-
- News
- Books
Featured Books
- pcb007 Magazine
Latest Issues
Current IssueInventing the Future with SEL
Two years after launching its state-of-the-art PCB facility, SEL shares lessons in vision, execution, and innovation, plus insights from industry icons and technology leaders shaping the future of PCB fabrication.
Sales: From Pitch to PO
From the first cold call to finally receiving that first purchase order, the July PCB007 Magazine breaks down some critical parts of the sales stack. To up your sales game, read on!
The Hole Truth: Via Integrity in an HDI World
From the drilled hole to registration across multiple sequential lamination cycles, to the quality of your copper plating, via reliability in an HDI world is becoming an ever-greater challenge. This month we look at “The Hole Truth,” from creating the “perfect” via to how you can assure via quality and reliability, the first time, every time.
- Articles
- Columns
- Links
- Media kit
||| MENU - pcb007 Magazine
Estimated reading time: 1 minute
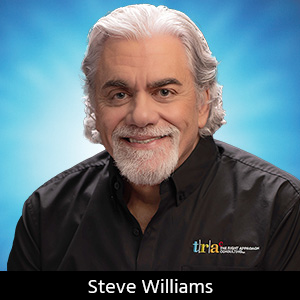
Cycle Time Reduction with WORK, Part I
Summary
Lean, theory of constraints (ToC), quick response manufacturing (QRM), cross training, and SPC are powerful, tried and true methodologies for process improvement. However, these tools are rooted in high-volume manufacturing environments and don't always play nice in a high-mix, low-volume (HMLV) operation. The new WORK manufacturing strategy was specifically developed to overcome these shortcomings while capitalizing on their strengths.
Limitations of the Current Toolset
Lean
Lean is a collection of tools and methods designed to eliminate waste, reduce delays, improve performance and reduce costs. Lean focuses on eliminating non-value-added activities, as opposed to more traditional improvement efforts, which focus on reducing the time in value-added steps. The problem with lean is that many of the tools work best in a high-volume process that has very little variation in product mix.
ToC
ToC is a methodology that focuses on removing bottlenecks from a process through a series of five steps:
1. Identify the constraint
2. Exploit (improve) the constraint
3. Subordinate (align all activities)
4. Elevate (additional actions)
5. Repeat
The problem with ToC is that, by definition, eliminating one bottleneck creates another, and in a high-mix process the bottlenecks can change with the mix.
Quick Response Manufacturing
Quick response manufacturing (QRM), a cell-based strategy closely related to focus factories that was developed specifically for HMLV, has been gaining popularity over the past few years. The problem with QRM is that it works best when equipment sets from a number of sequential departments can be physically organized into small cells. This becomes problematic in operations that have processes requiring capital intensive environments like plating, clean room imaging, etc., where setting up a single machine in a cell is prohibitive.
Editor's Note: This article originally appeared in the October 2015 issue of SMT Magazine.
More Columns from The Right Approach
The Right Approach: ‘Twas the Night Before Christmas (Harley-style)The Right Approach: I Hear the Train A Comin'
The Right Approach: Culture Change is Key to a QMS
The Right Approach: Leadership 101—Be a Heretic, Not a Sheep
The Right Approach: Leadership 101—The Law of Legacy
The Right Approach: Leadership 101: The Law of Explosive Growth
The Right Approach: Leadership 101—The Law of Timing
The Right Approach: The Law of Sacrifice