All About Flex: Lean Manufacturing and NPIP for Flexible Circuits
April 21, 2016 | Dave Becker, All FlexEstimated reading time: 1 minute
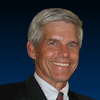
Many companies are familiar with lean manufacturing concepts and have successfully used these techniques to improve manufacturing processes. Lean techniques, while most often used in printed circuit fabrication and assembly operations, can also be applied to nonmanufacturing processes. One such process is new part number introduction (NPIP).
The main thrust of lean manufacturing is to eliminate or reduce waste. There are typically seven wastes (mudas), as defined by Toyota executive Taiicho Ohno, when he developed Toyota’s Production System (TPS)[1]. (“Muda” is a Japanese word meaning uselessness, idleness or other synonyms of waste.) The seven mudas are:
- Transport
- Inventory
- Motion
- Waiting
- Over-processing
- Over-production
- Defects
The typical part number startup for flexible circuits often can suffer from a number of those wastes. Certain waste items are specific to a part number (customer out of office, conflicts in documentation, iterative design conversations, etc.) or be ingrained as accepted gaps in a supplier’s product launch system. As part of a continuous improvement mentality, wastes should be identified for reduction through a documented and monitored part number introduction process. Some of the more common waste elements are:
Transport: In a new part number introduction process (NPIP), transport is the movement of documentation (electronic or paper) from one department to another requiring successive reviews and sign-offs. Excess transport is a symptom of a departmentalized approach to part number start-up rather than a process flow approach. A cross-functional design review team with one leader can remove departmental barriers and help assure that reviews and inputs are done in parallel rather than serially. Transport can also include sending information requests and approvals to customers and suppliers. These requests need to be challenged regarding their usefulness and necessity.
Editor's Note: This article originally appeared in the March 2016 issue of The PCB Magazine.
Testimonial
"The I-Connect007 team is outstanding—kind, responsive, and a true marketing partner. Their design team created fresh, eye-catching ads, and their editorial support polished our content to let our brand shine. Thank you all! "
Sweeney Ng - CEE PCBSuggested Items
VVDN Expands Manufacturing Footprint into the UAE to Meet Global Demand
08/20/2025 | PRNewswireVVDN Technologies, a global provider of software, product engineering and electronics manufacturing services & solutions, today announced it is setting up a new manufacturing facility in the UAE as part of its global expansion strategy.
Haylo Labs Acquires Plessey Semiconductors
08/20/2025 | Haylo LabsHaylo Labs has acquired Plessey Semiconductors, the UK’s leading innovator in microLED display technology.
Kimball Electronics Veterans ERG Members Proudly Participate in the 5th Annual Honor and Remember Run
08/20/2025 | Kimball ElectronicsVeterans and Military Service Advocacy (VMSA) Employee Resource Group (ERG) members Michael Mosher (Database Administration Engineer), Michael Stone (Test Technician Team Lead), and Joshua Belcher (Application Development Manager) took part in the 5th Annual Honor & Remember Run, a meaningful event dedicated to honoring fallen service members. The race featured a powerful memorial wall constructed from dog tags.
Meet Incap UK at the Electronic Component Show 2025
08/20/2025 | IncapIncap UK is pleased to be exhibiting at the Electronic Component Show 2025. This one-day event will take place on 18 September at the Kassam Stadium in Oxford, bringing together design engineers, purchasing professionals, manufacturers, distributors, and service providers to discover new products, solutions, and contacts. You will find us at stand 52.
Hon Hai Rotating CEO Yang Qiujin Wins 2025 Golden Yang Award for Women’s Power in Technology
08/20/2025 | Hon Hai Precision Industry Co., Ltd.Amid the global rise of "female-powered technology," Yang Qiujin, Rotating CEO of Hon Hai Precision Industry Co., Ltd. (TWSE: 2317), the world's largest platform solutions provider, has been awarded the "2025 Golden Yang Award - Female-Powered Technology" by the China Software Association/China Software Industry Association.