-
-
News
News Highlights
- Books
Featured Books
- pcb007 Magazine
Latest Issues
Current IssueThe Hole Truth: Via Integrity in an HDI World
From the drilled hole to registration across multiple sequential lamination cycles, to the quality of your copper plating, via reliability in an HDI world is becoming an ever-greater challenge. This month we look at “The Hole Truth,” from creating the “perfect” via to how you can assure via quality and reliability, the first time, every time.
In Pursuit of Perfection: Defect Reduction
For bare PCB board fabrication, defect reduction is a critical aspect of a company's bottom line profitability. In this issue, we examine how imaging, etching, and plating processes can provide information and insight into reducing defects and increasing yields.
Voices of the Industry
We take the pulse of the PCB industry by sharing insights from leading fabricators and suppliers in this month's issue. We've gathered their thoughts on the new U.S. administration, spending, the war in Ukraine, and their most pressing needs. It’s an eye-opening and enlightening look behind the curtain.
- Articles
- Columns
- Links
- Media kit
||| MENU - pcb007 Magazine
Collaboratively Creating Wearable Medical Products
May 28, 2019 | I-Connect007 Editorial TeamEstimated reading time: 5 minutes
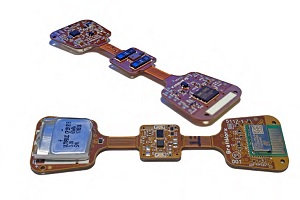
Patty Goldman, Barry Matties, and Happy Holden recently spoke with David Moody and Rich Clemente of Lenthor Engineering along with Anthony Flattery and Amit Rushi—their customers at GraftWorx. They discussed a recent project and how they worked together to solve a difficult problem by designing a rigidized flex circuit for their product.
Patty Goldman: Tony and Amit, thanks so much for joining us today to talk about your project with Lenthor.
Anthony Flannery: We had a number of different challenges that were unique to our product. It was fantastic working with Lenthor. We’re very happy with how the final product came out.
Barry Matties: Let’s start with some information on your company for our readers. What does your company make?
Amit Rushi: I lead business development product and marketing at GraftWorx, and I’ve been here for about two years. At GraftWorx, we build an end-to-end remote monitoring solution to target fluid management issues in chronic condition patient populations. We realized that a big gap in solving for that was the lack of a continuous-sensing technology that generates clinically actionable cardiovascular metrics, specifically hemodynamic metrics.
We took on this endeavor of creating an end-to-end platform, including making a new, continuous-sensing solution. In our vernacular, we refer to it as a SmartPatch. That journey has gone through its own gyrations to determine the adequate number of sensors, the desired flexibility of the circuit board, and how can we make it truly forgettable in the mind of the patient from a wearable perspective.
We started with the architecture of an end-to-end remote mounting platform but needed to solve for the gap of this continuous-sensing SmartPatch. The first market we’re targeting is dialysis—a patient population that, unfortunately, has a lot of rigor to living their life on dialysis; they go to dialysis treatment three times a week. Then, we’re looking at congestive heart failure or heart failure at large, since 40% of dialysis patients are diagnosed with heart failure. These are two very big markets in need of innovation, especially in supporting the patients’ lives outside of the clinic.
Goldman: Today, we’re here to talk about the topic for this issue, which is “From Design Through Final Product.” Our thought was to follow a product through from the design—the very beginning—through all of your concerns and what happens to make that product a reality. Let’s jump in at the design stage and talk about how everything worked out with Dave and Rich from Lenthor’s perspective. I know the end was good, but what happened in between?
David Moody: Tony, if you could give us a brief description of what determined the ultimate solution, that would be great. For example, it had to be a rigid-flex design from the standpoint of what you were trying to accomplish when you were all sitting around the table with a napkin trying to figure out what to do.
Flannery: It’s funny. We’re all going to sit down and write our memoirs about this company someday. GraftWorx has been around for about six and a half years, and we first cut our teeth on trying to bring a product to market on a monitoring system for peripheral arterial disease.
And there’s a long, convoluted history that goes beyond the scope of this conversation. What we ended up realizing was there was a tremendous opportunity to do this, and we’d get to market faster in the wearable space.
It’s no secret or surprise that there’s a tremendous opportunity in medicine to generate data that can make a huge difference in a clinical outcome. As Amit was describing, we’re trying to generate quality data that goes back to the clinic and has a positive impact on managing patients with a very difficult disease, end-stage renal disease. We wanted to design something that fits into a patient’s lifestyle with very little impact on their lives.
Figure 1: The GraftWorx end-to-end data path. Results from patient monitoring are transmitted via a semi-custom Bluetooth link to our B2H data bridge. Data is transmitted over a cellular IoT network to the Cloud where, after authentication, data is processed and alerts generated. Data and alerts are available to clinicians as part of their standard clinical workflow.
In terms of conveying what we’re trying to do, this is something that sits on your skin, such as a small, smart bandage. We wanted it to move with you and be flexible, comfortable, light, and forgettable. But at the same time, it’s a very sophisticated device. We have 11 different sensor data streams acquired during a reading. There is encryption that goes on so that we’re HIPAA-compliant in terms of how we store and transmit patient data. There is a tremendous optimization that went into power management so that our device lasts as long as it does on the skin, and this data is pulled into our cloud via a medical data relay (Figure 1).
What went into defining this device? Well, one of the things about the medical field that’s interesting is we have four different customers: patients, doctors, clinics, and payers. To answer your question about the journey in terms of starting the design, we have to take all of those players into account when we start laying out our product requirements, which then feed into our design inputs.
Clemente: I think you’re on a nice track. Would it be safe to say that the onset of wearable electronics helped you find a solution?
Flannery: I’m going to take a little hubris at this point and say we are the onset of wearable electronics (laughs). We’re one of the drivers in this field. There are other people on the market, for instance, such as iRhythm, who are out there looking for wearable devices to record EKGs and a number of other players in different spaces.
We’re driven by a need to solve a clinical problem. We’re not a hammer looking for a nail or a technology-driven solution; technology is our tool to solve a genuine clinical need. In a lot of ways, we’re taking the best that technology has to offer and designing it for our own product requirements and needs. We’re driving the revolution, not following on the wave. We like to think of ourselves as at the forefront.
To read the full article, which was originally published in the April 2019 issue of Flex007 Magazine, click here.
Suggested Items
DownStream Acquisition Fits Siemens’ ‘Left-Shift’ Model
06/26/2025 | Andy Shaughnessy, I-Connect007I recently spoke to DownStream Technologies founder Joe Clark about the company’s acquisition by Siemens. We were later joined by A.J. Incorvaia, Siemens’ senior VP of electronic board systems. Joe discussed how he, Rick Almeida, and Ken Tepper launched the company in the months after 9/11 and how the acquisition came about. A.J. provides some background on the acquisition and explains why the companies’ tools are complementary.
Elementary Mr. Watson: Retro Routers vs. Modern Boards—The Silent Struggle on Your Screen
06/26/2025 | John Watson -- Column: Elementary, Mr. WatsonThere's a story about a young woman preparing a holiday ham. Before putting it in the pan, she cuts off the ends. When asked why, she shrugs and says, "That's how my mom always did it." She asks her mother, who gives the same answer. Eventually, the question reaches Grandma, who laughs and says, "Oh, I only cut the ends off because my pan was too small." This story is a powerful analogy for how many PCB designers approach routing today.
Connect the Dots: The Future of PCB Design and Manufacturing
07/02/2025 | Matt Stevenson -- Column: Connect the DotsFor some time, I have been discussing the increasing complexity of PCBs and how designers can address the constantly evolving design requirements associated with them. My book, "The Printed Circuit Designer’s Guide to… Designing for Reality," details best practices for creating manufacturable boards in a modern production environment.
Siemens Turbocharges Semiconductor and PCB Design Portfolio with Generative and Agentic AI
06/24/2025 | SiemensAt the 2025 Design Automation Conference, Siemens Digital Industries Software today unveiled its AI-enhanced toolset for the EDA design flow.
Cadence AI Autorouter May Transform the Landscape
06/19/2025 | Andy Shaughnessy, Design007 MagazinePatrick Davis, product management director with Cadence Design Systems, discusses advancements in autorouting technology, including AI. He emphasizes a holistic approach that enhances placement and power distribution before routing. He points out that younger engineers seem more likely to embrace autorouting, while the veteran designers are still wary of giving up too much control. Will AI help autorouters finally gain industry-wide acceptance?