Cycle Time Reduction in a Flexible Circuit Facility
November 2, 2015 | Dave Becker, All Flex Flexible Circuits LLCEstimated reading time: 2 minutes
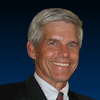
Managing product flow and cycle time across a wide range of product constructions and volumes in a high-mix flexible circuit fabrication facility can be extremely challenging. It can also be a critical success factor, so the only option is to accept the challenge! Many processes are capital-intensive as well as facility-limited, so using cellular manufacturing as an absolute solution is simply not feasible.
During the time I have spent in this industry (let’s not talk about how long), I have witnessed a substantial improvement with companies able to achieve significant cycle time reduction. This is done in several ways—with better processing equipment, faster design times, more predictable yields and improvements in material flow methods. Clever improvements in processing are myriad across many fabricators, but no single system seems to be a good fit for the challenges of a high-product-mix circuit fabrication facility.
What seems to work best for a high-mix factory with a wide range of part numbers is a tailored hybrid system. Concepts can be adopted from classic just in time manufacturing (JIT), theory of constraints (TOC) and quick response manufacturing (QRM). Four critical elements define cycle time management in a PCB factory:
• Material movement by Kanban (visual signal)
• Product mix control
• Short term capacity/workflow planning
• Daily management
Kanban
The basis of any cycle time reduction is to reduce work in process (WIP). The more work in process, the longer the overall cycle times. One controls WIP by controlling the amount of work introduced and flowing through the system. A common method is Kanban, where material movement is based on a visual signal indicating work is to be “pulled” from an upstream operation.
There are many versions of Kanban that are used successfully in manufacturing. One simple method is to Kanban from one operation or work center to the next. Signals are arranged so work is pulled into the next work center when it is ready to process it. This method works very well when the product flows tend to be homogeneous. Cellular manufacturing techniques tend to group operations by product family, which creates a near homogeneous product flow. Another method is using theory of constraints (TOC), where a critical work center is identified and work is introduced into the system based on the output of that constraint. Some companies simply have a Kanban based on what goes into finished goods. Material is introduced at the front end based on what gets completed into stock.
While all these methods will control WIP, they tend to struggle when a high product mix goes through the same work centers; this situation is very common for manufacturing that requires chemical processes and high capital cost equipment. The problem is that as product mix changes, the WIP will accumulate at different processes. The constraint moves around, while other critical work centers are starved for work. In this case cycle time reduction comes at the expense of overall throughput.
Editor's Note: This article originally appeared in the October 2015 issue of The PCB Magazine.
Testimonial
"We’re proud to call I-Connect007 a trusted partner. Their innovative approach and industry insight made our podcast collaboration a success by connecting us with the right audience and delivering real results."
Julia McCaffrey - NCAB GroupSuggested Items
SigmaTron Gets Supplier of the Year Award from Federal Signal
10/06/2015 | SigmaTron International Inc.SigmaTron International's Elk Grove Village (EGV), Illinois facility was named Supplier of the Year by Federal Signal.