-
-
News
News Highlights
- Books
Featured Books
- pcb007 Magazine
Latest Issues
Current IssueThe Hole Truth: Via Integrity in an HDI World
From the drilled hole to registration across multiple sequential lamination cycles, to the quality of your copper plating, via reliability in an HDI world is becoming an ever-greater challenge. This month we look at “The Hole Truth,” from creating the “perfect” via to how you can assure via quality and reliability, the first time, every time.
In Pursuit of Perfection: Defect Reduction
For bare PCB board fabrication, defect reduction is a critical aspect of a company's bottom line profitability. In this issue, we examine how imaging, etching, and plating processes can provide information and insight into reducing defects and increasing yields.
Voices of the Industry
We take the pulse of the PCB industry by sharing insights from leading fabricators and suppliers in this month's issue. We've gathered their thoughts on the new U.S. administration, spending, the war in Ukraine, and their most pressing needs. It’s an eye-opening and enlightening look behind the curtain.
- Articles
- Columns
- Links
- Media kit
||| MENU - pcb007 Magazine
What It Takes to Be a Milaero Supplier, Part 2
March 24, 2020 | Anaya Vardya, American Standard CircuitsEstimated reading time: 3 minutes
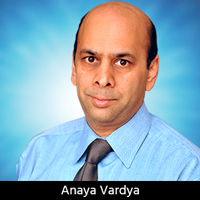
The decision to pursue military and aerospace (milaero) certification impacts every facet of the organization, and not every shop is prepared to make this transformation. Part 2 will focus on what it takes to be a milaero supplier in the areas of engineering and CAM.
Contract Review Handoff
As discussed in Part 1, contract review is done in sales and customer service; however, with today’s complicated product, some things just cannot be reviewed and verified until they reach engineering and CAM. In many cases, the contract review continues, as these departments do a thorough analysis of the customer’s data, drawings, and specifications.
As previously noted, most milaero customers will include their own very lengthy specification with every PO, outlining the requirements the PCB manufacturer must comply with. It is not uncommon for these documents to include requirements that must “flow down” to the suppliers of the PCB manufacturer. It may also contain specific purchasing requirements, including specific sub-suppliers that must be used by the manufacturer.
Engineering must work closely with purchasing to ensure these material and supplier requirements are accounted for. While it is the job of sales and customer service to capture all of these requirements in the quoting and contract review stage, it is the job of the engineering and CAM departments to make sure these requirements are integrated into the shop traveler and part-specific tooling. A poor contract review handoff will result in requirements being missed, potentially unshippable products, and poor customer satisfaction. In addition, required quality clauses, special inspection and tests, first article, and other deliverables all need to be identified and communicated to the quality group before the job is released to production.
Engineering Impact
An AS9100 aerospace and MIL-PRF-31032 order just cannot be processed the same as a commercial order. AS9100 has over 80 more requirements than ISO 9001—some of them minor—but the majority of them require additional documentation, activities, and/or processes that all have to be captured on the traveler. As a PCB performance standard, MIL-PRF-31032 orders require additional process controls, documentation, and testing. The labor required just to microsection a MIL-PRF-31032 job can be 3–4X that of a commercial order.
Processes, lead time and cost have to be factored in accordingly to ensure that these jobs meet the organization’s margin targets. One missed requirement can make the difference between making and losing money on any particular milaero order. Milaero orders cost more to manufacture than commercial orders; anyone who tells you differently is not being totally honest about it.
CAM Impact
The biggest impact to the CAM department is incorporating the required test vehicles, or coupons, into the production panel so that the required testing can be performed once manufacturing has begun. This can include special line widths and spaces that have to be measured for process control and complicated impedance coupons, but particularly microsection coupons.
This is where MIL-PRF-31032 starts to really separate from commercial or even aerospace products. MIL-PRF-31032 basically requires 200% microsectioning on every panel manufactured and is very prescriptive on the various different coupons needed and their location on the panel. Each particular coupon has a specific testing purpose, which not only presents a challenge in meeting the design requirements but also significantly impacts the panel utilization—the amount of available panel space for the product.
In some cases, the manufacturer will get fewer PCBs per panel strictly due to the number and placement of the required coupons. Fewer PCBs per panel mean a higher cost per individual board—one of the many added costs of producing milaero PCBs. Figure 1 shows the various coupons required for a typical MIL-PRF-31032 military order.
Coupon |
Purpose |
“A” |
General-purpose through-hole evaluation |
“B” |
General-purpose through-hole evaluation |
“C” |
Plating adhesion |
“D” |
Thermal shock |
“E” |
Isolation and resistance |
“G” |
Solder resist adhesion |
“P” |
Peel strength |
“S” |
Solderability |
Figure 1: Required military coupons per IPC-2221B.
Some of these coupons are specific to the specific part number design, and each requires a specific test and documentation. Again, there is 200% microsectioning per panel in both the X-axis and Y-axis.
Conclusion
In the engineering and CAM departments, becoming a milaero manufacturer changes the game significantly, adding new processes and a much higher degree of complexity when dealing with milaero orders. Milaero products demand some of the most technically challenging PCBs in the industry, and choosing a manufacturer that has the right staff, resources, and technology will be critical to your success. Part 3 will explore what it takes in the areas of purchasing and quality.
Editor’s Note: Read Part 1.
Anaya Vardya is president and CEO of American Standard Circuits. Vardya is also co-author of The Printed Circuit Designer’s Guide to… Fundamentals of RF/Microwave PCBs and Flex and Rigid-Flex Fundamentals. Visit I-007eBooks.com to download these and other free, educational titles.
Suggested Items
Driving Innovation: Direct Imaging vs. Conventional Exposure
07/01/2025 | Simon Khesin -- Column: Driving InnovationMy first camera used Kodak film. I even experimented with developing photos in the bathroom, though I usually dropped the film off at a Kodak center and received the prints two weeks later, only to discover that some images were out of focus or poorly framed. Today, every smartphone contains a high-quality camera capable of producing stunning images instantly.
Hands-On Demos Now Available for Apollo Seiko’s EF and AF Selective Soldering Lines
06/30/2025 | Apollo SeikoApollo Seiko, a leading innovator in soldering technology, is excited to spotlight its expanded lineup of EF and AF Series Selective Soldering Systems, now available for live demonstrations in its newly dedicated demo room.
Indium Corporation Expert to Present on Automotive and Industrial Solder Bonding Solutions at Global Electronics Association Workshop
06/26/2025 | IndiumIndium Corporation Principal Engineer, Advanced Materials, Andy Mackie, Ph.D., MSc, will deliver a technical presentation on innovative solder bonding solutions for automotive and industrial applications at the Global Electronics A
Fresh PCB Concepts: Assembly Challenges with Micro Components and Standard Solder Mask Practices
06/26/2025 | Team NCAB -- Column: Fresh PCB ConceptsMicro components have redefined what is possible in PCB design. With package sizes like 01005 and 0201 becoming more common in high-density layouts, designers are now expected to pack more performance into smaller spaces than ever before. While these advancements support miniaturization and functionality, they introduce new assembly challenges, particularly with traditional solder mask and legend application processes.
Knocking Down the Bone Pile: Tin Whisker Mitigation in Aerospace Applications, Part 3
06/25/2025 | Nash Bell -- Column: Knocking Down the Bone PileTin whiskers are slender, hair-like metallic growths that can develop on the surface of tin-plated electronic components. Typically measuring a few micrometers in diameter and growing several millimeters in length, they form through an electrochemical process influenced by environmental factors such as temperature variations, mechanical or compressive stress, and the aging of solder alloys.