Selecting a Reflow Oven, Part 1
August 10, 2015 | Robert Voigt, DDM NovastarEstimated reading time: 1 minute
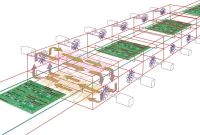
A reflow oven is simply any device that can liquefy solder in a controlled way to produce an electrical conductive bond between the component and its host (the board). There are several different methods to do this, not all of which can literally be called ovens. For instance, the simplest form of heating is performed by conduction, that is, by contact with a heated surface such as a hot plate. Other heating methods typically performed within a chamber (oven) but that rely on different heating methods include:
- Convection: Boards with their assembled components are passed through heated, circulating air from a conventional electrical heat source.
- Infrared (IR): Boards are passed inside a chamber over a direct IR heat source.
- Vapor Phase: Vapor is generated by heating a fluid with a specific boiling point (240°C) and transfers heat to the circuit board just above the melting point of the solder.
Let's begin with a commonly asked question: What size oven do I need? The answer is also a question: How many zones can you afford?
It seems like an odd way to start a discussion about reflow ovens, but it's not entirely unreasonable. As with any complex process, there will be tradeoffs between cost and capabilities, and more zones will always give you better flexibility and more control over your profile—but at a cost. The decision has to be qualified primarily on your anticipated throughput; that is, how many boards you process in a day or a week.
There are other considerations too, such as board size, component density, and appropriate thermal technology, but we’ll talk about those (and more) after identifying the work-flow volume.
A typical soldering operation in today's world requires three main stages for temperature profiling: preheat, soak (activate), and reflow, which perform these functions: 1) The preheat stage for a certain period of time to activation temperature; 2) the soak stage for a different period of time to activate the solder; and 3) the reflow stage where temperatures peak for yet a different time frame. After this, the board is typically cooled and removed. Depending on the material, e.g., leaded, lead-free or specialty materials such as epoxies, the heating profile for each stage will vary according to the manufacturer’s specifications to achieve optimal bonding.
Editor's Note: This article originally appeared in the August 2015 issue of SMT Magazine.
Suggested Items
Driving Innovation: Direct Imaging vs. Conventional Exposure
07/01/2025 | Simon Khesin -- Column: Driving InnovationMy first camera used Kodak film. I even experimented with developing photos in the bathroom, though I usually dropped the film off at a Kodak center and received the prints two weeks later, only to discover that some images were out of focus or poorly framed. Today, every smartphone contains a high-quality camera capable of producing stunning images instantly.
Hands-On Demos Now Available for Apollo Seiko’s EF and AF Selective Soldering Lines
06/30/2025 | Apollo SeikoApollo Seiko, a leading innovator in soldering technology, is excited to spotlight its expanded lineup of EF and AF Series Selective Soldering Systems, now available for live demonstrations in its newly dedicated demo room.
Indium Corporation Expert to Present on Automotive and Industrial Solder Bonding Solutions at Global Electronics Association Workshop
06/26/2025 | IndiumIndium Corporation Principal Engineer, Advanced Materials, Andy Mackie, Ph.D., MSc, will deliver a technical presentation on innovative solder bonding solutions for automotive and industrial applications at the Global Electronics A
Fresh PCB Concepts: Assembly Challenges with Micro Components and Standard Solder Mask Practices
06/26/2025 | Team NCAB -- Column: Fresh PCB ConceptsMicro components have redefined what is possible in PCB design. With package sizes like 01005 and 0201 becoming more common in high-density layouts, designers are now expected to pack more performance into smaller spaces than ever before. While these advancements support miniaturization and functionality, they introduce new assembly challenges, particularly with traditional solder mask and legend application processes.
Knocking Down the Bone Pile: Tin Whisker Mitigation in Aerospace Applications, Part 3
06/25/2025 | Nash Bell -- Column: Knocking Down the Bone PileTin whiskers are slender, hair-like metallic growths that can develop on the surface of tin-plated electronic components. Typically measuring a few micrometers in diameter and growing several millimeters in length, they form through an electrochemical process influenced by environmental factors such as temperature variations, mechanical or compressive stress, and the aging of solder alloys.