Stepping Up to Laser Processing for Flex, Part 2: Calculating and Optimizing Production
April 14, 2016 | Mike Jennings and Patrick Riechel, ESIEstimated reading time: 1 minute
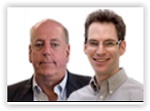
A Process of Continual Improvement
In Part 1 of this series, we discussed the advantages of adding flex laser processing to gain a competitive advantage. In Part 2 we will build on that discussion, looking at the ways you can optimize your flexible circuit laser processing to get the efficiencies that drive lower cost of ownership. When considering the cost associated with adding FPC processing, where do you look, what should you expect, and how can you control or minimize those costs?
Controlling Fixed costs
Aside from the obvious system purchase price and its associated depreciation expense, there are a variety of other—and less significant—fixed costs to consider. These can include system installation and personnel training costs, costs to qualify the system prior to running production, floor space allocation overhead allocation costs, as well as the costs related to upgrading facilities to meet the system’s site requirements. We will discuss site preparation in Part 3.
Typical areas to watch for in laser system site requirements include electrical, vacuum, compressed air, environmental air, as well as temperature and humidity. Neglecting any of these can result in poor product yield, scrap, or even damage to and downtime on your valuable UV laser system. Poor electrical power quality and sporadic brownouts and blackouts often can result in unexpected system errors, yield issues, and scrap.
Extending System Longevity
Typical high-power UV lasers used for flex processing have lifespans ranging from 1–2 years, although those lifespans may be drawn out if the laser is not in 24/7 use or the laser powers used for processing are much lower than the system’s work surface laser power specification.
Editor's Note: This article originally appeared in the March 2016 issue of The PCB Magazine.
Testimonial
"Our marketing partnership with I-Connect007 is already delivering. Just a day after our press release went live, we received a direct inquiry about our updated products!"
Rachael Temple - AlltematedSuggested Items
ION Storage Systems Launches 'Cornerstone'
08/12/2025 | PRNewswireION Storage Systems, Inc. (ION), a Maryland-based leader in next-generation solid-state battery technology, announces today that it has begun shipping Cornerstone, the first commercial generation of ION's solid-state battery technology, to leading consumer electronics companies.
Benchmark Completes Delivery of the Next Phase of High-Tech Surveillance Solutions for U.S. Customs and Border Protection Share
08/11/2025 | BUSINESS WIREBenchmark Electronics, Inc. proudly announces the successful completion of the delivery of 24 Mobile Vehicle Surveillance Systems with Radar (MVSS-R) for U.S. Customs and Border Protection (CBP) and the Federal Aviation Administration (FAA).
Spirit AeroSystems Announces Definitive Agreement with CTRM for Acquisition of Facility in Subang, Malaysia
08/11/2025 | PRNewswireSpirit AeroSystems Holdings, Inc. announces a purchase agreement to sell its facility and businesses in Subang, Malaysia to Composites Technology Research Malaysia Sdn Bhd (CTRM) for $95,200,000, subject to customary adjustments.
Smart Automation: Pick-and-place Machines—What Matters in 2025
08/12/2025 | Josh Casper -- Column: Smart AutomationWhen people talk about placement technology, they often zero in on speed: How fast can a machine place components? What's the quoted components per hour (CPH)? How many nozzles are on the head? While these metrics matter, on most production floors, the fastest machine on paper isn’t always the most productive.
BAE Systems to Build on AI Pedigree Through Investment in UK Start-up Oxford Dynamics
08/08/2025 | BAE SystemsBAE Systems has made a strategic investment in Oxford Dynamics, a UK-based deep-tech start-up specialising in artificial intelligence (AI) and robotics, as part of its ongoing drive to identify and harness innovative technologies for rapid deployment.