-
-
News
News Highlights
- Books
Featured Books
- pcb007 Magazine
Latest Issues
Current IssueThe Hole Truth: Via Integrity in an HDI World
From the drilled hole to registration across multiple sequential lamination cycles, to the quality of your copper plating, via reliability in an HDI world is becoming an ever-greater challenge. This month we look at “The Hole Truth,” from creating the “perfect” via to how you can assure via quality and reliability, the first time, every time.
In Pursuit of Perfection: Defect Reduction
For bare PCB board fabrication, defect reduction is a critical aspect of a company's bottom line profitability. In this issue, we examine how imaging, etching, and plating processes can provide information and insight into reducing defects and increasing yields.
Voices of the Industry
We take the pulse of the PCB industry by sharing insights from leading fabricators and suppliers in this month's issue. We've gathered their thoughts on the new U.S. administration, spending, the war in Ukraine, and their most pressing needs. It’s an eye-opening and enlightening look behind the curtain.
- Articles
- Columns
- Links
- Media kit
||| MENU - pcb007 Magazine
PCB Material Toolbox for Today’s 3G and 4G Networks and Future High-Speed Needs in 5G
June 27, 2018 | Stig Källman, ERICSSON with Happy Holden, I-CONNECT007Estimated reading time: 3 minutes
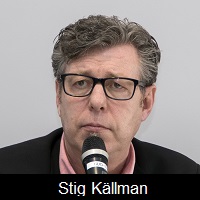
Introduction
The material toolbox idea first came up when I saw the IPC appendix list for standard 1-ply stack-ups. The idea is to make a very simple bill of materials, specifications and notes, and possibly use the same prepreg/resin in the laminate and in the core.
This article will introduce the material toolbox concept by discussing seven important factors:
- Standardization
- Toolbox idea
- Materials concerns
- Technology drivers
- Material needs
- Future
- Products
In the past, I came across many designers who wished to have the best specifications for impedance. They all start with specifying an impedance and conductor width that will make this according to their field solver. The conductor thickness is given as a constant due to plating or the base copper and the minimum requirement in the hole. This sets the requirement for certain material CCL and prepreg thicknesses. You may see this today in the material supplier’s data sheets for many customers.
If you start with what has the largest input to the impedance in the PCB you will find that it is dielectric thickness and conductor width that contribute the most. Accordingly, I reflected on what could be used as a benchmark for robust design and found that the Big Mac tastes the same anywhere in the world. Not the best burger according to some, but it’s my favorite as it’s something I can relate to and recognize. If I could copy this into our design toolbox I would have a design that, with the right recipe, would re sult in impedance performance of the chosen stack-up that would be the same regardless of where it is produced.
The Big Mac Index[1] provides an estimate of a particular country’s price level. It was first published the magazine The Economist, September 6, 1986. The index is based on McDonald’s Big Mac, which is uniform all over the globe while domestically produced.
For Standardization
You must have a dedicated lane to follow depending on your product requirements. If you choose the mainstream, you have the most options and the lowest price—but the more specific the requirements, the fewer the options and the higher the costs.
Philosophy of Toolbox
The big benefit of standardization is that if you know the impact of the prepreg on the design and you know the impact of copper foil and its different roughnesses you then can understand the impact of PCB manufacturing process tolerances—both the one you can take as default but also how they affect your design and the manufacturing requirements you put onto it. Then you can start comparing differences and design suitable resin systems with your material suppliers.
The toolbox consists of three levels:
- General properties as standard
- Group of materials with the same properties (multiple source)
- Specific supplier data (single source)
Material Concerns
When defining this we need to consider who in the supply chain controls the biggest impacts. We see it as follows:
Conductor width - PCB manufacturer
Conductor height - PCB manufacturer
Dielectric height - PCB laminate manufacturer
Dk/Df - PCB laminate manufacturer
By making the choice of specifying standard properties from production variations, the impact of Dk will be less important. Basically, if the tolerances of the dielectric are within IPC B/L (Class 2) and the conductor width for 0.1 mm conductors is +/- 0.03 mm, the impedance will be within 10% without need for measuring. If you choose to make a test board, measure the resulting properties and re-input into your field solver, the control will go to approximately 7%, without further measuring.
For the raw glass material there are a few sources in the world that make it. Many of the extra features with the material make it expensive due to the supply chain locations. Resin is made from oil, and that equals naphtha, a petrochemical product that is a mainstream raw ingredient for the whole industry. Here you must decide between either FR-4.0 (halogenated) or FR-4.1 (halogen-free) to start thinking of the resin’s properties to fulfill its purpose and not over-design the requirements. This helped us a lot going from the 3G products to 4G with its increased requirement for speed. Here it was easy to copy the building blocks of the older stack-ups and reuse them in new materials with better properties.
Weave is important to choose from the cloths mostly produced, and the most produced also got the best tolerances and availability. Higher frequencies require thinner, spread-glass cloths.
This article originally appeared in the May 2018 issue of PCB007 Magazine, click here.
Suggested Items
The Evolution of Picosecond Laser Drilling
06/19/2025 | Marcy LaRont, PCB007 MagazineIs it hard to imagine a single laser pulse reduced not only from nanoseconds to picoseconds in its pulse duration, but even to femtoseconds? Well, buckle up because it seems we are there. In this interview, Dr. Stefan Rung, technical director of laser machines at Schmoll Maschinen GmbH, traces the technology trajectory of the laser drill from the CO2 laser to cutting-edge picosecond and hybrid laser drilling systems, highlighting the benefits and limitations of each method, and demonstrating how laser innovations are shaping the future of PCB fabrication.
Day 2: More Cutting-edge Insights at the EIPC Summer Conference
06/18/2025 | Pete Starkey, I-Connect007The European Institute for the PCB Community (EIPC) summer conference took place this year in Edinburgh, Scotland, June 3-4. This is the third of three articles on the conference. The other two cover Day 1’s sessions and the opening keynote speech. Below is a recap of the second day’s sessions.
Day 1: Cutting Edge Insights at the EIPC Summer Conference
06/17/2025 | Pete Starkey, I-Connect007The European Institute for the PCB Community (EIPC) Summer Conference took place this year in Edinburgh, Scotland, June 3-4. This is the second of three articles on the conference. The other two cover the keynote speeches and Day 2 of the technical conference. Below is a recap of the first day’s sessions.
Preventing Surface Prep Defects and Ensuring Reliability
06/10/2025 | Marcy LaRont, PCB007 MagazineIn printed circuit board (PCB) fabrication, surface preparation is a critical process that ensures strong adhesion, reliable plating, and long-term product performance. Without proper surface treatment, manufacturers may encounter defects such as delamination, poor solder mask adhesion, and plating failures. This article examines key surface preparation techniques, common defects resulting from improper processes, and real-world case studies that illustrate best practices.
RF PCB Design Tips and Tricks
05/08/2025 | Cherie Litson, EPTAC MIT CID/CID+There are many great books, videos, and information online about designing PCBs for RF circuits. A few of my favorite RF sources are Hans Rosenberg, Stephen Chavez, and Rick Hartley, but there are many more. These PCB design engineers have a very good perspective on what it takes to take an RF design from schematic concept to PCB layout.