Quantum Dots by Nature
May 10, 2016 | Lehigh UniversityEstimated reading time: 5 minutes
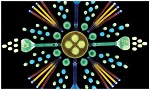
Lehigh researchers have successfully demonstrated the first precisely controlled, biological way to manufacture quantum dots. This one-step method starts with engineered bacterial cells in a simple, aqueous solution and ends with functional semiconducting nanoparticles, all without resorting to high temperatures and toxic chemicals.
Born of an ideal collaboration among three Lehigh faculty researchers, this elegant technique has great potential for green manufacturing of quantum dots (QDs), which are used in transistors, solar cells, LEDs, lasers and medical imaging. Current industrial processes to produce them are messy, requiring toxic solvents, heat and high pressure.
Bryan Berger, associate professor of chemical and biomolecular engineering and bioengineering, wondered in 2012 whether the bacterial strain Stenotrophomonas maltophilia could be manipulated to generate QDs on command, since it had previously been known to exhibit heavy metal resistance.
Berger teamed up with colleagues Steve McIntosh, associate professor of chemical and biomolecular engineering and member of Lehigh’s Class of ’61; Chris Kiely, the Harold B. Chambers Senior Professor of Materials Science and Engineering; Robert Skibbens, professor of biological sciences; and Ivan Korendovych, assistant professor of chemistry at Syracuse University. Together they won a $2 million grant in 2013 from NSF’s Division of Emerging Frontiers in Research and Innovation (EFRI) to prove the production of cadmium sulfide QDs using an engineered form of Stenotrophomonas. They tailored the bacteria to grow nanocrystalline metal sulfides including QDs, building on earlier research, which was funded by Lehigh’s Faculty Innovation Grant (FIG) and Collaborative Research Opportunity Grant (CORE) programs.
“The beauty of a biological approach is that it cuts down on the production needs, environmental burden and production time quite a lot,” says Berger. Industrial processes take many hours to grow the nanocrystals, which then need to undergo additional processing and purifying steps. On the other hand, biosynthesis takes minutes to hours maximum to make the full range of quantum dot sizes (about 2 to 3 nanometers) in a continuous, environmentally friendly process at ambient conditions in water that needs no post-processing steps to harvest the final, water-soluble product. Because bacterial cells are much larger than the nanocrystals, researchers simply use a centrifuge to pull the cells away from the QDs in the solution.
More recently, the researchers have branched into creating lead sulfide QDs and are working on oxide-based materials, widening the range of QD practical applications. Their underlying technique allows them to control the particle size to fractions of a nanometer, an essential function, since particle size determines the QD’s optical and electronic properties.
Cell-based growth needs only basic equipment in a typical biochemistry wet lab setting. Using a process called directed evolution, researchers altered the bacteria so they would selectively produce quantum dots. Housed in a beaker containing water, cadmium and sulfur precursors, and minimum levels of carbon and nitrogen, the cells forgo most normal biological functions. They build quantum dots by sequestering metal ions from their environment, generating a reactive sulfur source and controlling the resultant structure to form a crystal.
Perfecting the methodology to structurally analyze individual nanoparticles required a highly sophisticated Scanning Transmission Electron Microscope (STEM). Lehigh’s Electron Microscopy and Nanofabrication Facility was able to provide a $4.5 million state-of-the-art instrument that allowed the researchers to examine the structure and composition of each QD, which is only composed of tens to hundreds of atoms.
“Even with this new microscope, we’re pushing the limits of what can be done,” says Kiely. The instrument scans an ultra-fine electron beam across a field of QDs. The atoms block the electrons in the beam, producing a kind of shadow image on a fluorescent screen, akin to the way an object blocking light produces a shadow on the wall. A digital camera records the highly magnified atomic resolution image of the nanocrystal for analysis.
Page 1 of 2
Suggested Items
Frank Silva teams up with Technica USA as PCBA Representative for Southern CA and Southern NV Territories
07/16/2025 | Technica USATechnica USA is pleased to announce the partnership with veteran Frank Silva as our PCBA Sales Representative, supporting both supply partners and PCBA customers across Southern California and Southern Nevada.
Hon Hai Scholarship Whale Exchange and Growth Camp Empowers Winners and Helps Build Connections
07/16/2025 | Hon Hai Technology GroupThe "2025 Hon Hai Whale Scholarship Exchange and Growth Camp" hosted by the Hon Hai Education Foundation came to a successful conclusion on July 12.
Flexible Circuit Technologies Welcomes Regional Business Development Manager Derek Rossberg
07/15/2025 | Flexible Circuit TechnologiesFlexible Circuit Technologies a Minnesota-based flexible circuit and advanced electronics contract manufacturer, welcomes Derek Rossberg as Regional Business Development Manager.
Electronics Manufacturing & Assembly Collaborative (EMAC) Announces Innovative Student Competition
07/15/2025 | EMACThe Electronics Manufacturing & Assembly Collaborative (EMAC) recently announced the launch of the Bright Manufacturing Challenge 2025, a revolutionary hands-on competition that transforms how students experience electronics manufacturing and robotics engineering.
Delta Electronics Thailand Ranked Among Asia’s Top Corporates at the Alpha Southeast Asia 15th Institutional Investor Awards
07/14/2025 | Delta ElectronicsDelta Electronics (Thailand) Public Company Limited, a global leader in power management and smart green solutions, has been recognized by global investors for its excellence in investor relations and corporate governance, earning top ranking in the “Most Improved Investor Relations” at the Alpha Southeast Asia 15th Annual Institutional Investor Awards for Corporates, held on June 30, 2025, in Singapore.