Candor Improves Positive Acting Liquid Photoresist Process; Installs ENIPIG Line
June 28, 2016 | Candor IndustriesEstimated reading time: 1 minute
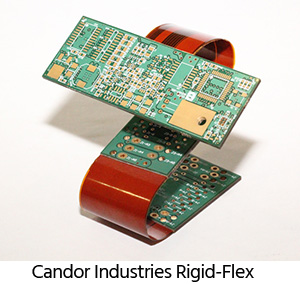
Toronto-based high technology circuit board manufacturer Candor Industries has recently taken steps to improve certain aspects of their fabrication processes.
The team has improved their rigid-flex manufacturing process utilizing positive acting liquid photoresist allowing them to do via filling on rigid areas. By improving their laminating processes and approaching rigid flex in a novel way they have successfully eliminated several processing steps in the manufacture 4-6 layer rigid flex. The elimination of these steps aligns with their simplified process criteria allowing the following to be available for their customers:
- 4-6 layer rigid flex can be done in 5 days
- Even dielectric across rigid areas
- Via filling capabilities for rigid-flex boards
In addition to the photoresist improvements Candor has also recently installed an ENIPIG (Electroless Nickel Immersion Palladium Immersion Gold) line. With the ever rising price of gold, Candor sought out a more affordable alternative to electrolytic nickel gold and electroless nickel electroless gold for their customers that resulted in the ENIPIG installation. Rather than putting 50 micro inches of gold, we put 2-4 micro inches of palladium, saving the customer money. In addition to the price, it also provides the combined benefits of exceptional shelf life, gold wire bondability, solder joint reliability and usage as a press contact surface.
Sunny Patel, Candor’s Technical Sales Manager states, “We’re always seeking new ways to improve our services for our customers. With these changes we’ve made a two pronged improvement by finding ways to lower costs and provide superior, faster products.”
About Candor Industries
Since 1999, Candor Industries has provided 21st Century customers with innovative PCB solutions for complex technologies through a commitment to service and support. Limitations created by standard manufacturing methods led Candor to invent and develop certain technological advancements, helping them to emerge in the forefront as a top of the line solutions provider. Candor continues to push the envelope of PCB manufacturing through continuous R&D, helping both customers and the industry to a brighter future. For more information about Candor, visit them on the web at www.candorind.com or contact Yogen Patel at (416) 736-6306.
Suggested Items
BEST Inc. Introduces StikNPeel Rework Stencil for Fast, Simple and Reliable Solder Paste Printing
06/02/2025 | BEST Inc.BEST Inc., a leader in electronic component rework services, training, and products is pleased to introduce StikNPeel™ rework stencils. This innovative product is designed for printing solder paste for placement of gull wing devices such as quad flat packs (QFPs) or bottom terminated components.
See TopLine’s Next Gen Braided Solder Column Technology at SPACE TECH EXPO 2025
05/28/2025 | TopLineAerospace and Defense applications in demanding environments have a solution now in TopLine’s Braided Solder Columns, which can withstand the rigors of deep space cold and cryogenic environments.
INEMI Interim Report: Interconnection Modeling and Simulation Results for Low-Temp Materials in First-Level Interconnect
05/30/2025 | iNEMIOne of the greatest challenges of integrating different types of silicon, memory, and other extended processing units (XPUs) in a single package is in attaching these various types of chips in a reliable way.
E-tronix Announces Upcoming Webinar with ELMOTEC: Optimizing Soldering Quality and Efficiency with Robotic Automation
05/30/2025 | E-tronixE-tronix, a Stromberg Company, is excited to host an informative webinar presented by Raphael Luchs, CEO of ELMOTEC, titled "Optimize Soldering Quality and Efficiency with Robotic Automation," taking place on Wednesday, June 4, 2025 at 12:00 PM CDT.
CE3S Launches EcoClaim Solutions to Simplify Recycling and Promote Sustainable Manufacturing
05/29/2025 | CE3SCumberland Electronics Strategic Supply Solutions (CE3S), your strategic sourcing, professional solutions and distribution partner, is proud to announce the official launch of EcoClaim™ Solutions, a comprehensive recycling program designed to make responsible disposal of materials easier, more efficient, and more accessible for manufacturers.