All About Flex: Common Flex Circuit Surface Finish Requirements
June 23, 2016 | Dave Becker, All Flex Flexible Circuits LLCEstimated reading time: 8 minutes
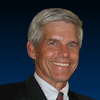
Copper is a unique metal and has been proven with the test of time in an incredible array of printed circuit and electrical wiring applications. It is highly conductive, has good flexibility properties, can withstand high temperatures and has good chemical resistance. Copper is also is in abundant supply and is fairly inexpensive. Copper does have one property requiring special processing attention: Copper corrodes at a faster rate than many other metals. This corrosion impedes bonding, soldering, fusing, and it creates high resistance in surface contact. Consequently, most flexible circuits and PC boards require a surface finish.
Most flex manufacturers offer a variety of surface finishes, as application requirements differ widely. Following are some typical applications and corresponding demand on the metal surface.
Surface Requirements
- Prepare for Soldering
Soldering is probably the most common post-fabrication operation for flexible circuits. Soldering is actually a fairly complex process as different metals flow together and combine to form a new alloy that creates an intermetallic layer. This intermetallic connection creates an excellent electrical and mechanical bond. Soldering requires a very clean surface and just about any degree of oxidation can impede the process, so the surface treatment needs to keep the copper oxide-free until soldering is completed. Sometimes the surface treatment is washed or dissolved away as part of the soldering process. In other cases the surface finish is a solderable metal that remains after the soldering application.
- Resistance to Surface Abrasion
Applications involving surface contact create a different challenge. Dome switches and pressure type connectors make multiple contact with the circuit and rely on a corrosion-free surface for adequate electrical contact. Since the mechanical abrasion can mar a soft surface, hardness to resist abrasion is a key feature.
- Wire Bond Assembly
Wire bonding places a different kind of requirement on the surface. Ideally the surface must be oxide-free and soft enough to form around the wire or ball that gets pressed against the surface with heat. The metal surface must be compatible with the metals used in wire bonding and be able to indefinitely hold a good electrical and mechanic connection. Both gold ball bonding and aluminum wedge bonding are widely used for direct chip attach components.
- Other
Another consideration when choosing a surface finish is flexing requirements. Metals such as tin, gold and solder may not be able to withstand flexing, so more pliable surface treatments may be required or a surface treatment needs selective application. Feature density is another factor that may eliminate some surface finishes as a viable option. For fine pitch components or small vias, the topography and thickness of the finish plays a critical part in successful component assembly.
Typical Surface Finishes
- Hot Air Solder Level (HASL)
- Hot air solder level is a common and fairly low-cost surface finish. The solder is applied by immersing a panel into molten solder and using hot air knives to remove the excess. HASL makes an ideal solder surface. A potential disadvantage of HASL is surface topography. The surface has some variation, and as component sizes continue to trend ever smaller, placement of small components can be affected.
- Tin-lead solder is usually a 63/37 eutectic blend, but HASL is also used with lead-free solder that is needed for RoHS compliance. Lead-free solder most commonly consists of 99% tin and a small percentage of copper or other doping agents. Lead-free solder flows at about 485degF, whereas the tin-lead solder will reflow at around 385degF. HASL is normally performed after the soldermask or coverlay operation so that it is applied only where needed.
- Requirements by the European Union in 2003 for RoHS compatibility have driven wide-spread adoption of lead-free solders. These alternatives can be applied with both HASL processes and screened/reflowed processing.
- Electrolytic Tin Plating (RoHS Compliant)
Tin plating is another solderable finish and is also used as a general anti-corrosion protection. Tin plating is often used as an etch resist for plated through-hole fabrication and is then chemically removed before coverfilm lamination. Tin plated traces will bend and flex, but extended flex life is poor and the surface is not used in dynamic flex applications. Tin is also susceptible to electro-migration known as “whiskering.” Typical tin thickness is 300 micro-inches.
- Immersion Silver (RoHS Compliant)
- Immersion silver treatment is most frequently used when solder paste contains silver for enhanced compatibility with subsequent soldering processes. Silver dissolves into the solder during the reflow process.
- While storage conditions affect shelf life, immersion silver is considered a surface with a limited shelf life. It should be soldered fairly soon after fabrication. Silver should not be left on the copper indefinitely as it is susceptible to dendritic growth.
- Silver also has a propensity to oxidize, but this is generally more of a cosmetic issue than a surface contact issue since silver oxide is actually very conductive. Immersion silver thickness is typically eight micro-inches.
- Immersion Tin
- Immersion tin will behave similarly to immersion silver. It is coated to about 40 micro-inches thick and will do well for short term oxidation prevention. Over time tin will oxidize and can also experience dendritic growth issues.
- Immersion tin is another surface that should not be used on areas that get a high degree of flexing or bending.
- Immersion tin over copper forms an intermetallic layer. Over time, the copper-tin intermetallic layer continues to grow. Soldering must be done to the tin and cannot be done directly to the intermetallic alloy. If too much time passes, there won’t be enough tin left for adequate soldering.
- Gold and soldering
- A gold-plated surface is very receptive to solder as gold will dissolve into the solder during reflow. Too much gold can cause solder joint embrittlement, however, a gold layer thickness of 10 micro-inches or less is considered safe for solder paste reflow.
- Gold can be more problematic in wave soldering where the gold dissolves into the wave and is washed into the solder supply. Over time, the percentage of gold continues to increase in the solder pot. As gold accumulates in the solder, the solder joints may become embrittled and eventually unreliable. With wave soldering, the solder pot must be continually tested for gold. If the gold content approaches 3% by weight, then the solder needs to be replenished.
- Hard Gold over Nickel (RoHS compliant)
- Applications requiring a highly conductive surface contact create a different challenge. Hard gold is often the selected surface finish with tactile metal domes, formed rubber domes, and pressure type connectors. These copper features rely on a corrosion-free surface for low resistance electrical contact. In these cases the surface finish needs to be wear resistant with multiple insertions and/or contacts a common requirement.
- An electrolytic hard gold surface is solderable but the additives that harden gold may make the process more difficult. Flexibility of this plated surface can also be an issue. While the gold itself is very flexible, the nickel barrier metal is somewhat brittle. Hard gold over nickel is often acceptable for limited flexing, such as flex to install, but not recommended for areas that are exposed to frequent or sharp bending.
- Typical thickness specifications are 20–30 micro-inches for gold and 50–200 micro-inches for nickel.
- Electroplated Soft Gold over Nickel (RoHS compliant)
- Soft gold is typically used for gold ball wire bonding for direct chip attach component assembly processing. Soft gold does provide a solderable surface, but would be an expensive choice if no wire bonding is needed. Electroless nickel immersion gold (ENIG) would be a more suitable choice when standard surface mount soldering is required.
- Like most of the metal surface finishes, soft gold/nickel must be kept away from areas that bend or flex. Soft gold thickness can vary from 3–20 micro-inches.
- ENIG (RoHS compliant)
- ENIG is considered by many to be the ideal surface for solder paste reflow. Not only does the surface easily accept solder, but it is very smooth, allowing easier placement of small components. ENIG is also an acceptable surface for direct chip attach with aluminum wire bonding.
- The electroless nickel is used as a barrier metal between the gold and copper to prevent copper from migrating into the gold and avoid corrosion by galvanic action.
- Immersion gold is thin enough so it does not create a problem with gold embrittlement. Typical thicknesses for ENIG are 3 micro-inches for gold, 120 micro-inches for nickel.
- Organic Coating—OSP (RoHS compliant)
OSP is the most environmentally friendly surface treatment and is fairly inexpensive. OSP is applied by spraying or dipping and typically is formulated to only bond to copper. OSP has a limited shelf life and while it does a reasonable job of inhibiting corrosion, an aggressive flux is usually required for successful soldering. OSP should be considered a short term anti-oxidant. Typical thickness is around 1.5 micro-inches.
A flexible circuit design might be imagined to include an area that gets wire bonded, another area that has SMT assembly, and yet another area may require multiple connector insertions. This creates a temptation to specify multiple surface treatments on the same circuit part number. While a fabricator may be able to produce a part with these features, it can become a very expensive alternative. Masking and stripping plated regions adds several process steps, cost, and diminishes yield. Avoiding multiple surface finishes on the same part is a strong recommendation. An excellent resource for answering specific surface treatment questions would be a flexible circuit application engineer, who can help determine the optimum surface treatment needed after reviewing the application and design.
Dave Becker is vice president of sales and marketing at All Flex Flexible Circuits LLC.
Testimonial
"We’re proud to call I-Connect007 a trusted partner. Their innovative approach and industry insight made our podcast collaboration a success by connecting us with the right audience and delivering real results."
Julia McCaffrey - NCAB GroupSuggested Items
Indium Corporation Promotes Two Leaders in EMEA (Europe, Middle East, and Africa) Markets
08/05/2025 | Indium CorporationWith its commitment to innovation and growth through employee development, Indium Corporation today announced the promotions of Andy Seager to Associate Director, Continental Sales (EMEA), and Karthik Vijay to Senior Technical Manager (EMEA). These advancements reflect their contributions to the company’s continued innovative efforts with customers across Europe, the Middle East, and Africa (EMEA).
MacDermid Alpha Electronics Solutions Unveils Unified Global Website to Deepen Customer, Talent, and Stakeholder Engagement
07/31/2025 | MacDermid Alpha Electronics SolutionsMacDermid Alpha Electronics Solutions, the electronics business of Elements Solutions Inc, today launched macdermidalpha.com - a unified global website built to deepen digital engagement. The launch marks a significant milestone in the business’ ongoing commitment to delivering more meaningful, interactive, and impactful experiences for its customers, talent, and stakeholders worldwide.
KOKI to Showcase Analytical Services and New HF1200 Solder Paste at SMTA Guadalajara 2025
07/31/2025 | KOKIKOKI, a global leader in advanced soldering materials and process optimization services, will exhibit at the SMTA Guadalajara Expo & Tech Forum, taking place September 17 & 18, 2025 at Expo Guadalajara, Salón Jalisco Halls D & E in Guadalajara, Mexico.
Weller Tools Supports Future Talent with Exclusive Donation to SMTA Michigan Student Soldering Competition
07/23/2025 | Weller ToolsWeller Tools, the industry leader in hand soldering solutions, is proud to announce its support of the upcoming SMTA Michigan Expo & Tech Forum by donating a limited-edition 80th Anniversary Black Soldering Set to the event’s student soldering competition.
Koh Young Appoints Tom Hattori as President of Koh Young Japan
07/21/2025 | Koh YoungKoh Young Technology, the global leader in True 3D measurement-based inspection solutions, announced the appointment of Tom Hattori as President of Koh Young Japan (JKY).