Honeywell Paper Investigates Avionics Vibration Durability
December 14, 2015 | Andy Shaughnessy, I-Connect007Estimated reading time: 6 minutes
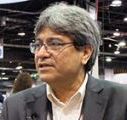
Andy Shaughnessy met with Dr. Joseph Juarez, principal mechanical engineer with Honeywell International, during SMTA International. He discussed his SMTA paper, which addresses avionics vibration durability between tin-lead and lead-free solder, the years of testing he conducted, and some of the surprising findings of his research.
Shaughnessy: You've written a pretty interesting paper on avionics vibration durability between tin-lead and lead-free solder interconnect. Joe, why don't you just walk us through, tell us about the paper, your research, and we'll go from there.
Joe Juarez: Absolutely. What we did was take one of our black box designs for an existing product made of tin-lead solder alloys and parts and fabricated an all lead-free version along with a tin-lead version and compares the two. Right now, all of our black boxes are made using tin-lead solder, but because of the advent of RoHS, we have to start looking at going to all lead-free alloy designs, and not only that, but most of the industry, in our cell phone or laptop computers and so on, are now all lead-free.
The idea here was, let's create another black box, an identical black box, but this time the solder is SAC-305, a lead-free solder. This project then focused on taking it through our normal qualification and subjecting both of them to the same level of qualification. We actually took them through 20 qualification cycles, which equals 300 hours on the vibration shaker for the tin-lead solder and parts, and 300 hours on the vibration shaker for their lead-free counterpart with survival on both boxes.
One of the issues was that we have a system that, under benign conditions, is identical. Well, of course, the issue then becomes that nothing broke. What's up with that? I mean, we've run these two things for 300 hours each and we’re trying to do a comparison. The next step was to step up the vibration level for both boxes, even though neither was designed for that. Let's just see what breaks first.
One of the things that we discovered was that if we put BGA component failure in context, we had other things that broke first. We had fretting, we had pins breaks, etc. What's interesting about this is that it made us realize, "Hey wait a minute, we've got a pretty robust system here when it comes to solderability." If you do a good job of soldering, guess what? That's not going to be the first thing that breaks. That was a pretty good breakthrough.
The other aspect of the paper was that we also ran a commercial code, University of Maryland's CALCE PWA code; to see how it performed in both of these environments, and it did very well for the product we designed. In other words, we ran regular qualification simulation and had statistical agreement. It was a very good predictor there, but when we actually cranked up the vibe levels, the code gave more conservative results. In other words, things broke that didn't really break, in reality, so that's the gist of the paper.
Shaughnessy: What would you say were some of the more surprising findings?
Juarez: In this paper, if you look through the literature review, I talk a lot about trying to statistically model what we actually saw. As I mentioned, I'm trying to break these boxes. When nothing broke through qualifications, I realized I was going to have to crank up the level, but when you do that and other things broke, I had to repair them. I get into this whole model complexity; now I have a repairable system that is now step-stress because I wasn't going to get a brand new box to run at a higher level from the start of testing.
I was going to have to keep the same box and step up the vibration level. I just complicated everything and what I discovered was that I got myself into a modeling area that's maybe breaking some new ground. So one of the next papers is to really delve into this whole thing of black box testing from a repairable step-stress standpoint, and that whole piece of reliability I try to really understand what's actually out there or do we have to invent new equations or something to really model that. Because what's in the literature, right now, doesn't cover some of the problems that we got ourselves into as we were trying to break things. Hopefully your readers may know of references that may be helpful to these circumstances?
The other discovery and I think I mentioned it already, was if you put failures in context, the solder joints break last. A lot of other things are going to bite you beforehand, and so it allows us to focus in on where we need to focus in terms of our design, like making sure that we understand fretting better so that things don't fret as early.
I guess the objective really is that everything breaks at the same time. Now you're wondering, that doesn't sound good, but you see the way we design stuff, given what I know now after this testing, everything will break at the same time, but maybe 50 years from now. Of course, with the electronics obsolescence and so on, by the time that thing breaks, it'll have been obsolete for a whole bunch of years. But at least for the service of the black box on the aircraft, it'll have its integrity.
Shaughnessy: That's good. It's funny you mention solder joints being the last to go. We surveyed our design readers and we asked them what they thought was the most common type of failure of a board in the field. Half of them said solder joint failure, and the other half said bad design.
Juarez: These lead-free boxes were specially made for this experiment, so there was a lot of workmanship in the solder joint assembly, but that should be standard anyway. I guess I'm going to be in the camp of, “If we do our solder joint assembly correctly, and we do our design well, we should be good to go.”
Shaughnessy: Is there anything else you wanted to add?
Juarez: Certainly, I will say one thing. In my acknowledgements, I acknowledge my director who really has supported my research. There will be a number of papers as a result of this work. We spent about two years of time doing the testing, and so it really takes a lot of faith in your management to turn you loose for a few years and give you the money you need to really do a good job. I have to say I laud my management.
Shaughnessy: Are you the head of the team?
Juarez: I guess I'm the head of the team that focuses on vibration issues. The other thing that I want to point out is, in terms of future work, there is an industry team that I do lead called the AVSI Consortium Airplane Environmental Monitor for In-Service Reliability project —it's the Airplane Vehicle Systems Institute out of Texas A&M. We're designing a black box containing a test vehicle that's actually going to be going on aircraft to actually test the performance of not only SAC305, which seems to be a standard for lead-free in our industry for high-reliability, but also emerging lower melting temperature lead-free solder alloys. We're looking at a lot of different alloys right now to actually put in aircraft.
We're looking at other aspects too, like wire bond and so on, so we're designing a special black box that's going to actually go on an aircraft. The big question is, “We do all of this on-the-ground test vehicle testing, but are we really subjecting these test vehicles to what you see in-flight?” What do those real in-service thermal and vibration loads look like? That's the follow-on to this to start getting this stuff in-service.
Shaughnessy: Joe thanks for sharing this with us. This is interesting stuff.
Juarez: Thank you, Andy.
Testimonial
"We’re proud to call I-Connect007 a trusted partner. Their innovative approach and industry insight made our podcast collaboration a success by connecting us with the right audience and delivering real results."
Julia McCaffrey - NCAB GroupSuggested Items
ZESTRON Expands Capabilities with Addition of the EPS by i-Tech AG 75 Pallet Cleaning System
08/26/2025 | ZESTRONZESTRON, the global leader in high-precision cleaning solutions and services, is excited to announce the addition of a new capability in its Technical Center in Manassas, VA:
Pick and Place Machine Innovator - NECTEC Launches Next-Gen SMT Line Solution With LED and X-ray Technology
08/26/2025 | Globe NewswireNECTEC PTE. LTD., a leading provider of SMT electronics manufacturing equipment, announced the official launch of its next-generation SMT solutions, featuring newly upgraded pick and place machine, specialized LED pick and place machines, enhanced Reflow Oven technology, advanced X-ray Inspection, high-speed X-ray Counter, and premium Solder Paste
MS2 Technologies, LLC/P. Kay Focuses on Central America with First Installation in Honduras
08/24/2025 | P. Kay Metal, Inc.This year MS2 Technologies has turned their focused to the growing electronics market in Central America. With that focus came the adaptation of MS2 and the Akila System from a Honduras-based corporation with manufacturing plants in both Honduras and Mexico.
BEST Inc. Provides High-Reliability BGA Reballing and Component Rework Services
08/22/2025 | BEST Inc.BEST Inc., a leader in electronic component services, is pleased to announce its component rework services are available for all types of area array devices including ball grid array, land grid array and quad flat no-lead SMT packages.
Indium Corporation Promotes Two Leaders in EMEA (Europe, Middle East, and Africa) Markets
08/05/2025 | Indium CorporationWith its commitment to innovation and growth through employee development, Indium Corporation today announced the promotions of Andy Seager to Associate Director, Continental Sales (EMEA), and Karthik Vijay to Senior Technical Manager (EMEA). These advancements reflect their contributions to the company’s continued innovative efforts with customers across Europe, the Middle East, and Africa (EMEA).