Rex Rozario, Part 3: The Future Beckons
March 16, 2016 | Barry Matties, I-Connect007Estimated reading time: 14 minutes
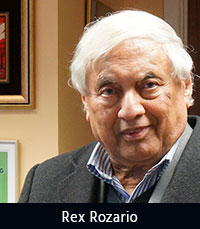
In Part 3 of our multi-part interview with industry veteran Rex Rozario, we begin with the future. Having achieved success in China, could Rex and the Graphic team have their sights trained on the U.S.? Also in this installment, Rex weighs in on China’s future, and we discuss the value of automation. Is it for everyone?
Click here for Part 1 and Part 2.
Barry: Rex, what can you tell me about what’s on the horizon for Graphic?
Rozario: We have a lot of possible plans in mind of where to go, so we are still looking around. We feel our next journey is to the U.S., because it's a huge marketplace. With our expertise and once they get to know what we do, we’ll be successful and it will open doors for us. I think the proof will be in the pudding once they try out our services. Also, we're the first company in the UK to offer application engineering as a free service. If somebody is designing something, we will go in there, provided we get the prototypes and the order to follow up on. And that gives them confidence. We can technically design it to manufacture and we can manufacture it much faster, more economically and at a cost saving. Now if someone is designing something really special, very high tech, we would send their favorite engineers and they could be there for two weeks with them to discuss it.
Matties: That was a big advantage in the early days for you.
Rozario: It certainly was.
Matties: Now other companies have followed suit.
Rozario: Anything you start, everybody will follow. It goes without saying that everybody claims all sorts of things and people only find out that it's not true when someone asks a question. But like I mentioned before, we have always worked on approvals. If there is one available we have to get it. Then they follow up like the managing director of BAE did in 1994, when he said our product had the best performance and all of his sites are open for our product and so forth. That's only one supplier. There are so many others at that level who are talking to us.
The only challenge is if for some reason they feel they want to split the order for security reasons, then somebody else gets it. Now we have so much choice here [UK], we can spread it out between UK, China, Italy and the U.S. It’s a safety net; if a factory burns down it doesn't make any difference to the customer.
We’re not putting all the eggs in one basket. That was a fear that most people had in the past, but they can come to us now for a one-off for any quantity they want. Obviously, we are competitive, otherwise customers wouldn't stay with us.
Matties: When you talk about the future and your strategies and looking to America, what is left to do there? In terms of strategy, what do you see?
Rozario: We start with the marketplace. We know rigid-flex could take off there. At Graphics USA, we would obviously think about putting a real facility in there at Santa Fe Springs, or we could look at combining it with someone else, like we do in China, at the DSG facility. We have the room there to expand.
Matties: Are you looking to do volume production in the U.S.? With automation it seems like volume production can be done anywhere in the world these days considering your expertise with automation.
Rozario: When you talk about automation, the volume is unlimited. In China, if you want half a dozen boards, it's not good to do it here in the UK and ship it over there. They can do it. China is geared up for large, consistent volume, so that's available, whereas other companies in the UK, and Italy, are medium-sized. We're talking about thousands, but not the full run of tens of thousands boards. Fortunately, I think when global customers realize that there is a company that with one phone call, text, or e-mail can look after all their needs of any type of board they would want, it’s hard to turn down.
Some people specialize in flex, rigid-flex or PTH and so forth. Not many people have the experience to do everything. We have worked on carbon fibre and have lots of experience with it because we feel it’s the material of the future. People will be looking for tougher materials in heating systems and so forth. It's a bit expensive for people to actually change over from epoxy glass now. At some stage there could be requisites that people would need. All the body work for planes is now done with carbon fibre, and some of the top cars. That's something on which we are in close liaison with Exeter University. We're constantly developing and experimenting and looking at what else is there, so that we can offer it to the customer, hopefully better than anybody else
Matties: What I hear you saying is, wherever you're at, it's never good enough, because the future is constantly changing.
Rozario: It's changing overnight, really. Whatever you have today is different on the following day.
Matties: You could easily sit back as a company and just enjoy the success that you've already achieved and ride off into the sunset so to speak.
Rozario: Easily, for myself personally, but for the company itself you have to compare us to the large companies who were competing with us when we first started—BAE, Marconi, IBM, Motorola—all these companies had their own PCB manufacturing. There came a time when they had to decide to just stay put or keep developing, and they decided, “Why should we spend money on R&D? Let those guys do it. Let's go to someone who has the facility and the experience. It’s cheaper than employing people and buying the raw material up front and all that hassle.”
Matties: Then the environmental impact came along, too.
Rozario: Yeah, I remember so many board shops being closed in the early days. I also remember people moving from one state to another to save cash, because the laws were different in the other state.
Fortunately, like most of the guys who started together back then, there are names that we still relate to, although they might not have been PCBs. Those were the pioneer days. You had to go looking for things and make things happen. It's a bit easier now, because you can go and buy a machine that will do the job. With the availability of all the facilities for manufacture now, you don’t have to reinvent the wheel. When somebody realized they wanted a double-sided board connected, nobody thought about through-hole plating. You just put an eyelet in there and that did the job. Someone said, "Gosh you have to put it in a mechanical device, why couldn't we do it in the plating?" Those things have all been done, but there are areas like buried capacitance where we are still doing that now. There will come a time for the future materials, like graphene. I think that's the way things will go, but hopefully we will be there and constantly be aware that these things are happening.
Again, fortunately with my connections to all the federations like IPC, I’ve been very much involved. We are fully aware of what's going on and also are constantly talking to suppliers and so forth. As long as that continues, I think we should be okay. We're always aware that there comes a saturation point, and then how do you carry on? The only way is technology. I feel the only way we can survive and make a profit is by constantly developing new technology, because customers will always pay for something that's going to save them cash, and probably pay a little bit more. We did a conference with IPC many years ago and called it “Circuits on the Cheap.” The hall was packed because people came in there looking for a cheap solution.
We were saying that what we manufactured 25 years ago, the same thing can be had cheaper than before. That was the idea, but they got the wrong impression with Circuits on the Cheap. Things are getting cheaper and cheaper due to the competition and if there's a recession, people are just cutting prices. Even now, to my knowledge, several small companies are struggling and some of them sadly might disappear.
Matties: There's no doubt some are going to disappear.
Rozario: Also, the new trend is amalgamation, and obviously if you look at the large companies like TTM, Viasystems and DDi, they are one company now, because that's another way of sustaining and keeping the levels going and keeping the marketplace. Obviously, the bigger you are, the more service you have. You don't want to stay where you are. You must look at the next stage. That's another thing that one can look at, and we've got a very good partner we are working with now. Those are other areas we might look at very closely as we develop.
Page 1 of 2
Suggested Items
Seeing a Future in Mexico
07/09/2025 | Michelle Te, I-Connect007The Global Electronics Association (formerly known as IPC) has been instrumental in fostering a partnership with Guanajuato, a state north of Mexico City with 12 industrial clusters and close to 150 companies involved in electronics. This past spring, Alejandro Hernández, the undersecretary for investment promotion in Guanajuato, attended IPC APEX EXPO 2025 at the invitation of IPC Mexico Director Lorena Villanueva, where he met with several companies to discuss the opportunities available in Mexico. He is inviting electronics-related companies seeking long-term investment in a centrally located area with access to highways, railways, and ports.
The Global Electronics Association Releases IPC-8911: First-Ever Conductive Yarn Standard for E-Textile Application
07/02/2025 | Global Electronics AssociationThe Global Electronics Association announces the release of IPC-8911, Requirements for Conductive Yarns for E-Textiles Applications. This first-of-its-kind global standard establishes a clear framework for classifying, designating, and qualifying conductive yarns—helping to address longstanding challenges in supply chain communication, product testing, and material selection within the growing e-textiles industry.
IPC-CFX, 2.0: How to Use the QPL Effectively
07/02/2025 | Chris Jorgensen, Global Electronics AssociationIn part one of this series, we discussed the new features in CFX Version 2.0 and their implications for improved inter-machine communication. But what about bringing this new functionality to the shop floor? The IPC-CFX-2591 QPL is a powerful technical resource for manufacturers seeking CFX-enabled equipment. The Qualified Product List (QPL) helps streamline equipment selection by listing models verified for CFX compliance through a robust third-party virtual qualification process.
The Knowledge Base: A Conference for Cleaning and Coating of Mission-critical Electronics
07/08/2025 | Mike Konrad -- Column: The Knowledge BaseIn electronics manufacturing, there’s a dangerous misconception that cleaning and coating are standalone options, that they operate in different lanes, and that one can compensate for the other. Let’s clear that up now. Cleaning and conformal coating are not separate decisions. They are two chapters in the same story—the story of reliability.
Advancing Aerospace Excellence: Emerald’s Medford Team Earns Space Addendum Certification
06/30/2025 | Emerald TechnologiesWe’re thrilled to announce a major achievement from our Medford, Oregon facility. Andy Abrigo has officially earned her credentials as a Certified IPC Trainer (CIT) under the IPC J-STD-001 Space Addendum, the leading industry standard for space and military-grade electronics manufacturing.