Booting up Spin-based Device Studies
August 16, 2016 | MITEstimated reading time: 3 minutes
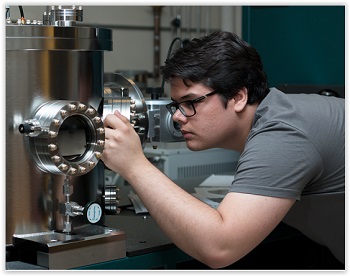
MIT Materials Processing Center (MPC)-Center for Materials Science and Engineering (CMSE) Summer Scholar Grant Smith is working in the lab of MIT assistant professor of electrical engineering and computer science Luqiao Liu, to create special thin film materials suitable for spin-based devices such as magnetic tunnel junctions used in computer memory.
For his summer project, Smith is operating a sputter deposition chamber, where he grows ultrathin films from 2 to 10 nanometers thick. He is making devices that are precursors to a memory device and measuring their properties.
Magnetic tunnel junctions used in spin-based systems for computer memory got their start with a key breakthrough in 1994 at MIT by research scientist Jagadeesh S. Moodera and colleagues. They are especially valued because they retain information even when the power is off.
A magnetic tunnel junction pairs two thin film materials, each with a special property called ferromagnetism. “Those ferromagnetic layers can either have their magnetizations aligned or anti-aligned,” Smith explains. If they are aligned, that is their magnetic fields both point in the same direction, the electrons in one layer will have more states available for them in the other layer, but if they are anti-aligned [with magnetic fields pointing in opposite directions], there will be fewer states for electrons available in that other layer.
Change in Resistance
“When you’re trying to push a current through and the magnetizations are aligned, the resistance is much lower. So if you fix one of the magnetic layers and flip the other one based on whether you want it to be a zero or a one or if you’re just trying to detect the existence of a magnetic field, you’ll be able to see something on the order of a 100 to 300 percent change in the resistance of that device,” Smith says. This is about 10 to 30 times greater that the approximately 10 percent shift in resistance in the first such devices.
Smith is working with a dual-layer of an antiferromagnet called iridium manganese and a ferromagnet called cobalt iron boron. “Those two in conjunction, when you condition them in a specific way, they pin the magnetization of the one ferromagnet in that one specific direction. So that is your fixed layer,” he explains.
For his summer project, Smith seeks to establish that ability to grow these magnetic tunnel junctions in Liu’s lab, and if that is a success, to try to manipulate that magnetization with the spin texture of a topological semimetal in order to do switching.
Nice spot to be
“I’m just happy to learn anything about this field basically,” says Smith, a rising senior at Penn State University majoring in physics, who hopes to pursue a doctorate in the sciences. “I’m glad to be learning how to manufacture these magnetic tunnel junctions. That’s a really important skill. They’re used everywhere as far as doing experiments in this field. They’re useful in industry. It’s actually a very nice spot to be in.”
Liu, who joined the MIT faculty in September 2015, says, “So far I have been very glad with Grant Smith's performance. Having a summer intern working in our lab does provide a good advantage to our research as it allows us to look into directions that we were not able to previously due to a shortage of manpower. Moreover, Mr. Smith is really diligent and smart. It is a very nice experience so far to work with such a motivated undergraduate student.”
For Smith, working in Liu’s lab on materials at room temperature is a change of pace from his work at Penn State on materials at extremely low temperatures in the range of 4 kelvins (-452.47 degrees Fahrenheit). “When you’re working with these sort of things you can learn about new behaviors, new scientific phenomenon,” he says. “Here everything is very room temperature focused working much closer towards, working much more closely with the place industry is at right now,” Smith says.
Suggested Items
The Pulse: Design Constraints for the Next Generation
07/17/2025 | Martyn Gaudion -- Column: The PulseIn Europe, where engineering careers were once seen as unpopular and lacking street credibility, we have been witnessing a turnaround in the past few years. The industry is now welcoming a new cohort of designers and engineers as people are showing a newfound interest in the profession.
Copper Price Surge Raises Alarms for Electronics
07/15/2025 | Global Electronics Association Advocacy and Government Relations TeamThe copper market is experiencing major turbulence in the wake of U.S. President Donald Trump’s announcement of a 50% tariff on imported copper effective Aug. 1. Recent news reports, including from the New York Times, sent U.S. copper futures soaring to record highs, climbing nearly 13% in a single day as manufacturers braced for supply shocks and surging costs.
Symposium Review: Qnity, DuPont, and Insulectro Forge Ahead with Advanced Materials
07/02/2025 | Barb Hockaday, I-Connect007In a dynamic and informative Innovation Symposium hosted live and on Zoom on June 25, 2025, representatives from Qnity (DuPont's electronics business), DuPont, and Insulectro discussed the evolving landscape of flexible circuit materials. From strategic corporate changes to cutting-edge polymer films, the session offered deep insight into design challenges, reliability, and next-gen solutions shaping the electronics industry.
Indium Corporation Expert to Present on Automotive and Industrial Solder Bonding Solutions at Global Electronics Association Workshop
06/26/2025 | IndiumIndium Corporation Principal Engineer, Advanced Materials, Andy Mackie, Ph.D., MSc, will deliver a technical presentation on innovative solder bonding solutions for automotive and industrial applications at the Global Electronics A
Gorilla Circuits Elevates PCB Precision with Schmoll’s Optiflex II Alignment System
06/23/2025 | Schmoll MaschinenGorilla Circuits, a leading PCB manufacturer based in Silicon Valley, has enhanced its production capabilities with the addition of Schmoll Maschinen’s Optiflex II Post-Etch Punch system—bringing a new level of precision to multilayer board fabrication.