All About Flex: High-Temperature Performance Flexible Circuits
January 21, 2016 | Dave Becker, All FlexEstimated reading time: 2 minutes
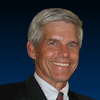
Markets requiring thermal exposure at elevated temperatures include down-hole oil drilling, semiconductor processing, medical diagnostics and a multitude of military/aerospace requirements. But a limitation of flexible circuitry has been performance at extremely high temperatures. For purposes of this discussion, the definition of “extremely high” is temperatures that exceed 150–200°C on a continuous basis or 288°C on an intermittent basis[1]. The flexible circuit industry has made inroads improving this product feature with recent developments and significantly improved high-temperature performance, which is being accomplished with new material constructions requiring some unique fabrication processing.
The adhesive system used to bond the various layers in a flexible circuit is normally considered the weakest link when parts are exposed to high temperature or a harsh chemical environment. This weakness has driven adoption of adhesiveless base laminate technology (the word “laminate” remains an industry term but is a bit misguiding when describing adhesiveless structures as they are not generally produced with a laminating process). Multiple methods for creating an adhesiveless base laminate substrates have become common (copper sputtering, vacuum deposition, cast polyimide) and provide improved performance in both extreme thermal and chemical environments.
But the most frequently used “top side” flexible circuit insulation is generally another layer of polyimide film commonly called coverlay or coverfilm. This layer of film is coated with an uncured adhesive and positioned onto the etched circuitry pattern and then permanently fastened during a temperature/pressure lamination cycle in a platen press. Consequently, an adhesive has been reintroduced into the circuit composite, despite removing the adhesive in the base substrate. Another top side dielectric used in the world of flexible printed circuits is a photo-imaged soldermask, but this material often becomes brittle at elevated temperatures, and can fracture or flake off when bent or folded.
Page 1 of 2
Testimonial
"Advertising in PCB007 Magazine has been a great way to showcase our bare board testers to the right audience. The I-Connect007 team makes the process smooth and professional. We’re proud to be featured in such a trusted publication."
Klaus Koziol - atgSuggested Items
Indium Corporation Promotes Two Leaders in EMEA (Europe, Middle East, and Africa) Markets
08/05/2025 | Indium CorporationWith its commitment to innovation and growth through employee development, Indium Corporation today announced the promotions of Andy Seager to Associate Director, Continental Sales (EMEA), and Karthik Vijay to Senior Technical Manager (EMEA). These advancements reflect their contributions to the company’s continued innovative efforts with customers across Europe, the Middle East, and Africa (EMEA).
MacDermid Alpha Electronics Solutions Unveils Unified Global Website to Deepen Customer, Talent, and Stakeholder Engagement
07/31/2025 | MacDermid Alpha Electronics SolutionsMacDermid Alpha Electronics Solutions, the electronics business of Elements Solutions Inc, today launched macdermidalpha.com - a unified global website built to deepen digital engagement. The launch marks a significant milestone in the business’ ongoing commitment to delivering more meaningful, interactive, and impactful experiences for its customers, talent, and stakeholders worldwide.
KOKI to Showcase Analytical Services and New HF1200 Solder Paste at SMTA Guadalajara 2025
07/31/2025 | KOKIKOKI, a global leader in advanced soldering materials and process optimization services, will exhibit at the SMTA Guadalajara Expo & Tech Forum, taking place September 17 & 18, 2025 at Expo Guadalajara, Salón Jalisco Halls D & E in Guadalajara, Mexico.
Weller Tools Supports Future Talent with Exclusive Donation to SMTA Michigan Student Soldering Competition
07/23/2025 | Weller ToolsWeller Tools, the industry leader in hand soldering solutions, is proud to announce its support of the upcoming SMTA Michigan Expo & Tech Forum by donating a limited-edition 80th Anniversary Black Soldering Set to the event’s student soldering competition.
Koh Young Appoints Tom Hattori as President of Koh Young Japan
07/21/2025 | Koh YoungKoh Young Technology, the global leader in True 3D measurement-based inspection solutions, announced the appointment of Tom Hattori as President of Koh Young Japan (JKY).