Mr. Laminate Tells All: Where in the Holy Halogens did 900, 900, 1500 Come From?
November 12, 2015 | Doug Sober, Essex Technologies GroupEstimated reading time: 4 minutes
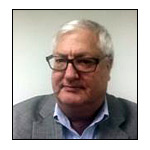
This new column, to appear monthly at PCB007, will focus on base materials and the laminate industry.
The 900, 900, 1500 is not a combination to an enormous safe that contains the remains of Jimmy Hoffa, nor is it the weight of three elephants at the San Diego Zoo in kilograms. The 900, 900, 1500 is the maximum parts per million (ppm) of bromine and chlorine and the total bromine and chlorine in a material that can be defined as “halogen-free” in the electronics industry today. But where did these requirements come from? Clearly, 900 ppm of bromine or chlorine is obviously not halogen-free. Some would argue that it is not even low-halogen at all.
In 2001, during an International Electrotechnical Commission (IEC, Geneva CH) meeting of TC91 Working Group 4: Base Materials and Boards, the member countries decided there should be a specification for FR-4 copper-clad laminates that were halogen-free. Several Japanese manufacturers were selling these laminates and prepregs around the world, primarily in Europe, but there were no specifications to conduct commercial business. Although the square meters per month of sales were quite small at the time, we knew that this product line would grow.
IEC 61249-2-21 was the document number designated in becoming the first FR-4 halogen-free standard in the world. The Working Group 4 decided to base the document and the requirements on the brominated counterpart IEC-61249-2-7 in terms of other property requirements. The main change was a relaxed moisture absorption requirement since halogen-free resins were worse than their brominated counterparts in these tests.
This was the easy part, but defining the halogen content would prove to be more controversial. During subsequent meetings, the Japanese National Committee, led by Dr. Aki Shibata, proposed a maximum of about 450 ppm of chlorine and about 450 ppm of bromine as a specification limit. As the USA National Committee leader, I proposed 1200 ppm for both halogens, as several domestic resin companies presented data that this was a more reasonable number. The debate continued for more than one year. No punches were thrown, but there was still a lot of pain.
One problem was that the copper-clad laminates (CCL), comprised of a higher resin content, generated a higher test value, since all the chlorine and bromine contaminants were coming from the epoxy resin components. For example, a 0.10 or 0.20 mm thick CCL may have a resin content of more than 65% while a 1.52 mm thick CCL may have only 40% resin. So two CCLs using the same resin varnish, but different constructions, generated significantly different results in the halogen test. In the end, the test specimen was defined as eight plies of low resin content/fiberglass fabric construction.
With the test specimen defined, the compromise on the definition of halogen-free between Dr. Shibata and me was decided upon as 900 ppm maximum chlorine, 900 ppm maximum bromine and a new requirement of 1500 ppm maximum for chlorine plus bromine. The rest of the Working Group 4 members agreed to these proposed specifications and the document was completed using the IEC process scheme for developing standards with a vote of the member countries.
Page 1 of 2
Testimonial
"Advertising in PCB007 Magazine has been a great way to showcase our bare board testers to the right audience. The I-Connect007 team makes the process smooth and professional. We’re proud to be featured in such a trusted publication."
Klaus Koziol - atgSuggested Items
SINBON Celebrates Opening of New US Manufacturing Facility
08/21/2025 | PRNewswireLeading electronics system integrator SINBON Electronics Co., Ltd. held an opening ceremony on August 18 to celebrate its new 59,000-square-foot facility in Clayton, Ohio.
PEDC Call for Abstracts Deadline Extended to Aug. 31
08/20/2025 | I-Connect007 Editorial TeamThe second Pan-European Electronics Design Conference (PEDC) will take place Jan. 21-22, 2026, in Prague, Czech Republic. The call for abstracts deadline has been extended to Aug. 31. Organized jointly by the German Electronics Design and Manufacturing Association (FED) and the Global Electronics Association (formerly IPC), PEDC serves as a European platform for knowledge exchange, networking, and innovation in electronics design and development.
Nano Silver Inks Market Forecast Report 2025-2030
08/20/2025 | Globe NewswireThe Nano Silver Inks Market is expected to grow from USD 427.415 million in 2025 to USD 836.160 million in 2030, at a CAGR of 14.36%.
VVDN Expands Manufacturing Footprint into the UAE to Meet Global Demand
08/20/2025 | PRNewswireVVDN Technologies, a global provider of software, product engineering and electronics manufacturing services & solutions, today announced it is setting up a new manufacturing facility in the UAE as part of its global expansion strategy.
Kimball Electronics Veterans ERG Members Proudly Participate in the 5th Annual Honor and Remember Run
08/20/2025 | Kimball ElectronicsVeterans and Military Service Advocacy (VMSA) Employee Resource Group (ERG) members Michael Mosher (Database Administration Engineer), Michael Stone (Test Technician Team Lead), and Joshua Belcher (Application Development Manager) took part in the 5th Annual Honor & Remember Run, a meaningful event dedicated to honoring fallen service members. The race featured a powerful memorial wall constructed from dog tags.