-
- News
- Books
Featured Books
- pcb007 Magazine
Latest Issues
Current IssueSales: From Pitch to PO
From the first cold call to finally receiving that first purchase order, the July PCB007 Magazine breaks down some critical parts of the sales stack. To up your sales game, read on!
The Hole Truth: Via Integrity in an HDI World
From the drilled hole to registration across multiple sequential lamination cycles, to the quality of your copper plating, via reliability in an HDI world is becoming an ever-greater challenge. This month we look at “The Hole Truth,” from creating the “perfect” via to how you can assure via quality and reliability, the first time, every time.
In Pursuit of Perfection: Defect Reduction
For bare PCB board fabrication, defect reduction is a critical aspect of a company's bottom line profitability. In this issue, we examine how imaging, etching, and plating processes can provide information and insight into reducing defects and increasing yields.
- Articles
- Columns
- Links
- Media kit
||| MENU - pcb007 Magazine
Residual/Free TBBPA in FR-4
January 31, 2020 | Sergei Levchik, ICL-IP AmericaEstimated reading time: 4 minutes
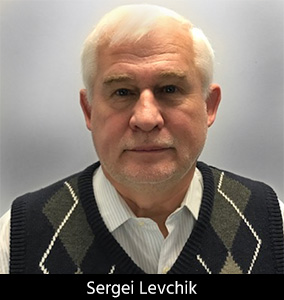
FR-4 laminates and prepregs are important fiberglass epoxy materials for printed circuit boards (PCBs). FR-4 base materials are the most popular grade used today because they offer a cost-effective and versatile solution for electrical engineers and product designers. The FR-4 designation was created by NEMA in 1968 and denotes the laminate is flame-retarded to meet a UL94 V-0 fire rating.
Trade associations such as IEC, IPC, and JEDEC have separated FR-4 into two distinct categories based on the flame-retardant mechanism—one using brominated chemistries and the other being comprised of flame retardants, such as phosphorus, nitrogen, and synergistic fillers. FR-4 base materials using bromine as the flame-retardant mechanism are made, so the bromine-containing molecules are chemically bonded in the epoxy resin polymer. Tetra-bromobisphenol-A (TBBPA) is an important and widely used flame retardant for FR-4 base materials. Difunctional epoxy resin is reacted with TBBPA to produce oligomers of epoxy resins (Figure 1). Once cured, there is no opportunity for TBBPA to leach out.
Figure 1: Reaction of TBBPA to form epoxy polymers.
In recent years, market and regulatory interest have grown regarding potential exposure to flame retardants found in consumer and industrial goods. This has come with greater expectations that manufacturers can estimate exposures over the life cycle of their product. In some jurisdictions, there are also regulatory reporting considerations (e.g., California Prop 65) that demand a higher level of manufacturing understanding of their goods. Product designers have long presumed TBBPA is fully reacted in laminates to optimize costs and material performance and do not generally report on TBBPA levels. However, there has been little public data documenting this or defining potential “free TBBPA” within the epoxy polymer.
Testing
Laminate samples were obtained from TUC (Taiwan), Shengyi Technology (China), and Ventec (China)—all major suppliers to the electronics supply chain. The laminates tested were selected to cover both ends of the glass transition temperature (Tg) range for FR-4 products used from 140°C to over 170°C. In addition, non-brominated FR-4 laminates were tested as controls.
Laminate samples were prepared for analysis according to EPA Method 3545A (Pressurized Fluid Extraction). Method 3545 is a procedure for extracting water-insoluble or slightly water-soluble organic compounds from soils, clays, sediments, sludges, and waste solids. The method uses elevated temperature (100–180°C) and pressure (1,500–2,000 psi) and is applicable to the extraction of semi-volatile organic compounds, organophosphorus pesticides, organochlorine pesticides, chlorinated herbicides, PCBs, and PCDDs/PCDFs, which may then be analyzed by a variety of chromatographic procedures. Prepared samples were analyzed for TBBPA by EPA Method 8321B, which covers the use of high-performance liquid chromatography (HPLC), coupled with both thermospray-mass spectrometry (TS-MS) and an ultraviolet (UV) detector, for the determination of a variety of solvent-extractable nonvolatile compounds.
Before analyzing FR-4 laminate samples from the three manufacturers, the test method was independently validated with respect to TBBPA detection and quantification. Two control samples of reportedly TBBPA-free epoxy resins were obtained. One gram of each board material was ground and extracted by sonication in toluene for 90 minutes at 27°C (as described in above EPA methods) to make sample solutions. Sonication equipment was set to maximum power to ensure an aggressive extraction of any background TBBPA. Sample solutions from this process were retained and fortified with pure TBBPA at three recovery levels: 2, 4, and 10 ppm.
Results
Control and fortified samples were analyzed for TBBPA in duplicate, and the data, are shown in Table 1. The TBBPA concentration in control samples was below the 1 ppm limit of detection. TBBPA recovery in fortified sample solutions was very consistent and repeatable across all samples and, on average, was greater than 80%. There was some slight decline in percent recovery with increasing TBBPA fortification. However, in all cases, percent recoveries were well above the 70% limit of acceptability for such methods and excellent confirmation of the methods for analyzing epoxy boards.
Table 1: Fortified sample method results.
Commercially produced FR-4 laminate results are shown in Table 2. The data show all the TBBPA FR-4s had less than 1 ppm (< LOD) of “free TBBPA” demonstrating essentially complete reaction of TBBPA with the epoxy. Non-brominated samples (6, 7, 8, 9) showed the same, demonstrating the methodology consistency. The results demonstrate that the full conversion of TBBPA is independent of the glass transition temperature (Tg) of the final product and show the robustness of these production processes with respect to TBBPA conversion. Tests 10 and 11 were high-performance laminates for high-speed/high-frequency applications (not FR-4), where TBBPA-based epoxy resin was a modifying polymer in the system.
Table 2: Free-TBBPA test results.
Conclusion
In summary, it is clear FR-4 products in the market today, comprised of reacted-in brominated chemistries, do not contain “free TBBPA” after curing. As such, these products demonstrate how reactive brominated flame retardants can be used effectively to enhance the fire safety of product designs. This information will be provided to the IPC (Association Connecting Electronics Industries) for inclusion in their next revision of IPC-WP/TR-584: “IPC White Paper and Technical Report on the Use of Halogenated Flame Retardants in Printed Circuit Boards and Assemblies.”
In addition, the information will be supplied to the IEC (International Electrotechnical Commission, Geneva, Switzerland) for consideration in their standardization activities. If any manufacturers of FR-4 would like to have data on their products included in the future reports, there is still time to have FR-4 products analyzed. Please email me at Sergei.Levchic@ICL-Group.com for the contact information of the test laboratory.
I would also like to thank the analytical laboratory Applied Technical Services in Atlanta, Georgia.
Sergei Levchik is R&D director at ICL Group.
Testimonial
"In a year when every marketing dollar mattered, I chose to keep I-Connect007 in our 2025 plan. Their commitment to high-quality, insightful content aligns with Koh Young’s values and helps readers navigate a changing industry. "
Brent Fischthal - Koh YoungSuggested Items
A.R.T. Ltd. Nominated in Four Categories at 2025 Instrumentation and Electronics Industry Awards
08/11/2025 | A.R.T. Ltd.Advanced Rework Technology Ltd. (A.R.T. Ltd.), a leading provider of electronics training and consultancy, has been shortlisted in four categories at the 2025 Instrumentation and Electronics Industry Awards, including Industry Personality, Academic Support, Rising Star, and Best Customer Service.
EMC Taiwan Receives IPC-4101 Qualified Products Listing Certification
08/08/2025 | Global Electronics AssociationIPC’s Validation Services Program has awarded an IPC-4101 Qualified Products Listing (QPL) to Elite Materials Co. (EMC), an electronics base material manufacturing company headquartered in Taoyuan City, Taiwan.
Global Excellence in PCB Design: The Global Electronics Association Expands to Italy
08/07/2025 | Global Electronics AssociationIn today's rapidly evolving electronics industry, printed circuit boards (PCBs) serve as the critical backbone influencing the success, reliability, and time-to-market of countless products. Recognizing this essential role, the Global Electronics Association (formerly IPC), a worldwide leader in electronics standards, certification, and education, is now expanding its internationally acclaimed PCB design training to Italy.
Dana on Data: Best Practices in Interpreting Drawing Notes—‘Use Latest Revision’
08/07/2025 | Dana Korf -- Column: Dana on DataThe global nature of electronics manufacturing requires clear, consistent, and precise communication, particularly in technical documentation. An area where miscommunication often arises is in interpreting drawing notes—small lines of text with the potential to dramatically impact product quality, manufacturing efficiency, and customer satisfaction.
Creating Connections in Mexico
07/30/2025 | Michelle Te, Community MagazineA concerted effort by the Global Electronics Association—Mexico team over the past year has created inroads for the Global Electronics Association (formerly IPC) with leading electronics companies, government offices, and academic institutions in Mexico. “Our goal is to bring more awareness to what the Global Electronics Association is and what it offers,” says Lorena Villanueva, senior director. “We also aim to increase our membership. Of 3,200 members of the Global Electronics Association, only 180 are in Mexico.”