-
-
News
News Highlights
- Books
Featured Books
- pcb007 Magazine
Latest Issues
Current IssueThe Hole Truth: Via Integrity in an HDI World
From the drilled hole to registration across multiple sequential lamination cycles, to the quality of your copper plating, via reliability in an HDI world is becoming an ever-greater challenge. This month we look at “The Hole Truth,” from creating the “perfect” via to how you can assure via quality and reliability, the first time, every time.
In Pursuit of Perfection: Defect Reduction
For bare PCB board fabrication, defect reduction is a critical aspect of a company's bottom line profitability. In this issue, we examine how imaging, etching, and plating processes can provide information and insight into reducing defects and increasing yields.
Voices of the Industry
We take the pulse of the PCB industry by sharing insights from leading fabricators and suppliers in this month's issue. We've gathered their thoughts on the new U.S. administration, spending, the war in Ukraine, and their most pressing needs. It’s an eye-opening and enlightening look behind the curtain.
- Articles
- Columns
- Links
- Media kit
||| MENU - pcb007 Magazine
I-Connect007 In-Depth: Averatek and RBP Chemical Ink Distribution Agreement
May 7, 2020 | Nolan Johnson, I-Connect007Estimated reading time: 6 minutes
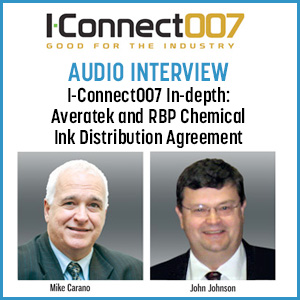
On April 30, 2020, Michael Carano, RBP Chemical Technology’s VP of technology and business development, and John Johnson, VP of Averatek, talked with I-Connect007’s Nolan Johnson about the new distribution agreement inked by the two companies.
Carano and Johnson spoke in more detail about the Averatek A-SAP(TM) additive plating process developed by Averatek. The conversation included why Averatek and RBP have partnered to distribute chemistries related to Averatek's A-SAP(TM) process.
For those not familiar, Carano described the capabilities and benefits of Averaek’s A-SAP(TM) technology. Averatek’s Johnson outlined why the company chose RBP Chemical for this distribution partnership.
I-Connect007 continues to deliver original reporting and coverage of the electronics design, electronics manufacturing, and contract manufacturing industries, including up-to-date information from the companies, associations, and supply chains, which serve the industry around the globe. Find the latest news and information at www.iconnect007.com.
Related Links:
- To download this audio (mp3) file, click here.
Nolan Johnson: Hi, Nolan Johnson here for I-Connect007. I’m speaking with Michael Carano and John Johnson. Michael Carano is VP of technology at RBP Chemical Technology, and John Johnson is VP of application engineering for Averatek. Gentlemen, thank you for joining me this morning.
Carano: Thank you.
John Johnson: Thanks.
Nolan Johnson: Averatek and RBP have partnered to distribute some chemistries that are related to Averatek’s ASAP process. For those who aren’t familiar, what is ASAP technology? And we’re talking here in response to a press release that you just recently released on this subject. What is the ASAP technology?
John Johnson: Nolan, the Averatek semi-additive process is really a technology set that allows for printed wiring board manufacturers to break through this three-mil line and space barrier. And it allows them to get down to one-mil lines or even less. And all that can be done with pretty minimal capital investment. And really the process integrates very well into the existing processes. It’s really a way to get down to those lower levels that have been very, very hard for our industry to get to using standard subtractive technologies.
Nolan Johnson: Mike, the Averatek ASAP process, according to the press release, provides an option to significantly change the technology of the application. How do you think this is going to benefit your customers in doing this?
Carano: Nolan, let’s look at it from several aspects because that’s an excellent question. Think about the industry in general and where it needs to go. First of all, what drives bare board designs? It’s the semiconductor technology. It’s putting more angels dancing on the head of a pin, which means the functionality of those chips, and those semiconductors must continually do more and more for today’s and the next wave of new technology—whether it’s the internet of things or 77 gigahertz and beyond. Smart factories, CFX, 4.0, and all of those things are going to require higher technology, higher speeds, and lower issues in general for the circuit board fabrication process.
Circuit board then needs to have higher lines and spaces because you have to be able to put more density on a circuit board, and you can’t have a circuit board that’s 40 inches long by 50 inches long; it must be smaller. Basically, it’s about wiring density to support the functioning of the chips—the BGAs. Wiring density is achieved generally in two ways: you increase the number of layers, or you have finer lines and spaces.
Now, obviously, from a fabrication standpoint, if you could reduce the line widths and spaces somewhere below three mil, and getting down to two mil, then that opens up a whole new world of technology for the industry, including the chip packaging side. That’s where I see this as being very exciting.
And the most important thing is yields. You’re competing in this business today on yields and technology. Technology curves, we all know, and you keep jumping the technology curve. What typically happens is yields can’t go down unless you have the right equipment, processes, and space. I see the ASAP process from Averatek meeting that need and going beyond in the future.
Instead of messing around with one-eighth ounce copper foils to get fine lines and spaces, and then worrying about adhesion—or trying to build up films and hoping you get metalization adhesion, which is a challenge—we can talk about that for three days, but we’re not. The process from Averatek is going to allow you to bridge that gap. It will make you because I always liked the phrase “jump the technology curve,” and jump it significantly.
Nolan Johnson: That certainly does open things up for the industry. John, RBP Chemicals has a nice, strong reputation. What drew Averatek to RBP’s distribution?
John Johnson: Prior to joining Averatek, I had been a customer of RBP for many, many years. And over that time, I had experienced what they could do: very consistent quality, great service, and competitive pricing. And really, at Averatek, we’re not about manufacturing; we’re about developing technology and focusing on innovation for our customers.
When it came to actually commercially providing these chemistries to the marketplace, we were looking for someone to partner up with to be able to supply them. And RBP was a top choice, in my mind, because of that past experience. We couldn’t pick a better partner, and they’re located in the Midwest, so it makes it pretty centrally located for customers here. They also have coverage around the world, so it was a really good fit for us.
Carano: John is right on, and one of the things about RBP is we are a technology provider and also have world-class manufacturing, which is done in Milwaukee, Wisconsin. The company has been in business since 1954 and has had two owners. That’s it. Mark Kannenberg is the current owner of RBP. He bought the company many years ago and has been guiding RBP for many, many years. We continue to serve the industry. As John said, we focus on quality. We focus on being our customers’ trusted source.
As I said, we have world-class manufacturing operations, so we can blend products for other companies who might need something that we’re not competing with, which we’re not, in this case; we’re just supporting Averatek. We continue to support Averatek in their ASAP process because it’s an exciting technology, and we have that type of control in place. And that’s going to give their Averatek’s customers very consistent quality. At the end of the day, they’re going to be consistent. They’re going to have technical support as needed from a world-class group of scientists and chemists and manufacturing professionals at our facility in Milwaukee, Wisconsin.
Nolan Johnson: Gentlemen, thank you for taking the time to talk a little bit more deeply about this announcement. Your time is very much appreciated.
John Johnson: Thanks, Nolan.
Carano: You’re welcome. We appreciate the opportunity, Nolan. Thank you again, and thank you, I-Connect007, for the continued coverage. It’s very much appreciated.
Nolan Johnson: It’s absolutely our pleasure. For I-Connect007, this is Nolan Johnson, and I’ve been talking with Michael Carano and John Johnson. Thanks for listening.
Suggested Items
Delta SEA Partner Event 2025 Unites Regional Partners to Embrace a “Future Ready” Vision
07/03/2025 | Delta ElectronicsDelta Electronics (Thailand) Public Company Limited, successfully hosted its Delta SEA Partner Event 2025: Future Ready at Delta Chungli Plant 5, Taiwan on June 10 – 11 , 2025.
Murray Percival Company Welcomes CeTaQ to Its Line Card, Optimizing SMT Processes for PCB Manufacturers
07/03/2025 | Murray Percival CompanyThe Murray Percival Company, a trusted supplier to the Midwest's electronics industry, is pleased to announce that it has added CeTaQ to its line card, a global expert in Surface Mount Technology (SMT) measurement systems.
RBB’s Jeff Schartiger Appointed to SMTA Ohio Board as Technical Advisor
07/03/2025 | RBBRBB, a trusted leader in electronics manufacturing since 1973, is proud to announce that Jeff Schartiger, Operations Manager at RBB, has been appointed to the SMTA Ohio Chapter Board as a Technical Advisor.
The Global Electronics Association Releases IPC-8911: First-Ever Conductive Yarn Standard for E-Textile Application
07/02/2025 | Global Electronics AssociationThe Global Electronics Association announces the release of IPC-8911, Requirements for Conductive Yarns for E-Textiles Applications. This first-of-its-kind global standard establishes a clear framework for classifying, designating, and qualifying conductive yarns—helping to address longstanding challenges in supply chain communication, product testing, and material selection within the growing e-textiles industry.
Eiyu Electronics Launches Pre-Assembled Module Product Line to Simplify Sourcing for Embedded Projects
07/02/2025 | BUSINESS WIREEiyu Electronics Co., Ltd., a Hong Kong-based electronic component trading company, today announced the official launch of its pre-assembled module product line, designed to help engineers and procurement teams save time when sourcing complex modular components.