Accomplish Change Together (ACT)
July 31, 2015 | Barry Matties, I-Connect007Estimated reading time: 2 minutes
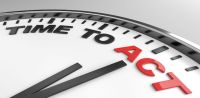
Shifting strategies for selling PCBs and the materials to build them is the impetus for ACT. Insulectro’s Ken Parent and Jason Marsh spoke to I-Connect007 Publisher Barry Matties about the ACT approach—and how it is helping their PCB fabricator customers increase sales and OEMs to get better products.
Barry Matties: Ken, tell me a little bit about what ACT is.
Ken Parent: One of the biggest excuses I hear, which is a reality, is that fabricators can’t put a new material in because a print comes in, they get a purchase order with the print, and it says that they have to use XYZ material. Their reasoning is that they cannot change materials because the OEM specified something else on the print. Accomplish Change Together (ACT) means there is probably something in the offering that we have that could make them more competitive as a fabricator; it could make the end-use product more competitive from a technology or cost perspective.
Matties: How do you do that? How do you get the OEM to change?
Parent: Well, we go after it together. When we met at APEX this year, you saw that we had Freedom CAD there in our booth. That is another important equation. We’re bridging Isola and DuPont into the design community. We have to get it designed onto the print, so we bring those resources together. I met new designers at the IMS show that were interested in ACTing with us, and between those OEM requirements, the design community, the material supplier, the PCB or PE fabricators and Insulectro, we believe that together, we can accomplish that change on a print. ACT is all of the above: designer, fabricator, material supplier, and distributor.
Matties: So by the time it reaches the fabricator, though, it’s a print shop basically. All the decisions have been made. So now it’s just matching the requirement with the best manufacturer.
Jason Marsh: In many cases that is true, but it is not always the case. In the really cutting-edge stuff, and you see a lot of it the RF space, people are pushing the physics envelope. We’re trying to push material solutions that have been around for 25 or 30 years, and we are running out of runway, so to speak. They might come to the fabricator and say, “Okay, I’ve designed this. I’ve modeled this. Can this be done?” It might not even test the way it’s been modeled.
It might not be possible to do, or certainly won’t be with reasonable yields. You mentioned the unique nature of us being a distributor, which is one of the things that allows us to sit in the middle—not just of traditional PCBs, but we also have this whole space in the additive conductor area of printed electronics. We have a lot of conversations with the assembly shop. We understand the whole ecosystem and how it fits together, and we’re continuously educating ourselves in that space.
Editor's Note: This article originally appeared in the July 2015 issue of The PCB Magazine.
Testimonial
"Advertising in PCB007 Magazine has been a great way to showcase our bare board testers to the right audience. The I-Connect007 team makes the process smooth and professional. We’re proud to be featured in such a trusted publication."
Klaus Koziol - atgSuggested Items
Magnachip Semiconductor Announces YJ Kim to Step Down as CEO; Current Board Chairman Camillo Martino Appointed Interim CEO
08/14/2025 | PR NewswireMagnachip Semiconductor Corporation today announced that YJ Kim has agreed to step down as CEO and as a member of the Board of Directors, effective immediately. Camillo Martino, Chairman of the Board of Directors, has also been appointed Interim Chief Executive Officer, effective immediately.
Bell to Build X-Plane for Phase 2 of DARPA Speed and Runway Independent Technologies (SPRINT) X-Plane Program
07/09/2025 | Bell Textron Inc.Bell Textron Inc., a Textron Inc. company, has been down-selected for Phase 2 of Defense Advanced Research Projects Agency (DARPA) Speed and Runway Independent Technologies (SPRINT) X-Plane program with the objective to complete design, construction, ground testing and certification of an X-plane demonstrator.
Nolan’s Notes: Moving Forward With Confidence
06/03/2025 | Nolan Johnson -- Column: Nolan's NotesWe’re currently enjoying a revitalized and dynamic EMS provider market with significant growth potential. Since December 2024, the book-to-bill has been extremely strong and growing. Starting with a ratio of 1.24 in December, book-to-bill has continued to accelerate to a 1.41 in April. Yet, there is a global economic restructuring taking place. To say that the back-and-forth with tariffs and trade deals makes for an uncertain market is an understatement. While we may be in a 90-day tariff pause among leading economic nations, the deadline is quickly approaching and that leaves many of you feeling unsettled about what to expect.
Mycronic High Flex Changes Division Name to PCB Assembly Solutions
05/20/2025 | MycronicMycronic AB, the leading Sweden-based electronics assembly solutions provider, announced that its division formerly known as High Flex will now operate under the name PCB Assembly Solutions.
SolderKing Achieves the Prestigious King’s Award for Enterprise in International Trade
05/06/2025 | SolderKingSolderKing Assembly Materials Ltd, a leading British manufacturer of high-performance soldering materials and consumables, has been honoured with a King’s Award for Enterprise, one of the UK’s most respected business honours.