-
-
News
News Highlights
- Books
Featured Books
- pcb007 Magazine
Latest Issues
Current IssueThe Hole Truth: Via Integrity in an HDI World
From the drilled hole to registration across multiple sequential lamination cycles, to the quality of your copper plating, via reliability in an HDI world is becoming an ever-greater challenge. This month we look at “The Hole Truth,” from creating the “perfect” via to how you can assure via quality and reliability, the first time, every time.
In Pursuit of Perfection: Defect Reduction
For bare PCB board fabrication, defect reduction is a critical aspect of a company's bottom line profitability. In this issue, we examine how imaging, etching, and plating processes can provide information and insight into reducing defects and increasing yields.
Voices of the Industry
We take the pulse of the PCB industry by sharing insights from leading fabricators and suppliers in this month's issue. We've gathered their thoughts on the new U.S. administration, spending, the war in Ukraine, and their most pressing needs. It’s an eye-opening and enlightening look behind the curtain.
- Articles
- Columns
- Links
- Media kit
||| MENU - pcb007 Magazine
Victory Giant Technology: The Qualified Forerunner of PCB Smart Factories
August 2, 2017 | Tulip Gu, I-Connect007Estimated reading time: 7 minutes
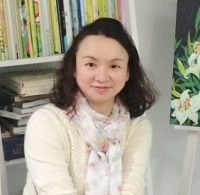
The topic of the July issue of PCB007’s China Online Magazine is “Automatic PCB Factories,” focusing on the pressures of cost, delivery time and process, and the irreversible trend toward automated PCB factories. Centering on this theme, we interviewed Andy Zhou, COO of Victory Giant Technology (HuiZhou) Co. Ltd., the first domestic PCB manufacturer who carries out large-scale implementation of intellectualization throughout the factory. As there are various opinions about how to build a smart PCB factory, we invited him to give us some ideas.
For quite a long time, Victory Giant Technology (HuiZhou) Co., Ltd. acted as the world’s largest PCB provider of high-density multilayer VGA (video card). The company’s layout also covers high value-added application areas like new energy automobile circuit board, server, industrial control, etc.
Benefiting from the smart manufacturing shop, which came into use in 2015, and gradually reaching target output, it brought huge growth in capacity and saved more labour cost. Most obvious, the price increase of copper-clad laminate and copper foils started from last year, instead, completely reflected the advantage of the supply chain.
Figure 1: Automated horizontal plating line at Victory Giant Technology.
Tulip Gu: As a forerunner of PCB smart factories, what kind of actions on the smart factory project is Victory Giant Technology taking, and what are the results?
Andy Zhou: Globalization is putting more and more pressure on market competition, and the life cycle of electronic products is becoming shorter and shorter. The market is requiring more and more from the PCB manufacturers. To conform to the times, Victory Giant Technology now has invested 1.12 billion yuan to build a smart factory based on Industry 4.0, thus we can fully realize “Production automation, unmanned logistics, intelligent scheduling, and digital management.” By making comprehensive innovation and intelligent reconstruction in the production process, we need only 350 people to fulfill 10 billion output value, and we have shortened the delivery time from 57 days to only 36 hours.
Gu: Do you agree that high-starting-point automation leads to high-production benefits? As we know, talking about “using machinery to replace people,” Victory Giant Technology is the leading player in the industry. You have mentioned that you need just 350 people to fulfill 10 billion output value, so do you think per-capita output value is good criteria to measure the success of automation? Or do you think there are other factors which are more important? (e.g., the perfect combination of people, machinery, information exchange is the very essence of automation.)
Figure 2: The LDI room at Victory Giant.
Zhou: High-starting-point automation does not always lead to high production benefit. High production benefit comes from system engineering. We started from the whole planning of IE, and used automation and informatization to achieve overall lowest cost, highest productivity and best quality. Per-capita output value is one of the key criteria to measure the success of automation, yet we regard return on investment as the most important one. If investing in automation could bring “lower cost, shorter delivery time, and better quality,” that means the project has succeeded.
Gu: Some experts think that the overall level of automation in China lags, but we should not improperly belittle ourselves, for we have the best manufacturing ecosystem in the world. What is your opinion? Along the way Victory Giant Technology pushing smart factory forward, what kind of problem you have encountered and how do you solve them? Could you please give us some real cases?
Zhou: China does have the best manufacturing ecosystem in the world. In the construction of the whole Victory Giant Technology smart factory, we can find 80% of equipment vendors that we need for our project within Pearl River Delta, a two-hour economic circle. And they are very willing to innovate and upgrade the equipment together with us. This is the important foundation which can ensure the success of our project. Along the way as we were pushing smart factory forward, the biggest problem we met is the standardization. In the past, when we talked about automation, we only focused on partial automation, but now we focus on whole automation. If we cannot realize the standardization of loading before and after the procedure, we cannot realize the logistics of automation. If we cannot realize the standardization of communication protocol between equipment from different vendors, we cannot realize perfect informatization. So standardization is always the stumbling block on the way of pushing smart factory forward. Based on “Collaborative Innovation,” we discuss with our vendors and we together work on standards. For example, we have solved the problem of feeding and unloading vehicles during different procedures, and we have also solved the problem of communication protocol between equipment from different vendors. Working together, collaboration innovation, and interconnection must be the inevitable choice of future intelligent manufacturing.
Figure 3: Robot in the exposure area.
Page 1 of 2
Suggested Items
Driving Innovation: Direct Imaging vs. Conventional Exposure
07/01/2025 | Simon Khesin -- Column: Driving InnovationMy first camera used Kodak film. I even experimented with developing photos in the bathroom, though I usually dropped the film off at a Kodak center and received the prints two weeks later, only to discover that some images were out of focus or poorly framed. Today, every smartphone contains a high-quality camera capable of producing stunning images instantly.
Hands-On Demos Now Available for Apollo Seiko’s EF and AF Selective Soldering Lines
06/30/2025 | Apollo SeikoApollo Seiko, a leading innovator in soldering technology, is excited to spotlight its expanded lineup of EF and AF Series Selective Soldering Systems, now available for live demonstrations in its newly dedicated demo room.
Indium Corporation Expert to Present on Automotive and Industrial Solder Bonding Solutions at Global Electronics Association Workshop
06/26/2025 | IndiumIndium Corporation Principal Engineer, Advanced Materials, Andy Mackie, Ph.D., MSc, will deliver a technical presentation on innovative solder bonding solutions for automotive and industrial applications at the Global Electronics A
Fresh PCB Concepts: Assembly Challenges with Micro Components and Standard Solder Mask Practices
06/26/2025 | Team NCAB -- Column: Fresh PCB ConceptsMicro components have redefined what is possible in PCB design. With package sizes like 01005 and 0201 becoming more common in high-density layouts, designers are now expected to pack more performance into smaller spaces than ever before. While these advancements support miniaturization and functionality, they introduce new assembly challenges, particularly with traditional solder mask and legend application processes.
Knocking Down the Bone Pile: Tin Whisker Mitigation in Aerospace Applications, Part 3
06/25/2025 | Nash Bell -- Column: Knocking Down the Bone PileTin whiskers are slender, hair-like metallic growths that can develop on the surface of tin-plated electronic components. Typically measuring a few micrometers in diameter and growing several millimeters in length, they form through an electrochemical process influenced by environmental factors such as temperature variations, mechanical or compressive stress, and the aging of solder alloys.