The Sum of All Parts: The Cost of Quality
March 9, 2016 | Sam Sangani, PNC Inc.Estimated reading time: 2 minutes
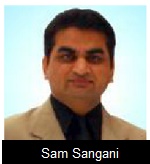
Throughout the decades, irrespective of industry or sector, markets have thrived on competition. They have, however, also relied upon some semblance of unity within their respective competitors. Industries rely upon their individual member companies’ ability to work together for the greater good.
The PCB industry is no different.
First and foremost, the desire for the utmost quality through parts manufactured in the United States is something that we should all be committed to. Here at PNC, we like to say, "We'd rather explain the cost of quality than have to apologize for the lack of it." The pros of using and buying PCBs in the United States, as opposed to Asia far outweigh the cons and the inverse holds true as well. Besides the obvious reasons such as promoting the domestic economy instead of a foreign one and keeping the jobs stateside, the most important factor is quality. Today’s customer—understandably so—has been forced to think from a cheaper-now perspective and has not been able to give any thought to longevity. The very same customer is subsequently required to buy more frequently due to the fact that the whole is less than the sum of its foreign parts.
Some may think that this is better for us, the actual producers of the boards, due to a frequent turnaround. However, with a sacrifice in quality of goods provided comes a sacrifice in the reputation of the business—and by extension, the industry—providing said goods. Another key facet of made-in-America boards is the service provided by the firm designing, making and/or assembling them. Sure, when you buy from Asia, the pricing is extremely competitive; however, chances are you are dealing with a broker whose only concern is their percentage. For brokers, promptness, quality and longevity take a backseat to commission and personal gain. In the unfortunate event that your order is late or revisions need to be made, they are long gone.
Perhaps the most important downfall of Asian-made boards is their manufacturing practices. Bare minimums are keys to the pricing success that makes U.S. board manufacturers at a disadvantage. For example: The IPC Standard states 1.97 Au over 118 Ni, but it is often seen that the overseas boards are far under the standard amounts of Au and Ni. It may look good, but this will certainly have an effect on the solderabilty. But how can we all do our part?
As a board house, we can all focus on educating our customers with regards to why it is worth the extra dollars to get the job done stateside. Most consumers of PCBs already have some semblance of knowledge about the product they are asking for and will know some of the pros and cons.
As a customer, you can think about your end user. Whether it is for the mass production of a board, which will then be incorporated into a box build or for a small run of prototypes, the goal is to overall deliver the best product possible. That is something we can all agree on is easiest to accomplish in this country.
Sam Sangani is president and CEO of PNC Inc.
Testimonial
"The I-Connect007 team is outstanding—kind, responsive, and a true marketing partner. Their design team created fresh, eye-catching ads, and their editorial support polished our content to let our brand shine. Thank you all! "
Sweeney Ng - CEE PCBSuggested Items
Flexible Circuit Technologies to Host Free Flex Heater Webinar
08/18/2025 | Flexible Circuit TechnologiesGlobal Supplier of flexible circuits, flex design services, and assembly/box-build services, Flexible Circuit Technology will host their latest webinar, "Thermal Precision Meets Flexibility: The Technology Behind Heater Circuits" on Tuesday, August 26th, 2025 at 11 AM EDT.
A.R.T. Ltd. Nominated in Four Categories at 2025 Instrumentation and Electronics Industry Awards
08/11/2025 | A.R.T. Ltd.Advanced Rework Technology Ltd. (A.R.T. Ltd.), a leading provider of electronics training and consultancy, has been shortlisted in four categories at the 2025 Instrumentation and Electronics Industry Awards, including Industry Personality, Academic Support, Rising Star, and Best Customer Service.
EMC Taiwan Receives IPC-4101 Qualified Products Listing Certification
08/08/2025 | Global Electronics AssociationIPC’s Validation Services Program has awarded an IPC-4101 Qualified Products Listing (QPL) to Elite Materials Co. (EMC), an electronics base material manufacturing company headquartered in Taoyuan City, Taiwan.
Global Excellence in PCB Design: The Global Electronics Association Expands to Italy
08/07/2025 | Global Electronics AssociationIn today's rapidly evolving electronics industry, printed circuit boards (PCBs) serve as the critical backbone influencing the success, reliability, and time-to-market of countless products. Recognizing this essential role, the Global Electronics Association (formerly IPC), a worldwide leader in electronics standards, certification, and education, is now expanding its internationally acclaimed PCB design training to Italy.
Dana on Data: Best Practices in Interpreting Drawing Notes—‘Use Latest Revision’
08/07/2025 | Dana Korf -- Column: Dana on DataThe global nature of electronics manufacturing requires clear, consistent, and precise communication, particularly in technical documentation. An area where miscommunication often arises is in interpreting drawing notes—small lines of text with the potential to dramatically impact product quality, manufacturing efficiency, and customer satisfaction.