All About Flex: Imaging Methods for Etch Resist, Part 1
April 28, 2016 | Dave Becker, All FlexEstimated reading time: 6 minutes
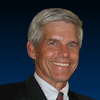
Imaging is a major process step in creating a copper circuit or flexible PCB. In single-sided circuit fabrication, the imaging process creates the resist pattern that protects the copper from the etchant. It is critical that this pattern precisely define the circuit traces, as issues with imaging will transfer to the subsequent processes. There are three basic methods for defining the etch resist image in typical flexible circuit manufacturing:
- Screen printing
- Photo imaging
- Laser direct imaging
Each of these methods has unique differences relating to cost, quality, capital investment and through-put. This three-part article will explore each method in detail, starting with screen printing.
Screen Printing
Screen printing is widely used in a number of industries. It is commonly used in decorating T-shirts, printing colorful posters, creating sophisticated graphic overlays, printing ceramic hybrid circuits and creating membrane switches, as well as PCBs. Screen printing equipment can be as basic as a wooden frame placed on a table or as sophisticated as a fully automated computer-controlled system with optical registration and digital inspection.
While the quality, speed and precision can widely vary depending on materials, technology and operator skill level, the basic principles are the same. A screen mesh is stretched and bonded to a frame. The pattern is defined by a solid emulsion coated and imaged over the screen where selected areas are left as open mesh. The screen is aligned to the desired substrate and positioned so that the mesh is just a few millimeters above the surface. The material that gets deposited is often just referred to as “ink” or “paste.” The ink is flood-coated over the mesh area with a flood bar. With the screen aligned over the substrate, a vinyl or rubber squeegee is “pushed” across the screen; the squeegee pumps the ink through the mesh and onto the substrate while pressing the screen in contact with the surface, resulting in a printed pattern.
The diagram below shows the basic actions of screen printing.
A Study of the Abrasion of Squeegees Used in Screen Printing and its Effect on Performance with Application in Printed Electronics[1].
Consider the critical elements of this process.
The ink needs to be viscous enough to sit on the mesh without dripping or bleeding through the mesh. Then when it is pumped through the mesh onto the substrate, it needs to fill in the voids caused by the strands of wire mesh, yet not flow so much as to affect the desired resolution.
The screen itself needs to be able to stretch enough to contact the substrate where the squeegee is pressing down, but have enough memory to return to its original tension. Screen meshes are typically made from stainless steel fibers, polymer fibers or a metalized polymer fiber. Screen mesh comes in all different sizes: at one extreme you have very coarse strands with very large mesh openings and at the other you have very fine strands with tiny mesh openings. The finer the screen mesh the better the resolution and the thinner the ink deposit. The coarser mesh yields a thicker ink deposit but results in lower resolution than finer mesh. Screens are described by the number of mesh openings in a square inch. Coarse mesh might be around 100, fine mesh can be 400.
Figure 1 depicts an emulsion image on screen mesh.
Figure 1.
Screen printing is a distortion process. In the print position, the screen is set at some small distance above the surface. The squeegee action stretches the screen at the point of contact. Without compensation mechanisms, the image that is printed onto the substrate will end up slightly larger than the image pattern on the screen mesh. The larger the screen and print area, the larger the distortion; the level of acceptable distortion depends on the application. Screen printing on a t-shirt does not require a lot of precision or accuracy, at least relative to the precision needed for a printed circuit or a ceramic hybrid circuit. One way to compensate for the distortion is to factor the artwork, so that the actual pattern on the screen is smaller than the desired pattern. Some of the more sophisticated screen printing machines can automatically compensate for the distortion by moving the screen while printing. This can be combined with optical measurements that will calculate the distortion and modify the screening motion to correct the dimensional differences.
There are two types of screen printing presses, flatbed and cylinder. A flatbed press typically uses a vacuum table that holds the material flat; the screen is positioned to be aligned over the substrate and the squeegee pushes across the screen. A cylinder press has the substrate partially wrapped around a vacuum cylinder so that the point of contact with the screen will only occur at the tangential point. The substrate and the screen both move together while the squeegee is stationary. The advantage of a cylinder press is the screen has a much smaller off-contact than a flatbed screen printer. This results in much less screen distortion, better resolution and longer screen life. The major disadvantage of a cylinder press is that the material must be flexible. It also usually requires the substrate to be a continuous reel of material. A diagram of a cylinder screen printing press is shown in Figure 2.
Figure 2.
There are several potential issues with screen printing that can affect quality and productivity:
- Screen life: Even if everything is set up correctly, the screen has a limited life. During the printing process the screen is in a continual cycle of stretching and snapping back into position. The properties of the screen will degrade with every cycle; eventually the screen tension drops below the point of acceptability and it must be replaced.
- Pot life of the ink: The ink is also in a continuous cycle of being pushed across a mesh. Only a very small amount of ink gets pushed through the mesh in a cycle, the rest is gathered back up and re-flooded over the mesh. This continual working of the ink will result in loss of solvents and changes in viscosity properties. As the ink changes, the precision of the print may also change. If ink loses too much solvent, it can dry in the screen and plug holes in the mesh.
- Dirt/particles: Foreign material in the screen will plug mesh openings and particles on the substrate cause imaging problems. Anyone who has tried to paint a wall when the paint has particles in it has dealt with a similar issue. The same principle applies to screen printing. The ink must be kept as pristine as possible for a repeatable process.
Screen printing is used for ultra-high volume, low-density flexible circuit applications. Screen printing requires less process material and automated printing has a significantly higher throughput rate vs. the other imaging processes. Screen mesh has limitations on the image resolution. While some ceramic hybrid circuit manufacturers are screen printing densities to 5 mil lines and spaces, their print area is typically less than a 3” x 3” square. With a smaller print area and screen, finer mesh is possible, resulting in better control. Most flexible circuit fabricators are processing much larger panel sizes, so printing 3” x 3” patterns is not very efficient. High density interconnect (HDI) applications require much better resolution vs. what screen printing can repeatedly provide.
Figure 3.
Regardless of the mesh size, image size and other controls, the screen printed pattern will have a slightly jagged edge, as shown in Figure 3.
Figure 3 illustrates the resolution limitation of screen printing. In applications with dynamic flexing, the scalloped edge can cause stress concentration and conductor fracturing. As density demands within the electronic market continue to increase, photo imaging has become the preferred imaging technology. To a large extent, the printed circuit world has settled on a photo-lithographic process for imaging technology. There is a well-established infrastructure of equipment, chemistries, and material supporting this process methodology.
Next time, in Part 2: photoimaging.
References
1. www.mdpi.com
Dave Becker is vice president of sales and marketing at All Flex Flexible Circuits LLC.
Testimonial
"Advertising in PCB007 Magazine has been a great way to showcase our bare board testers to the right audience. The I-Connect007 team makes the process smooth and professional. We’re proud to be featured in such a trusted publication."
Klaus Koziol - atgSuggested Items
Statement from the Global Electronics Association on the July 2025 Tariff on Copper Foil and Electronics-Grade Copper Inputs
07/31/2025 | Global Electronics AssociationWe are disappointed by today’s decision to impose a 50% tariff on imported copper foil and other essential materials critical to electronics manufacturing in the United States.
Considering the Future of Impending Copper Tariffs
07/30/2025 | I-Connect007 Editorial TeamThe Global Electronics Association is alerting industry members that a potential 50% tariff on copper could hit U.S. electronics manufacturers where it hurts.
Connect the Dots: Sequential Lamination in HDI PCB Manufacturing
07/31/2025 | Matt Stevenson -- Column: Connect the DotsAs HDI technology becomes mainstream in high-speed and miniaturized electronics, understanding the PCB manufacturing process can help PCB design engineers create successful, cost-effective designs using advanced technologies. Designs that incorporate blind and buried vias, boards with space constraints, sensitive signal integrity requirements, or internal heat dissipation concerns are often candidates for HDI technology and usually require sequential lamination to satisfy the requirements.
OKI Launches Rigid-Flex PCBs with Embedded Copper Coins Featuring Improved Heat Dissipation for Space Equipment Applications
07/29/2025 | BUSINESS WIREOKI Circuit Technology, the OKI Group’s printed circuit board (PCB) business company, has developed rigid-flex PCBs with embedded copper coins that offer improved heat dissipation for use in rockets and satellite-mounted equipment operating in vacuum environments.
Designers Notebook: Basic PCB Planning Criteria—Establishing Design Constraints
07/22/2025 | Vern Solberg -- Column: Designer's NotebookPrinted circuit board development flows more smoothly when all critical issues are predefined and understood from the start. As a basic planning strategy, the designer must first consider the product performance criteria, then determine the specific industry standards or specifications that the product must meet. Planning also includes a review of all significant issues that may affect the product’s manufacture, performance, reliability, overall quality, and safety.