Patty’s Perspective: Everything Old is New Again
January 19, 2017 | Patty Goldman, I-Connect007Estimated reading time: 4 minutes
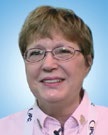
Happy New Year to all of you faithful and new readers out there! I hope you are looking forward to 2017 as much as we are here at I-Connect007. We have exciting plans for this year and can’t wait to get started, but first we need to talk about this month’s topic.
This month’s issue is all about plating and surface finishes; long ago, that was pretty much my start in the world of printed circuits—wet processing. So this is kind of my home turf—and not, since I haven’t worked in wet processing for some…well, for many years. I’ve always expected that I could hop right back onto the plating room floor and pick right up where I left off all those years ago. Or could I? Have things changed much? Time to read on and see.
So what is new in plating and surface finishes? Well it’s true that there are still the basic processes—cleaners and microetches, copper and nickel and gold electroplating, immersion tin, nickel, silver—all of which have been around for quite a long time. But with the finer features, the far greater reliability concerns, the lead-free solders, the constant need for lower cost and greater efficiency, etc., the spotlight is often on these “old” processes. Plus, there are a few new ones like ENIPIG.
Much research and development has gone into refining additives for electroplating and electroless/immersion baths to improve the plating quality in one way or another, both on surfaces and in through-holes and vias. Following on that is a tremendous amount of testing to prove out said processes and the subsequent assembly-ability of components. In the end, it’s all about reliability, reliability, and reliability.
There are a plethora of final finishes to choose from today. How does one decide? Well, that takes us right to the line-up for this month. Regular columnist Tara Dunn of Omni PCB has chosen that very subject so it seems appropriate to start with her column on how to choose a final surface finish.
Following this is a study of immersion gold processes—some of that R&D work I mentioned earlier. Don Gudeczauskas, et al, of Uyemura International, present a fine research paper on a comparative study of three immersion gold processes, looking at both solderability and wire bondability.
Lest anyone think that wet processes have no effect on electrical test, Gardien Services’ Todd Kolmodin is here to set the record straight with a look at the challenges that plating and surface finishes present to electrical test.
RBP Chemical Technology’s Michael Carano is Mr. Plating himself, and he gives us a detailed look at some of those things you might tend to overlook or perhaps take for granted in your acid copper plating process. Rather than talk about controlling the typical constituents, Mike looks beyond at tank parameters and the surrounding process steps.
We are fortunate to have another R&D article, this one by Ron Blake, et al, of MacDermid Enthone Electronics Solutions. They get into another relatively new area for copper electroplating, the filling of through-holes with copper.
Next, our own Pete Starkey reports on a MACFEST development project on a “univer sal surface finish,” namely ENIPIG (electroless nickel/immersion palladium/immersion gold).
This detailed report—including ample test data—has also been recorded as a webinar and can be viewed by clicking on the link near the end of the article.
In keeping with our policy of having a few general interest items for those chemistryphobes out there, we have no less than three columnists weighing in on the U.S. presidential election—in vastly different ways. IPC President John Mitchell starts with a discussion on how the Trump presidency and potential policy shifts may affect the electronics industry. He is followed by guest columnist John Hasselmann, IPC’s VP of Government Relations, with a discussion on corporate tax policy and possible changes that may come about with the new administration in Washington, DC.
Regular columnist Barry Lee Cohen compares the “fake news” from this past presidential campaign to the potentially false news that can and probably does occur within and about your own company. Barry also provides some concrete advice on how to keep the communication lines open so news and other information can be quickly disseminated—and any false “news” can be immediately combatted.
IPC APEX EXPO 2017 happens next month (see our calendar of events) and what better time to have our magazine focus on new technology—our topic for February. We expect there to be plenty for you to read about. You can subscribe now and have The PCB Magazine delivered to your inbox every month, giving you a head start on all things PCB.
Patricia Goldman is a 30+ year veteran of the PCB industry, with experience in a variety of areas, including R&D of imaging technologies, wet process engineering, and sales and marketing of PWB chemistry. Active with IPC since 1981, Goldman has chaired numerous committees and served as TAEC chairman, and is also the co-author of numerous technical papers. To contact Goldman, click here.
Suggested Items
Trump Copper Tariffs Spark Concern
07/10/2025 | I-Connect007 Editorial TeamPresident Donald Trump stated on July 8 that he plans to impose a 50% tariff on copper imports, sparking concern in a global industry whose output is critical to electric vehicles, military hardware, semiconductors, and a wide range of consumer goods. According to Yahoo Finance, copper futures climbed over 2% following tariff confirmation.
Happy’s Tech Talk #40: Factors in PTH Reliability—Hole Voids
07/09/2025 | Happy Holden -- Column: Happy’s Tech TalkWhen we consider via reliability, the major contributing factors are typically processing deviations. These can be subtle and not always visible. One particularly insightful column was by Mike Carano, “Causes of Plating Voids, Pre-electroless Copper,” where he outlined some of the possible causes of hole defects for both plated through-hole (PTH) and blind vias.
Trouble in Your Tank: Can You Drill the Perfect Hole?
07/07/2025 | Michael Carano -- Column: Trouble in Your TankIn the movie “Friday Night Lights,” the head football coach (played by Billy Bob Thornton) addresses his high school football team on a hot day in August in West Texas. He asks his players one question: “Can you be perfect?” That is an interesting question, in football and the printed circuit board fabrication world, where being perfect is somewhat elusive. When it comes to mechanical drilling and via formation, can you drill the perfect hole time after time?
The Evolution of Picosecond Laser Drilling
06/19/2025 | Marcy LaRont, PCB007 MagazineIs it hard to imagine a single laser pulse reduced not only from nanoseconds to picoseconds in its pulse duration, but even to femtoseconds? Well, buckle up because it seems we are there. In this interview, Dr. Stefan Rung, technical director of laser machines at Schmoll Maschinen GmbH, traces the technology trajectory of the laser drill from the CO2 laser to cutting-edge picosecond and hybrid laser drilling systems, highlighting the benefits and limitations of each method, and demonstrating how laser innovations are shaping the future of PCB fabrication.
Day 2: More Cutting-edge Insights at the EIPC Summer Conference
06/18/2025 | Pete Starkey, I-Connect007The European Institute for the PCB Community (EIPC) summer conference took place this year in Edinburgh, Scotland, June 3-4. This is the third of three articles on the conference. The other two cover Day 1’s sessions and the opening keynote speech. Below is a recap of the second day’s sessions.