Smaller. Cheaper. Better.
March 28, 2016 | DOE/Sandia National LaboratoriesEstimated reading time: 2 minutes
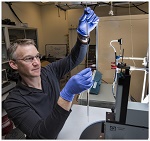
A Sandia-led team has developed a way to make a magnetic material that could lead to lighter and smaller, cheaper and better-performing high-frequency transformers, needed for more flexible energy storage systems and widespread adoption of renewable energy.
The work is part of a larger, integrated portfolio of projects funded by Department of Energy's (DOE) Energy Storage Program in the Office of Electricity Delivery and Energy Reliability.
Transportable energy storage and power conversion systems, which can fit inside a single semi-trailer, could make it cost effective to rapidly install solar, wind and geothermal energy systems in even the most remote locations.
"Such modular systems could be deployed quickly to multiple sites with much less assembly and validation time," said Sandia researcher Todd Monson of Nanoscale Sciences Department, who led the team with Stan Atcitty of Sandia's Energy Storage Technology & Systems Department.
Sandia manufactures iron nitride (γ'-Fe4N) powders by ball-milling iron powders in liquid nitrogen and then ammonia. The iron nitride powders are then consolidated through a low-temperature field-assisted sintering technique (FAST) that forms a solid material from loose powders through the application of heat and sometimes pressure.
The FAST manufacturing method enables the creation of transformer cores from raw starting materials in minutes, without decomposing the required iron nitrides, as could happen at the higher temperatures used in conventional sintering. Previously, the γ' phase of iron nitride has only been synthesized in either thin-film form in high-vacuum environments or as inclusions in other materials, and never integrated into an actual device.
Monson said using this method could make transformers up to 10 times smaller than they are currently.
No machining required
"FAST enables the net-shaping of parts, meaning that iron nitride powders can be sintered directly into perfectly sized parts, such as transformer cores, which don't require any machining," Monson said.
Due to its magnetic properties, iron nitride transformers can be made much more compact and lighter than traditional transformers, with better power-handling capability and greater efficiency. They will require only air cooling, another important space saver. Iron nitride also could serve as a more robust, high-performance transformer core material across the nation's electrical grid.
So far, Monson and his colleagues have demonstrated the fabrication of iron nitride transformer cores with good physical and magnetic characteristics and now are refining their process and preparing to test the transformers in power-conversion test beds.
Page 1 of 2
Suggested Items
Symposium Review: Qnity, DuPont, and Insulectro Forge Ahead with Advanced Materials
07/02/2025 | Barb Hockaday, I-Connect007In a dynamic and informative Innovation Symposium hosted live and on Zoom on June 25, 2025, representatives from Qnity (formerly DuPont Electronics), DuPont, and Insulectro discussed the evolving landscape of flexible circuit materials. From strategic corporate changes to cutting-edge polymer films, the session offered deep insight into design challenges, reliability, and next-gen solutions shaping the electronics industry.
Indium Corporation Expert to Present on Automotive and Industrial Solder Bonding Solutions at Global Electronics Association Workshop
06/26/2025 | IndiumIndium Corporation Principal Engineer, Advanced Materials, Andy Mackie, Ph.D., MSc, will deliver a technical presentation on innovative solder bonding solutions for automotive and industrial applications at the Global Electronics A
Gorilla Circuits Elevates PCB Precision with Schmoll’s Optiflex II Alignment System
06/23/2025 | Schmoll MaschinenGorilla Circuits, a leading PCB manufacturer based in Silicon Valley, has enhanced its production capabilities with the addition of Schmoll Maschinen’s Optiflex II Post-Etch Punch system—bringing a new level of precision to multilayer board fabrication.
Day 1: Cutting Edge Insights at the EIPC Summer Conference
06/17/2025 | Pete Starkey, I-Connect007The European Institute for the PCB Community (EIPC) Summer Conference took place this year in Edinburgh, Scotland, June 3-4. This is the second of three articles on the conference. The other two cover the keynote speeches and Day 2 of the technical conference. Below is a recap of the first day’s sessions.
American Made Advocacy: Supporting the Entire PCB Ecosystem—Materials to OEMs
06/17/2025 | Shane Whiteside -- Column: American Made AdvocacyWith the addition of RTX to PCBAA’s membership roster, we now represent the interests of companies in the entire PCB ecosystem. From material providers to OEMs, the insights of our collective members help us educate, advocate, and support legislation and policy favorable to America’s microelectronics manufacturers. The industry veterans who lead these companies provide valuable perspective, and their accumulated wisdom makes us an even stronger association.