Search for New Semiconductors Heats up With Gallium Oxide
July 23, 2019 | University of IllinoisEstimated reading time: 2 minutes
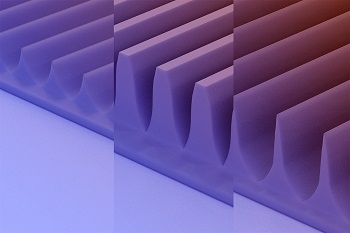
University of Illinois electrical engineers have cleared another hurdle in high-power semiconductor fabrication by adding the field’s hottest material—beta-gallium oxide—to their arsenal. Beta-gallium oxide is readily available and promises to convert power faster and more efficiently than today’s leading semiconductor materials—gallium nitride and silicon, the researchers said.
Flat transistors have become about as small as is physically possible, but researchers addressed this problem by going vertical. With a technique called metal-assisted chemical etching—or MacEtch—U. of I. engineers used a chemical solution to etch semiconductor into 3D fin structures. The fins increase the surface area on a chip, allowing for more transistors or current, and can therefore handle more power while keeping the chip’s footprint the same size.
Developed at the U. of I., the MacEtch method is superior to traditional “dry” etching techniques because it is far less damaging to delicate semiconductor surfaces, such as beta-gallium oxide, researchers said.
“Gallium oxide has a wider energy gap in which electrons can move freely,” said the study’s lead author Xiuling Li, a professor of electrical and computer engineering. “This energy gap needs to be large for electronics with higher voltages and even low-voltage ones with fast switching frequencies, so we are very interested in this type of material for use in modern devices. However, it has a more complex crystal structure than pure silicon, making it difficult to control during the etching process.”
Applying MacEtch to gallium oxide crystals could benefit the semiconductor industry, Li said, but the advancement is not without hurdles.
“Right now, the etching process is very slow,” she said. “Because of the slow rate and the complex crystal structure of the material, the 3D fins produced are not perfectly vertical, and vertical fins are ideal for efficient use of power.”
In the new study, the beta-gallium oxide substrate produced triangular, trapezoidal and tapered fins, depending on the orientation of metal catalyst layout relative to the crystals. Although these shapes are not ideal, the researchers were surprised to find that they still do a better job conducting current than the flat, unetched beta-gallium oxide surfaces.
“We are not sure why this is the case, but we are starting to get some clues by performing atomic-level characterizations of the material,” Li said. “The bottom line is that we have shown it is possible to use the MacEtch process to fabricate beta-gallium oxide, a potentially low-cost alternative to gallium nitride, with good interface quality.”
Li said further research will need to address the slow etch rate, enable high performance beta-gallium oxide devices, and try to get around the problem of low thermal conductivity.
“Increasing the etch rate should improve the process’s ability to form more vertical fins,” she said. “This is because the process will happen so quickly that it will not have time to react to all of the differences in crystal orientations.”
The low thermal conductivity issue is a deeper problem, she said. “High-power electronics produce a lot of heat, and device researchers are actively seeking thermal engineering solutions. While this is a wide-open aspect in the semiconductor field right now, 3D structures like what we have demonstrated could help guide the heat out better in some device types.”
Li is affiliated with the Nick Holonyak Jr. Micro and Nanotechnology Laboratory, the Frederick Seitz Materials Research Laboratory and the Beckman Institute for Advanced Science and Technology at the U. of I.
The National Science Foundation and the U.S. Department of Energy supported this research.
Suggested Items
Meet the Author Podcast: Martyn Gaudion Unpacks the Secrets of High-Speed PCB Design
07/16/2025 | I-Connect007In this special Meet the Author episode of the On the Line with… podcast, Nolan Johnson sits down with Martyn Gaudion, signal integrity expert, managing director of Polar Instruments, and three-time author in I-Connect007’s popular The Printed Circuit Designer’s Guide to... series.
Intervala Hosts Employee Car and Motorcycle Show, Benefit Nonprofits
08/27/2024 | IntervalaIntervala hosted an employee car and motorcycle show, aptly named the Vala-Cruise and it was a roaring success! Employees had the chance to show off their prized wheels, and it was incredible to see the variety and passion on display.
KIC Honored with IPC Recognition for 25 Years of Membership and Contributions to Electronics Manufacturing Industry
06/24/2024 | KICKIC, a renowned pioneer in thermal process and temperature measurement solutions for electronics manufacturing, is proud to announce that it has been recognized by IPC for 25 years of membership and significant contributions to electronics manufacturing.
Boeing Starliner Spacecraft Completes Successful Crewed Docking with International Space Station
06/07/2024 | BoeingNASA astronauts Barry "Butch" Wilmore and Sunita "Suni" Williams successfully docked Boeing's Starliner spacecraft to the International Space Station (ISS), about 26 hours after launching from Cape Canaveral Space Force Station.
KIC’s Miles Moreau to Present Profiling Basics and Best Practices at SMTA Wisconsin Chapter PCBA Profile Workshop
01/25/2024 | KICKIC, a renowned pioneer in thermal process and temperature measurement solutions for electronics manufacturing, announces that Miles Moreau, General Manager, will be a featured speaker at the SMTA Wisconsin Chapter In-Person PCBA Profile Workshop.