High-Density Interconnects: Enabling the Intelligence of Things
May 13, 2015 | William Beckenbaugh, Ph.D. and Joan K. Vrtis, Ph.D., Multek Technologies LtdEstimated reading time: 2 minutes
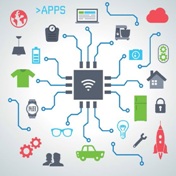
The rapid evolution of high-density interconnects printed circuit board (HDI PCB) technologies over the last five years has been accelerated largely by the mass production demands for global deployment of 3G and 4G mobile phone products at attractive consumer pricing. The major capacity expansions in Asia factories has allowed circuit shipments at the highest volumes and quality levels yet experienced since the invention of the circuit board in the 1950s.
As the Internet of Things (IoT) spawns new intelligent connected platforms (IP) for sensing and control products such as wearable electronics, home automation, and medical monitoring, HDI processing is being applied to rigid-flexible printed circuits (RFPC) and multilayer flexible printed circuits (FPCs), modified in new ways to achieve mechanical, physical, and chemical exposure robustness and low latency communication to the cloud. The purpose of this article is to explore the key requirements and new approaches required for the application of HDI, especially stacked, copper-filled microvia processing of thinner, low-loss materials, to achieve the routing and solder joining capabilities required by advanced surface mount technology and final assembly techniques dictated for leading edge semiconductor component packaging densities.
Background
Beginning in the 1980s, the electronics industry began the early days of transition from pin-in-hole wave soldering to surface mounting of increasingly complex semiconductor packages. Strategic technical analysts at companies such as IBM, Bell Labs (Western Electric), Digital Equipment, Hitachi, NEC, and Hewlett Packard realized the existing PCB processes and materials faced an impending industry-wide capability bottleneck with urgent implications in limiting copper trace and solder pad featuring. From this exigency came the industry-wide invention of a continuing variety of microvia processes and production systems that continues to this day. Today, the copper filled, stacked laser drilled microvia multilayer process is the dominant in global production.
In a parallel but separate roadmap, the flexible circuit has evolved since its inception as an early alternative to cabling and power distribution. Flexible printed circuits evolved quickly in the early 1980s to become the dominant form factor for very fine-pitch semiconductor packaging substrates and liquid crystal display interconnection. With reel-to-reel mass production lines adapted for wet chemical and fine-line lithographic techniques, FPCs continue to be an essential element in product design solutions today, especially for touch screen and large area LCD and LED based displays.
The HDI-FPC hybrid platform, known as rigid-flex or RFPCs, has been adapted to a number of different stackups to solve designers’ interconnect- product structuring challenges, resulting in an extensive patent literature of innovation. In general, one or more fine line single or double sided FPCs are applied as the conformal connection planes in a stackup combining HDI rigid PCB inner and outer layers, and appropriate adhesives and coverlays to both combine and protect the core for laser via creation, as well as final plated through-hole (PTH) and final metal finish plating steps. HDI layers and sub-composites with laser drilled vias combined with stacked, copper filled vias up to 16 layers has become the state of the art in circuit design for the newest generation of mobile phones, wearable electronics, and IoT modules.
Editor's Note: This article originally appeared in the April issue of The PCB Magazine.
Testimonial
"We’re proud to call I-Connect007 a trusted partner. Their innovative approach and industry insight made our podcast collaboration a success by connecting us with the right audience and delivering real results."
Julia McCaffrey - NCAB GroupSuggested Items
Indium Corporation Promotes Two Leaders in EMEA (Europe, Middle East, and Africa) Markets
08/05/2025 | Indium CorporationWith its commitment to innovation and growth through employee development, Indium Corporation today announced the promotions of Andy Seager to Associate Director, Continental Sales (EMEA), and Karthik Vijay to Senior Technical Manager (EMEA). These advancements reflect their contributions to the company’s continued innovative efforts with customers across Europe, the Middle East, and Africa (EMEA).
MacDermid Alpha Electronics Solutions Unveils Unified Global Website to Deepen Customer, Talent, and Stakeholder Engagement
07/31/2025 | MacDermid Alpha Electronics SolutionsMacDermid Alpha Electronics Solutions, the electronics business of Elements Solutions Inc, today launched macdermidalpha.com - a unified global website built to deepen digital engagement. The launch marks a significant milestone in the business’ ongoing commitment to delivering more meaningful, interactive, and impactful experiences for its customers, talent, and stakeholders worldwide.
KOKI to Showcase Analytical Services and New HF1200 Solder Paste at SMTA Guadalajara 2025
07/31/2025 | KOKIKOKI, a global leader in advanced soldering materials and process optimization services, will exhibit at the SMTA Guadalajara Expo & Tech Forum, taking place September 17 & 18, 2025 at Expo Guadalajara, Salón Jalisco Halls D & E in Guadalajara, Mexico.
Weller Tools Supports Future Talent with Exclusive Donation to SMTA Michigan Student Soldering Competition
07/23/2025 | Weller ToolsWeller Tools, the industry leader in hand soldering solutions, is proud to announce its support of the upcoming SMTA Michigan Expo & Tech Forum by donating a limited-edition 80th Anniversary Black Soldering Set to the event’s student soldering competition.
Koh Young Appoints Tom Hattori as President of Koh Young Japan
07/21/2025 | Koh YoungKoh Young Technology, the global leader in True 3D measurement-based inspection solutions, announced the appointment of Tom Hattori as President of Koh Young Japan (JKY).