Advantages of Using ZIF Connectors as a Termination Method
March 17, 2020 | All FlexEstimated reading time: 1 minute
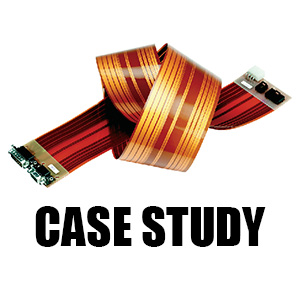
Application: Advantages and Information About ZIF Connectors
There are many types of connectors and termination methods available when designing a flexible circuit. One of the most common is the zero insertion force (ZIF) connector. The reason why the ZIF connector is so popular is that they eliminate the requirement for an added connector. They create a direct connection from the circuit to the mating connector reducing overall weight and cost. Here are a few general facts about ZIF connectors.
1. ZIF Connectors Capabilities and Requirements
- Our equipment allows us to hold ±0.002” tolerance on overall width
- The standard allowable thickness tolerance for 0.012” connectors is ±0.002”
- Specialized material sets have allowed us to hold ±0.001” thickness tolerance on ±0.012” requirement applications verified through multiple capability studies
2. Finishes of ZIF Connectors and Matching With Mating Connector
- Applications that require multiple insertions or greater mechanical force applications (membrane switches) should use hard electrolytic nickel gold (Ni/Au)
- Applications that are static or flex-to-install may only use ENIG/Tin/HASL, depending on the mating connector. It is important to match surface finishes with the contact finishes to inhibit corrosion, especially with tin and gold
- Electroless nickel immersion gold (ENIG) is our most common ZIF plating method and allows for solderability and one surface finish across the entire flex board
3. ZIF Stiffeners
- Polyimide is the most common material added to our standard flex circuit (polyimide) stackup to meet the final ZIF thickness requirement, which is typically 0.012”. Many ZIF connectors have some type of latching mechanism that allows the flex to be inserted and then ultimately clamped down using this latching mechanism
- For ZIF connectors that do not have a latching mechanism, we have utilized an F-R4 (rigid) material as the increased thickness material. The rigid material has the copper etched off which creates a “tooth” for the connector to grab onto versus the polyimide material, which is a smooth material
- ZIF stiffeners are designed to overlap the conductors; 1 mm is the minimum requirement, but 2.5–3 mm is recommended. This provides a “finger hold” for insertion to the connector and prevents mechanical stress and cracking of the conductors. The following images depict the correct design:
Disclaimer
Data presented for informational purposes only. Actual values and/or usage is for reference.
Suggested Items
The Evolution of Picosecond Laser Drilling
06/19/2025 | Marcy LaRont, PCB007 MagazineIs it hard to imagine a single laser pulse reduced not only from nanoseconds to picoseconds in its pulse duration, but even to femtoseconds? Well, buckle up because it seems we are there. In this interview, Dr. Stefan Rung, technical director of laser machines at Schmoll Maschinen GmbH, traces the technology trajectory of the laser drill from the CO2 laser to cutting-edge picosecond and hybrid laser drilling systems, highlighting the benefits and limitations of each method, and demonstrating how laser innovations are shaping the future of PCB fabrication.
Day 2: More Cutting-edge Insights at the EIPC Summer Conference
06/18/2025 | Pete Starkey, I-Connect007The European Institute for the PCB Community (EIPC) summer conference took place this year in Edinburgh, Scotland, June 3-4. This is the third of three articles on the conference. The other two cover Day 1’s sessions and the opening keynote speech. Below is a recap of the second day’s sessions.
Day 1: Cutting Edge Insights at the EIPC Summer Conference
06/17/2025 | Pete Starkey, I-Connect007The European Institute for the PCB Community (EIPC) Summer Conference took place this year in Edinburgh, Scotland, June 3-4. This is the second of three articles on the conference. The other two cover the keynote speeches and Day 2 of the technical conference. Below is a recap of the first day’s sessions.
Preventing Surface Prep Defects and Ensuring Reliability
06/10/2025 | Marcy LaRont, PCB007 MagazineIn printed circuit board (PCB) fabrication, surface preparation is a critical process that ensures strong adhesion, reliable plating, and long-term product performance. Without proper surface treatment, manufacturers may encounter defects such as delamination, poor solder mask adhesion, and plating failures. This article examines key surface preparation techniques, common defects resulting from improper processes, and real-world case studies that illustrate best practices.
RF PCB Design Tips and Tricks
05/08/2025 | Cherie Litson, EPTAC MIT CID/CID+There are many great books, videos, and information online about designing PCBs for RF circuits. A few of my favorite RF sources are Hans Rosenberg, Stephen Chavez, and Rick Hartley, but there are many more. These PCB design engineers have a very good perspective on what it takes to take an RF design from schematic concept to PCB layout.