Sustainable Nanotechnology
May 3, 2016 | DTUEstimated reading time: 2 minutes
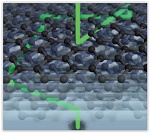
Corrosion protection with graphene
In a world where at least 3 % of the GDP of developed countries are being used to protect against or rebuild after corrosion, better barrier materials would make a large impact, prolonging the life time for the objects exposed to corrosion and reducing the consumption of resources.
Since its isolation in 2004, graphene has drawn huge attention due to its unique electrical properties, but more recently its mechanical and chemical properties are being more heavily investigated. Single layers of graphene are impermeable even for molecules as small as hydrogen, making graphene the perfect barrier.
When graphene protective coatings are taken out of the lab, however, things are less perfect. Even though graphene is the strongest material known relative to its size, a single atomic layer of any material is still easily damaged. When metal, graphene and a corrosive liquid are exposed at the same time, an electrochemical process called galvanic corrosion can in some cases even enhance the corrosion rate – and this may only show up after extended durations of time.
“However,” PhD Student Adam Stoot says “we can grow graphene directly on a catalytic metal surface, and when we use nickel, the graphene typically forms relatively thick coatings – with hundreds of layers. Even a 100 nm thick coating with 300 layers is still extremely thin compared to conventional, micrometre thick coatings for corrosion protection”.
Researchers from DTU Nanotech in collaboration with SP Group A/S have grown such multilayer graphene coatings and have proved longer term performance of graphene coatings in highly corrosive boiling saline solutions. An effective and also conducting coating can have a profound impact in several application areas such as fuel cells, batteries, sensors and contacts.
Test chip with several CZTS solar cells and their metal contacts. Cell thickness is 2 micrometres.
Thin film solar cells
In solar cells, the materials responsible for converting sunlight into electricity are semiconductors. In those materials, first, electrons have to overcome a moderate energy gap by exploiting the energy of sunlight, and then, they can contribute to the electric current in the solar cell.
The current standard solar cell semiconductor, silicon, has an energy gap of the indirect type. As predicted by quantum mechanics, an indirect gap allows only weak absorption of light. Therefore, silicon needs to be at least 200 micrometres thick to absorb all sunlight. On the other hand, sulphur based semiconductor compounds such as Cu2ZnSnS4 (CZTS) or Cu2SnS3 (CTS) have an energy gap of the direct type. They absorb light more than 200 times better than silicon and their thickness can be cut down to 0.8 micrometres, thus saving a lot of resources. For this reason, we call them "thin-film solar cells".
Still, the actual laboratory efficiency of CZTS and CTS is mostly below 10%, whereas silicon excels with 25% in large scale production. PhD student Andrea Crovetto explains that “to improve the efficiency, we need to address a major challenge with these materials, namely the phase purity. Because there are many chemical elements involved in those compound semiconductors, we have to find synthesis methods that result in the correct, pure material with fairly large crystals so that crystal defects and loss of light-excited electrons are reduced”.
Suggested Items
The Pulse Design: Constraints for the Next Generation
07/16/2025 | Martyn Gaudion -- Column: The PulseIn Europe, where engineering careers were once seen as unpopular and lacking street credibility, we have been witnessing a turnaround in the past few years. The industry is now welcoming a new cohort of designers and engineers as people are showing a newfound interest in the profession.
Copper Price Surge Raises Alarms for Electronics
07/15/2025 | Global Electronics Association Advocacy and Government Relations TeamThe copper market is experiencing major turbulence in the wake of U.S. President Donald Trump’s announcement of a 50% tariff on imported copper effective Aug. 1. Recent news reports, including from the New York Times, sent U.S. copper futures soaring to record highs, climbing nearly 13% in a single day as manufacturers braced for supply shocks and surging costs.
Symposium Review: Qnity, DuPont, and Insulectro Forge Ahead with Advanced Materials
07/02/2025 | Barb Hockaday, I-Connect007In a dynamic and informative Innovation Symposium hosted live and on Zoom on June 25, 2025, representatives from Qnity (formerly DuPont Electronics), DuPont, and Insulectro discussed the evolving landscape of flexible circuit materials. From strategic corporate changes to cutting-edge polymer films, the session offered deep insight into design challenges, reliability, and next-gen solutions shaping the electronics industry.
Indium Corporation Expert to Present on Automotive and Industrial Solder Bonding Solutions at Global Electronics Association Workshop
06/26/2025 | IndiumIndium Corporation Principal Engineer, Advanced Materials, Andy Mackie, Ph.D., MSc, will deliver a technical presentation on innovative solder bonding solutions for automotive and industrial applications at the Global Electronics A
Gorilla Circuits Elevates PCB Precision with Schmoll’s Optiflex II Alignment System
06/23/2025 | Schmoll MaschinenGorilla Circuits, a leading PCB manufacturer based in Silicon Valley, has enhanced its production capabilities with the addition of Schmoll Maschinen’s Optiflex II Post-Etch Punch system—bringing a new level of precision to multilayer board fabrication.