Stepping up to Laser Processing for Flex, Part 3: Readiness and Site Preparation
May 4, 2016 | Mike Jennings and Patrick Riechel, ESIEstimated reading time: 8 minutes
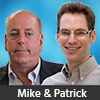
This six-part series will examine how to effectively supplement your flex production capabilities with laser processing.
Supplementing your production capabilities with flexible circuit laser processing can pay big dividends. It not only widens the scope of customers whom you can service, but it also extends your reach into additional markets you might not be well-equipped to serve otherwise. Employing laser technology is one of the best ways to stay current in PCB processing, as it enables you to achieve manufacturing flexibility and agility with more accurate and/or smaller features than is possible with mechanical processing. The purpose of this six-part series is to arm you with enough information to understand the opportunities and applications related to flex laser processing and to provide a clearer picture of how the implementation of laser processing capabilities can help to further optimize your production.
In part 2 of this series, we provided an overview of the various cost and benefit components related to flex laser processing, and how those components can be managed to allow you to gain the efficiencies that ultimately drive lower cost of ownership. It outlined what you should expect—and what areas you should focus on—when considering the costs and benefits associated with FPC processing.
In Part 3, it’s time to consider the factors associated with actually bringing flex laser processing systems on site so you can begin to reap the benefits.
Introduction
It’s fairly common for manufacturers to overlook some of the cost factors associated with upgrading facilities to accommodate the addition of new processing methodologies. For PCB manufacturers considering the addition of laser processing for flex circuit production, there is an entirely new set of considerations to be aware of and to manage effectively, if they plan to step into flex PCB laser processing. Getting a handle on those issues early helps to avoid common and costly issues once they’re actually in production.
Typical areas to investigate when it comes to proper site preparation for laser systems include the site’s electrical power configuration, vacuum removal capabilities, compressed air availability, environmental air management, and the adequate control of temperature and humidity. Neglecting any of these can result in poor product yield, scrap or even damage to—and downtime of—your valuable UV laser system. Furthermore, it is often extremely difficult to isolate process issues from system and site issues once you’re up and running. So, obviously, it’s best to ensure that your site fully meets requirements before those yield and scrap and issues occur in production.
Temperature and Humidity Control
Flex material processing requires an environment with stable temperature and humidity levels. The accuracies that are typically required for flex processing require a much more stringent environmental control regimen than what is necessary for other PCB processing methodologies. Both the laser system and the flex material itself are sensitive to changes in temperature and humidity.
As flex processing continues to push the envelope of ever-finer lines, smaller vias and smaller pads, the level of drilling accuracy must also increase. Given the high accuracy requirements associated with flex processing, it’s necessary to minimize the impact of shifts in humidity and temperature, not only in the drilling room, but also for downstream processes.
System accuracy and spot quality can be affected by temperature changes due to a variety of reasons, including alignment issues associated with the thermal expansion and contraction of the system frame, a shift in optics alignment, thermal errors, etc. Certain optics coatings can also be compromised by shifts in humidity. When combined with the impact of those same temperature and humidity shifts on the dimensional stability of your flex material, accurate drilling requires the control of many variables.
Air conditioning vent placement and associated lack of air mixing is often overlooked when considering temperature control. Your thermostat and temperature monitor might be registering tiny temperature fluctuations far away from the air conditioning vents. However, if your laser system is placed directly underneath one of those vents without taking measures to baffle and mix that cold or hot air with the ambient air, your laser system could be experiencing much higher temperature fluctuations! Similarly, be aware of any large heat-generating sources and how they are placed and vented relative to your laser tools.
Another commonly overlooked issue is related to the environmental conditions that your system is initially calibrated in. If your laser system is installed and calibrated in summer at a high factory temperature and humidity, you may find that letting the temperature and humidity significantly drop in winter in order to save on utility costs can cause process accuracy or quality issues. Similarly, if you plan factory shutdowns where you turn off your HVAC or have just moved the system into your facility, make sure to let the system “soak” and stabilize at the set temperature for several hours prior to calibration or processing.
Electrical Power
Poor power quality, not to mention power outages and sporadic brownouts, can result in unexpected system errors, yield issues, and scrap. While much of this can be controlled through the use of quality voltage regulators, power conditioners and uninterruptable power supplies (where needed), it’s best to start at the source and ensure that clean, conditioned and reliable power is made available to your laser processing system. While blackouts are perhaps the most obvious contributor to scrap, brownouts and power quality issues can be the most problematic. This is due to the fact that the symptoms of brownouts and power quality issues can look very similar to process and system issues while in fact the root cause is poor input power. Electrical service should be provided by a qualified electrician and should meet local code and regulation.
Vacuum
Flex circuit laser processing equipment typically include debris removal vacuum functionality and a vacuum chuck to hold the flexible, malleable and easily-damaged sheets in a stable and flat position. While many equipment manufacturers offer the addition of a standalone vacuum pump, it is often more cost-effective to use existing facilities vacuum, especially if considering a multi-system installation. Doing so, however, carries some risks if the implications of multiple systems on a single vacuum line are not considered. When installing your new laser equipment, take time to review your facility vacuum capabilities and plumbing architecture. Before the final step of placing your systems into production, test vacuum pressure and flow rate at each system input when all systems are in operation to verify your facilities under a realistic production scenario.
A commonly overlooked issue occurs during equipment capacity expansions—even if a given pump and plumbing meets system requirements before the expansion, additional vacuum branching after expansion can cause overall vacuum loss that results in insufficient pressure. Another common mistake is to test the vacuum pressure and flow when other systems have their debris vacuum off or their chuck vacuum fully covered, both of which do not represent the worst-case production scenario. As a practice, vacuum pressure and flow should be tested again after all equipment is hooked up to the vacuum system and in operation with real panel material—ideally with a production application that exposes the highest number of open vacuum holes on the vacuum chuck.
Test with worst-case typical vacuum leakage on all system vacuum chucks with debris removal on for all systems
Vacuum facilities with inadequate pressure and flow can prevent the system’s debris removal from doing its job properly. This can result in damage to the system’s optics over time, since the particles ejected during laser processing are not effectively removed, can settle on the nearby optics, and eventually burn onto those optics. Missing or incompletely-drilled vias can also be caused by poor debris removal due to optics contamination and the debris and processing plasma interfering with the laser reaching the work piece. Finally, insufficient vacuum can also be the cause of panel movement or non-flat panel material on the system’s vacuum work table, resulting in a decrease in yield.
Page 1 of 2
Suggested Items
OSI Systems Lands $17 Million Order for Cargo and Vehicle Inspection Systems
07/07/2025 | BUSINESS WIREOSI Systems, Inc. announced that its Security division received an order valued at approximately $17 million from an international customer for cargo and vehicle inspection systems.
KYOCERA AVX Releases New 3DB Hybrid Couplers
07/04/2025 | PRNewswireKYOCERA AVX, a leading global manufacturer of advanced electronic components engineered to accelerate technological innovation and build a better future, released a new line of integrated thin film (ITF) hybrid couplers designed to facilitate the continued evolution of high-frequency wireless systems in industrial, automotive, telecommunications, and telemetry applications.
Accenture Acquires SYSTEMA to Drive Manufacturing Automation for Semiconductor Clients
07/02/2025 | AccentureAccenture has acquired SYSTEMA, a provider of software solutions and consulting services for manufacturing automation, headquartered in Dresden, Germany.
Driving Innovation: Direct Imaging vs. Conventional Exposure
07/01/2025 | Simon Khesin -- Column: Driving InnovationMy first camera used Kodak film. I even experimented with developing photos in the bathroom, though I usually dropped the film off at a Kodak center and received the prints two weeks later, only to discover that some images were out of focus or poorly framed. Today, every smartphone contains a high-quality camera capable of producing stunning images instantly.
Specially Developed for Laser Plastic Welding from LPKF
06/25/2025 | LPKFLPKF introduces TherMoPro, a thermographic analysis system specifically developed for laser plastic welding that transforms thermal data into concrete actionable insights. Through automated capture, evaluation, and interpretation of surface temperature patterns immediately after welding, the system provides unprecedented process transparency that correlates with product joining quality and long-term product stability.