?
Trouble in Your Tank: Yield Improvement and Reliability
Trouble in Your Tank: Causes of Plating Voids, Pre-electroless Copper
Trouble in Your Tank: Organic Addition Agents in Electrolytic Copper Plating
Trouble in Your Tank: Interconnect Defect—The Three Degrees of Separation
Trouble in Your Tank: Things You Can Do for Better Wet Process Control
Trouble in Your Tank: Processes to Support IC Substrates and Advanced Packaging, Part 5