Institute of Circuit Technology Annual Symposium
June 14, 2016 | Pete Starkey, I-Connect007Estimated reading time: 11 minutes
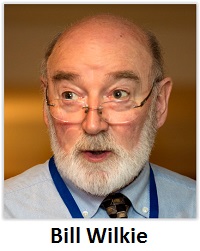
On June 1, Technical Director Bill Wilkie introduced the 42nd Annual Symposium of the Institute of Circuit Technology, at the Motorcycle Museum in Birmingham, UK, commenting upon the success of the recent Foundation Course and acknowledging the sterling efforts of his course tutors, although recognising that some of his longest-standing experts were now retiring. With Institute membership currently standing at 422, there existed a wealth of talent from which he hoped to strengthen his team.
Keynote presentation came from EIPC chairman Alun Morgan, with a highly informative and occasionally humorous insight into the evolution of automotive electronics, from 1886, when Karl Benz produced the first petrol-engined automobile, which at least had an electrical ignition system, to the present day where, in a world automotive market worth $600 billion, electronics represents 40% of the value. There had been rapid growth over the last decade, as a consequence of developments in lightweight materials, miniaturization, intelligence and electrification.
The first introduction of electronics into the automobile was in 1930, with Motorola’s car radio, costing over $100 before installation—which was a major job occupying two men for several days and involved substantial modification to the bodywork and interior trim. The installation manual had 28 pages of instructions!
Once in-car entertainment had become established— radio, 8-track stereo, cassette tape and CD player along the way—the next generation of automotive electronics was engine management, with the Bendix Electrojector electronic fuel injection system in 1958, although the early electronic components were not reliable in under-the-hood service. The technology progressed through the 1960s, and the Bosch D-Jetronic became the industry standard in1975. ABS braking evolved through the 1970s and 1980s, became the norm in the 2000s, and was an early example of the synchronisation of a group of inputs to execute a function as a system.
Presently, vehicle electronics could be grouped into four functional domains: 1) powertrain, including engine control, transmission control and start/stop systems; 2) control/body, including air conditioning and climate control, dashboard, wipers, lights, doors, seats, windows, mirrors, cruise control, park distance control, alarm, keyless entry; 3) multimedia/entertainment, including multimedia, infotainment, GPS and in-vehicle navigation systems, CD/DVD players, rear-seat entertainment; and 4) safety, including rollover sensors, airbags, belt pre-tensioners, antilock braking, electronic stability programs, automatic stability controls, adaptive cruise controls, tyre pressure monitoring systems and auto lane keeping. Morgan referred to an announcement by Toyota that they will integrate between 60 and 100 electronic control units into these four functional groups. He discussed layers of increasing integration, from the low-level electronic system platform, up through intelligent actuators and integrated vehicle control, to direct vehicle-to-vehicle interaction and the control of vehicle groups and fleets. The Internet of Things was driving the next generation of development, although there would inevitably be some issues related to the security of data and the protection of privacy that would have to be resolved.
Morgan switched his focus from electronic functionality to road safety trends. European statistics indicated a 26% reduction in annual road fatalities between 2009 and 2013, whereas the USA only achieved 3%, for reasons he could not explain. The fatality reduction forecast for intelligent vehicle safety systems indicated that electronic stability control and lane-keeping support had by far the greatest potential for reducing fatalities. Electronic stability programme sensors and systems for anticipating problems could take corrective actions faster, and with more functionality to control the vehicle, than even the most skillful of human drivers. And he illustrated their capabilities with scary but very convincing video case studies. Elegant collision avoidance radar systems were becoming available, having evolved from early prototypes in the mid-1970s, and the achievement of accident-free driving as the objective, and systems were migrating to higher operating frequencies as a means of offering a homogeneous concept for deployment in the mass market at affordable cost. The car was becoming an intelligent vehicle that understood what was going on around it as well as within it. On a salutary note: the more complex the electronics, the more to potentially go wrong - recall figures had shown a steep rise through the 2000s, and were plateaued at an uncomfortably high level.
Recently introduced all-electric vehicles—Morgan’s example was the Tesla-S—were mechanically far simpler than conventional vehicles: in essence, an assembly of batteries constituting the floor pan and an electric motor driving each wheel, with digital control of motors, brakes and steering, and active, traffic-aware cruise control effectively offering “autopilot” capability.
From automotive electronics, attention turned to metal finishing and printed circuit processing: Dr. Steven Brewer from C-Tech Innovation described the objectives and achievements of the REPRIME project, funded by the Home Office to investigate the application of advanced ultrasonics to enable the replacement of poisons and explosive precursors used in industrial metal finishing processes and the manufacture of printed circuit boards. The Home Office was conscious that quantities of chemicals which could support terrorist activities were held by SMEs in relatively unsecure locations, and wanted to work with industry associations to find alternative materials via technical solutions rather than by legislation. Objectives were to overcome the barriers to the use of cyanide-free technology, to demonstrate cyanide-free zinc and zinc-nickel plating on an industrial scale, to extend the work to cyanide-free copper, gold and silver plating, to reduce hydrogen peroxide use in the printed circuit industry and to ensure that the technology could be easily and cheaply retrofitted to existing equipment.
It had been demonstrated in a pilot line that the use of ultrasound enhanced the deposition rate of cyanide-free zinc electroplating plating chemistries and improved coverage and distribution on complex shapes. Ultrasound enabled the use of reduced concentrations of hydrogen peroxide in etchant solutions used in PCB manufacturing, and gave improved bath life with reduced frequency of replenishment and no adverse effect on downstream processing. The project had been successfully completed, and was being rolled out to industry with continuing support from the Home Office, the Surface Engineering Association and the ICT. Update information was available on the project website (www.reprime.co.uk).
Tamara den Daas-Wijnen, Ventec’s global account manager, OEM marketing, introduced the tec-speed™ product portfolio, which positioned Ventec’s comprehensive range of high-speed low-loss PCB laminates under a clear single-brand identity, symbolised by a sharp-pointed pyramid with standard-loss material at the base and ultra-low-loss at the apex. “Upwards is the direction we are going, as a technology leader—no longer a me-too!” was her comment. She described in detail the characteristics and properties of two examples from the range: tec-speed 3.0 (VT-464L) and tec-speed 6.0 (VT462S). tec-speed 3.0 was a high-Tg halogen-free low-loss material for telecom and networking applications, with Dk 3.7 and Df 0.009 at 50% resin content, which had better electrical properties and was more thermally robust than competitive products.
She quoted reliability results for a 32-layer, 4 mm thick construction with 0.3 mm holes at 0.8 and 1.0 mm pitch, withstanding 10 lead-free reflow cycles at 280°C without failure, and explained how Ventec’s glass treatment and resin-impregnation procedure led to remarkable improvements in CAF resistance. Similar thermal reliability results were achieved with the ultra-low-loss tec-speed 6.0 material. The electrical performance characteristics of tec-speed 6.0 were interesting, particularly the fact that at 10GHz its Df decreased with increasing resin content - a consequence of the resin having lower dielectric constant than the glass.
Ms. den Daas-Wijnen concluded her presentation by commenting that the whole of Ventec’s supply chain was accredited to AS9100C—the only laminate manufacturer able to make that claim. And the Ventec App was now available, with instant access to data for the whole product portfolio.
Industry analyst and ICT Council member Francesca Stern delivered her annual outlook on the global PCB and electronics industry, reviewing world trends in electronics and PCB production, and how they related to the industry in the UK.
Global electronics production, including components, for 2015 totalled $US 1,861 billion, with China accounting for 38%, the rest of Asia-Pacific 22%, Japan 7%, the Americas 18% and Western Europe 11%. Principal end-use markets were cellphone, standard PC, digital TV and automotive. Standard PCs and tablets were showing negative growth, but there was continuing growth in medical electronics and huge growth in IoT applications.
Electronic equipment production in Europe and North America remained strong in 2015 in the industrial, instrumentation and automation sectors. There had been little growth in the military sector, but it was forecast to increase slightly in 2016. Growth in infrastructure equipment for 4G long-term-evolution had slowed in 2015, but industrial and instrumentation electronics production grew in China. UK electronics production, which had grown 3% in 2014, had fallen by1% in 2015.
PCB production in Europe had declined by 3% and some recovery, but no growth, was expected in 2016. Growth had been low in North America and there had been further decline in Japan. Exchange rate fluctuations could lead to distortions of the figures; for example, measured in domestic currencies, there had been positive growth in Asia, but negative if measured in US dollars. The outlook for 2016 was that it would be similar to 2015, with a recovery towards the end of the year, and the next surge expected in 2017–2018.
Ms. Stern commented on recent updates to the Open General Export Licence (OGEL) by the UK government, which made it easier to export PCBs to most worldwide destinations for military contracts, and other more sensitive countries including China for aerospace and industrial-grade PCBs. The Export Control Organisation (ECO) was currently looking for feedback from PCB companies as to how these changes were affecting their business.
Page 1 of 2
Suggested Items
Koh Young Installs 24,000th Inspection System at Top 20 EMS
05/14/2025 | Koh YoungKoh Young, the global leader in True 3D measurement-based inspection and metrology solutions, proudly announces the installation of its 24,000th inspection system at a Top 20 Global EMS in Thailand.
Indium’s Karthik Vijay to Present on Dual Alloy Solder Paste Systems at SMTA’s Electronics in Harsh Environments Conference
05/06/2025 | Indium CorporationIndium Corporation Technical Manager, Europe, Africa, and the Middle East Karthik Vijay will deliver a technical presentation on dual alloy solder paste systems at SMTA’s Electronics in Harsh Environments Conference, May 20-22 in Amsterdam, Netherlands.
SolderKing Achieves the Prestigious King’s Award for Enterprise in International Trade
05/06/2025 | SolderKingSolderKing Assembly Materials Ltd, a leading British manufacturer of high-performance soldering materials and consumables, has been honoured with a King’s Award for Enterprise, one of the UK’s most respected business honours.
Knocking Down the Bone Pile: Gold Mitigation for Class 2 Electronics
05/07/2025 | Nash Bell -- Column: Knocking Down the Bone PileIn electronic assemblies, the integrity of connections between components is paramount for ensuring reliability and performance. Gold embrittlement and dissolution are two critical phenomena that can compromise this integrity. Gold embrittlement occurs when gold diffuses into solder joints or alloys, resulting in mechanical brittleness and an increased susceptibility to cracking. Conversely, gold dissolution involves the melting away of gold into solder or metal matrices, potentially altering the electrical and mechanical properties of the joint.
'Chill Out' with TopLine’s President Martin Hart to Discuss Cold Electronics at SPWG 2025
05/02/2025 | TopLineBraided Solder Columns can withstand the rigors of deep space cold and cryogenic environments, and represent a robust new solution to challenges facing next generation large packages in electronics assembly.