Tin Whisker Mitigation Methodologies: Report from SMART Group, Part 1
December 1, 2016 | Pete Starkey, I-Connect007Estimated reading time: 8 minutes
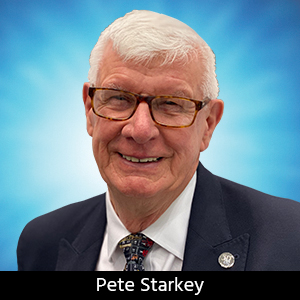
Since the introduction of the RoHS legislation in 2006, the threat of tin-whisker-related short circuit failure from pure tin finished components has remained a major concern within the high-reliability electronics manufacturing industry. But how do we set about mitigating against such failure where the use of pure tin finished components is unavoidable?
A distinguished group of experts gathered at Loughborough University in the East Midlands of the UK to share their knowledge with a room-full of engineers from the defence, aerospace and high-reliability electronics sector, at a seminar organised by SMART Group.
SMART Group Chairman Keith Bryant welcomed all present before inviting Technical Committee member Charles Cawthorne, Electronics Manufacturing Technologist with missile systems group MBDA, to moderate the proceedings.
Cawthorne’s first presenter was Dr Barrie Dunn, for many years Head of Materials and Processes Division with the European Space Agency, more recently Honorary Professor in the School of Engineering at the University of Portsmouth, and author of the newly published book, Materials and Processes for Spacecraft and High Reliable Applications. He began his presentation on problems associated with whisker growths with a remarkable time-lapse video recorded by researchers at Brown University, showing the initiation and growth of a tin whisker at a steady rate of about 1 micron per hour over a period of 40 hours.
The space environment presented particular challenges to electronic systems: high vacuum, low temperatures and thermal cycling as well as cosmic radiation, micrometeoroids and space debris. Remoteness and the inability to repair systems in situ obviously made the reliability issue even more critical, albeit for example Voyager 1 was still functioning after 39 years in operation. Although equipment designed to go into space was exempt from the RoHS Directive, the reliability of space projects clearly depended on the integrity of PCBs, components and assembly processes. Regarding whiskers, the aerospace industry standard GEIA-STD-0005-2 “Standard for Mitigating the Effects of Tin Whiskers in Aerospace and High Performance Electronic Systems,” revised in 2012, defined three control levels. Level 3, which was relevant to equipment designed to be sent into space, prohibited the use of pure tin finishes.
Dr Dunn showed a selection of illustrations from his “Black Museum” of whiskering effects on a wide variety of tin-plated components and connectors. And he quoted instances of systems failure in communications satellites originating from tin whiskers. A whisker one micron in diameter could support a current of 10 mA. Although higher currents would cause instant burn-out, in high-vacuum conditions a short circuit could result in a plasma discharge. Dr Dunn had collected data on whiskering effects over a period of 32 years, using the C-Ring test to introduce tensile and compressive stress, with different metal substrates, barrier layers and tin plating thicknesses, and the results were shortly to be published. A remarkable observation was that in some instances it could be several years before whiskers began to grow, depending on the substrate and stress level. Plated brass, tin-plated brass with a copper barrier layer, tin plated steel, tin-plated steel with a copper barrier layer, all displayed their own characteristics, sometimes predictable, sometimes not, but fused tin plating showed no whisker nucleation on any of these substrates during the 32 years of the study.
On behalf of ESA, a working group led by Dr Dunn had produced a comprehensive set of guidelines for creating a lead-free control plan, which described the problems, requirements and methods relevant to the preparation of a plan for companies to control against the use of lead-free components and to ensure that pure tin did not find its way into the manufacturing chain. He distributed copies to delegates, and it is available on-line for free download by clicking here.
Charles Cawthorne then introduced Dr Mark Ashworth of Loughborough University, who discussed the effect of plating methodologies, the first of two presentations describing research carried out at Loughborough into mechanisms and strategies for tin whisker mitigation. The factors influencing whisker growth were electroplating bath chemistry, whether pure tin or a tin alloy, bright or matte, electroplating parameters such as current density, temperature and agitation, and substrate, taking copper, brass and alloy 42 as examples. The deposit characteristics studied were thickness, grain size, morphology, orientation, intermetallic formation and elemental diffusion effects, under varying conditions of temperature, humidity, thermal cycling and applied external stress. A proprietary bright tin plating process was used.
The main conclusions were that bright tin electrodeposited onto copper did not always result in significant whisker growth, even after five years’ storage. Whisker growth was reduced by increasing deposit thickness and by deposition at higher current densities. The higher current densities tended to favour the formation of large eruptions, rather than filament whiskers. And it appeared that storage of tin deposits on copper for 5000 hours at 55°C and 85% humidity did not accelerate whisker growth, although these conditions favoured the formation of Cu3Sn intermetallic which was more planar than that developed at room temperature.
Pulse plating could be used as a means of manipulating the grain structure and orientation of the tin deposit, and in some instances showed reduced whisker growth compared with direct current deposits. But higher pulse frequencies could result in greatly accelerated whisker growth, which was believed to be favoured by fine grained columnar structures. Dr Ashworth stressed that these observations related to the particular proprietary electroplating chemistry used in the study, and that other commercial formulations might demonstrate different relationships between current density, deposit microstructure and whisker growth.
With Professor Geoff Wilcox taking over as moderator, Charles Cawthorne began his own presentation by remarking that, since first observed in 1946, and despite many years of study, the mechanism of tin whiskering was still not fully understood and predictive modelling was not yet possible. But, because of RoHS legislation, increasing numbers of components were only available with pure tin finishes. Consequently, manufacturers of high-reliability electronics with RoHS exemption were left with no alternative but to manage tin-lead obsolescence by avoidance or mitigation. He discussed the evolution of tin whisker mitigation methods via technical standards, with reference to the updated GEIA-STD-0005-2 standard already mentioned by Barrie Dunn, and the IEC/TS 62647-2 technical specification “Process Management for Avionics, Aerospace and Defence Electronic Systems containing Lead free Solder, Part 2: Mitigation of Deleterious Effects of Tin”, published in November 2012.
Page 1 of 2
Suggested Items
Silicon Mountain Contract Services Enhances SMT Capabilities with New HELLER Reflow Oven
07/17/2025 | Silicon Mountain Contract ServicesSilicon Mountain Contract Services, a leading provider of custom electronics manufacturing solutions, is proud to announce a significant upgrade to its SMT production capability with the addition of a HELLER 2043 MK5 10‑zone reflow oven to its Nampa facility.
Knocking Down the Bone Pile: Addressing End-of-life Component Solderability Issues, Part 4
07/16/2025 | Nash Bell -- Column: Knocking Down the Bone PileIn 1983, the Department of Defense identified that over 40% of military electronic system failures in the field were electrical, with approximately 50% attributed to poor solder connections. Investigations revealed that plated finishes, typically nickel or tin, were porous and non-intermetallic.
SHENMAO Strengthens Semiconductor Capabilities with Acquisition of PMTC
07/10/2025 | SHENMAOSHENMAO America, Inc. has announced the acquisition of Profound Material Technology Co., Ltd. (PMTC), a premier Taiwan-based manufacturer of high-performance solder balls for semiconductor packaging.
KYZEN to Highlight Understencil and PCB Cleaners at SMTA Querétaro Expo and Tech Forum
07/09/2025 | KYZEN'KYZEN, the global leader in innovative environmentally responsible cleaning chemistries, will exhibit at the SMTA Querétaro Expo & Tech Forum, scheduled to take place Thursday, July 24, at Centro de Congresos y Teatro Metropolitano de Querétaro.
Driving Innovation: Direct Imaging vs. Conventional Exposure
07/01/2025 | Simon Khesin -- Column: Driving InnovationMy first camera used Kodak film. I even experimented with developing photos in the bathroom, though I usually dropped the film off at a Kodak center and received the prints two weeks later, only to discover that some images were out of focus or poorly framed. Today, every smartphone contains a high-quality camera capable of producing stunning images instantly.