-
-
News
News Highlights
- Books
Featured Books
- pcb007 Magazine
Latest Issues
Current IssueThe Hole Truth: Via Integrity in an HDI World
From the drilled hole to registration across multiple sequential lamination cycles, to the quality of your copper plating, via reliability in an HDI world is becoming an ever-greater challenge. This month we look at “The Hole Truth,” from creating the “perfect” via to how you can assure via quality and reliability, the first time, every time.
In Pursuit of Perfection: Defect Reduction
For bare PCB board fabrication, defect reduction is a critical aspect of a company's bottom line profitability. In this issue, we examine how imaging, etching, and plating processes can provide information and insight into reducing defects and increasing yields.
Voices of the Industry
We take the pulse of the PCB industry by sharing insights from leading fabricators and suppliers in this month's issue. We've gathered their thoughts on the new U.S. administration, spending, the war in Ukraine, and their most pressing needs. It’s an eye-opening and enlightening look behind the curtain.
- Articles
- Columns
- Links
- Media kit
||| MENU - pcb007 Magazine
Orbotech’s Latest Technology at IPC APEX EXPO
May 2, 2016 | Barry Matties, I-Connect007Estimated reading time: 8 minutes
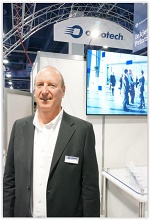
Orbotech presented their latest new technologies at IPC APEX EXPO 2016. The Nuvogo 1000 is a higher power version of their multi wavelength direct imaging machine, as well as their new automated optical shaping technology which can add copper deposition to an otherwise defective PCB. I met with Orbotech’s Micha Perlman in their booth on the show floor, to learn more.
Barry Matties: Micha, you are the senior marketing manager for the PCB division. I think that most people in our industry know Orbotech, but just for some context, tell us a little about the company.
Micha Perlman: Orbotech is a worldwide company focused on providing manufacturing equipment to the electronic industry. We have a wide variety of products, usually high-tech optical and digital products. We have been involved in the business of PCBs for many years as well as in the flat-panel display business, and lately we also entered into the advanced packaging market.
Matties: Your well-known AOI was kind of the starting point for Orbotech, right?
Perlman: Yes, but this was a long time ago. We are still the market leaders in AOI for PCBs and for flat-panel displays, but today that’s only a small part of our business. Many years ago, we moved to production machines and brought unique laser direct imaging to the PCB market, which we lead today as well.
We are also involved in other areas like the production of advanced packaging. We are proud to say that any electronic product that you hold in your hands today has more than one component which was manufactured using Orbotech solutions. It could range from the LCD or the touchscreen of your mobile phone to the PCBs or the components inside.
Matties: I've heard the revenue numbers for Orbotech and they're just incredibly large numbers. You guys really have a lot of resources to apply into R&D. It looks like you invest a lot back into R&D.
Perlman: That's right. We invest a high percentage of our revenue—typically about 13%—into R&D. This is a very high number for a capital solution business like ours that offers equipment for production.
Matties: What is the North American market like for Orbotech?
Perlman: It's a market that we have been leading for many years. It used to be our largest market, but then there was a shift to the Pacific and China. It is still a very important market for us where expensive, complicated and ‘one-off’ products are manufactured. We see a lot of military and aerospace applications that rely on Orbotech’s manufacturing expertise. I hear a lot of appreciation from the North American PCB manufacturers for what Orbotech’s solutions provide, how we enable them to meet the advanced technical requirements of PCB production here in America.
Matties: Well, direct imaging certainly makes a lot sense, especially here in America. There’s a lot more competition that has come into that arena. How has that impacted your strategies?
Perlman: At Orbotech, we never stand still. We are always looking at new ways to improve and stay ahead of the competition in terms of the quality, the speed and the performance of our products. Direct imaging is, as you say, very important for North America, and very important for the manufacturing of advanced smartphones in the Pacific. There is no way to manufacture a smartphone without having the direct imaging equipment, and it’s better to have Orbotech equipment because of its superior quality and lower total cost of ownership.
Matties: What sort of demands do your customers put on you, as far as the types of technology, the terms, or the requirements?
Perlman: We have very close relationships with our customers. We talk to them a lot, share our plans with them and they share their needs with us. When they are asked to develop tougher, more advanced PCBs they come to us to see how and if we can meet those needs. As our roadmap is defined well in advance, we are often ready with the solutions they need and we help them to ramp up their production of their increasingly complex products.
Matties: Here at the show, are you showing some new technology?
Perlman: Yes, definitely. There is one new product and one new technology that we are showing here. The Nuvogo™ 1000 is a new direct imaging machine that significantly enhances the power and the printing speed of the Nuvogo family that was introduced 18 months ago,
At the end of 2014, we introduced direct imaging technology with multi wavelengths that gives a much better imaging quality. For that, we moved from solid-state laser technology to laser diodes which enables the multi wavelength and the higher energy that give the DI better quality, better adhesion, better sidewalls and higher throughput.
Matties: How do the demands from a North American shop differ from the demands from a Chinese facility? Are there different requirements in terms of the relationship between you and your customers?
Perlman: There are fundamental differences in the business models between North America and China. In China, the focus is largely on high volume and low cost, both for simple and for very advanced products. Their business model is focused on pushing the production cost down—high speed, high efficiency and low cost of ownership.
Here in North America, the emphasis is more on advanced engineering to support low volume production of unique products. In the Pacific, it is not unusual to see an entire fab dedicated to one production line for a period of three or four months. In America, different and unique products are manufactured every day requiring a lot of engineering resources, experience, knowledge and advanced tools in order to deliver the required results.
Matties: Does that create a challenge for Orbotech, in terms of the technology itself?
Perlman: It does, but as a result of our vast experience and unique global view, we have comprehensive solutions. We have a wide range of products and solutions, and we have the flexibility to support different applications and different requirements. We also have very experienced engineers and field experts that enable our customers to get the most from our solutions, whether we’re talking about our high-capacity, high-quality, high-yield, advanced fab customers in the Pacific or the specific technological challenges of the American market.
Page 1 of 2
Suggested Items
The Evolution of Picosecond Laser Drilling
06/19/2025 | Marcy LaRont, PCB007 MagazineIs it hard to imagine a single laser pulse reduced not only from nanoseconds to picoseconds in its pulse duration, but even to femtoseconds? Well, buckle up because it seems we are there. In this interview, Dr. Stefan Rung, technical director of laser machines at Schmoll Maschinen GmbH, traces the technology trajectory of the laser drill from the CO2 laser to cutting-edge picosecond and hybrid laser drilling systems, highlighting the benefits and limitations of each method, and demonstrating how laser innovations are shaping the future of PCB fabrication.
Day 2: More Cutting-edge Insights at the EIPC Summer Conference
06/18/2025 | Pete Starkey, I-Connect007The European Institute for the PCB Community (EIPC) summer conference took place this year in Edinburgh, Scotland, June 3-4. This is the third of three articles on the conference. The other two cover Day 1’s sessions and the opening keynote speech. Below is a recap of the second day’s sessions.
Day 1: Cutting Edge Insights at the EIPC Summer Conference
06/17/2025 | Pete Starkey, I-Connect007The European Institute for the PCB Community (EIPC) Summer Conference took place this year in Edinburgh, Scotland, June 3-4. This is the second of three articles on the conference. The other two cover the keynote speeches and Day 2 of the technical conference. Below is a recap of the first day’s sessions.
Preventing Surface Prep Defects and Ensuring Reliability
06/10/2025 | Marcy LaRont, PCB007 MagazineIn printed circuit board (PCB) fabrication, surface preparation is a critical process that ensures strong adhesion, reliable plating, and long-term product performance. Without proper surface treatment, manufacturers may encounter defects such as delamination, poor solder mask adhesion, and plating failures. This article examines key surface preparation techniques, common defects resulting from improper processes, and real-world case studies that illustrate best practices.
RF PCB Design Tips and Tricks
05/08/2025 | Cherie Litson, EPTAC MIT CID/CID+There are many great books, videos, and information online about designing PCBs for RF circuits. A few of my favorite RF sources are Hans Rosenberg, Stephen Chavez, and Rick Hartley, but there are many more. These PCB design engineers have a very good perspective on what it takes to take an RF design from schematic concept to PCB layout.