Goodwinds Composites: Putting a Helicopter on Mars
July 31, 2020 | Nolan Johnson, I-Connect007Estimated reading time: 5 minutes
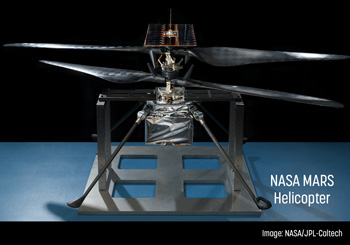
On July 30, 2020, Nolan Johnson spoke with Leland Holeman and Amelia Cook, the owners of Goodwinds Composites. While Goodwinds may be a small business, they still pack a heavy punch in the carbon fiber fabricating business. Case in point, the NASA Perseverance Mars rover mission, which had just launched as we captured this interview, carries a helicopter (named Ingenuity) in its payload and contains custom parts fabricated by Goodwinds.
Cook and Holeman detailed the process for working with NASA on these key helicopter components. They also clarified for Nolan how Goodwinds could be a part of the overall electronics manufacturing supply chain.
I-Connect007 continues to deliver original reporting and coverage of the electronics design, electronics manufacturing, and contract manufacturing industries, including up-to-date information from the companies, associations, and supply chains globally. Find the latest news and information at I-Connect007.com.
Related Links:
- To download this audio (mp3) file, click here
- Read our previous interview with Goodwinds here
- Learn more about Ingenuity here
- Watch the Perserverance launch here
Audio Interview Transcript:
Nolan Johnson: Hi, Nolan Johnson here for I-Connect007. Today, we’re talking with Leland Holeman and Amelia Cook, the owners of Goodwinds Composites. Welcome. You have some really exciting stuff on the threshold right now, don’t you?
Amelia Cook: Hi, Nolan. We sure do. It has been a really cool day for us.
Johnson: Tell us about it. What’s up?
Cook: We’re on the West Coast. At about 4:50 a.m., NASA launched their Perseverance rover, and attached to the belly of that rover headed to space, headed to Mars right now, is something called the Ingenuity Helicopter. It’s a little drone, and we manufactured the carbon tubes that are the landing gear for that little helicopter. We’re so excited because coming up in probably March or April next year, once it’s landed on the red planet and everything looks good, it’s going to take off and fly around, and hopefully transmit some of the first aerial videos of Mars back to Earth.
Johnson: That has to be just amazing. How did you get involved in that project?
Cook: Actually, NASA found us, and that’s just the coolest thing about the internet and the world right now; they visited our website. They were looking for composite tubes. They knew what they wanted. They ordered some without telling us, “Hey, we’re NASA.” They just got on our website, paid retail for some tubes that we’d already designed, and then gave us a call and said, “These are kind of right, but not quite right.” They worked with our engineers to figure out exactly what they would need. As you might imagine, the atmosphere on Mars and the UV exposure of that long flight in space to Mars presents some challenges for anything that’s going on that journey. We had to work with them on materials and all sorts of specifications for those composite tubes to make sure that they could fly in that atmosphere and then bounce.
The helicopter is going to have to land and take off a few times. We wanted to make sure that they had exactly the right impact strength, hoop strength, flexibility, UV protection, and all sorts of neat things. We worked with them on that, sent some prototypes, and then we did another round, and they loved it. It made the cut, was attached to the helicopter, and, of course, we had to keep quiet about it for several years actually. Then, once the whole project was a “go,” we were able to talk about it. We’ve been on the edge of our seats ever since watching the news and getting for launch.
Johnson: It sounds like the process was highly interactive with NASA once they selected you.
Cook: It absolutely was. Their engineers were so cool to work with and are amazingly smart people. This is a tiny little piece of the whole puzzle, but it had to be perfect. There were lots of conversations, back and forth.
Johnson: Leland, is custom work most of what you do?
Leland Holeman: It’s a large part of what we do, but we offer many, what we call, standard sizes of the different materials that we sell that are in stock, cut to a specific length, and have ready for retail or many wholesale shipments. In many cases, those standard items are used in industrial applications and are customized further just off the shelf. A large part of our business, however, is custom work—absolutely. We have a full machine shop on-site, and we do custom layup of different carbon fiber and fiberglass tubes as well as overwrapping of rods. We do lots of different rapid prototyping for people doing experiments that they don’t need large runs of material for. And we do it all.
Johnson: You obviously work a lot with OEMs and electronics manufacturing as a part of the components that you put together. Tell us how you fit with the overall manufacturing.
Holeman: In many cases, our components are structural. They’ll be spec’d or called out in an assembly of an item and some kind of box build, as a component within somebody’s design.
Cook: Right. It’s going to be the end-product that electronics manufacturers need to put their stuff inside of something. Carbon is wonderful for a lot of things. It’s extremely resistant to changes in the environment. That can be whether it’s UV, heat, or water—all those sorts of things. That makes it a really nice component for structural support. Anything that you want to put inside something that’s carbon or use carbon with, you’re not going to have expansion. You’re not going to have corrosion and all of those things that you might worry about as an OEM. With our carbon rods and tubes, we can build them to spec to fit into any of those sorts of things.
Johnson: And if it works for NASA, it should work for just about anybody.
Cook: That’s the idea.
Johnson: Congratulations on the big event for today and the news for the launch. It’s been great talking to you.
Cook: Thank you, Nolan. We really appreciate the opportunity.
Johnson: Once again, I’m Nolan Johnson with I-Connect007. We’ve been speaking with Leland Holeman and Amelia Cook from Goodwinds Composites. Thanks for listening.
Suggested Items
I-Connect007’s Editor’s Choice: Five Must-Reads for the Week
07/04/2025 | Marcy LaRont, I-Connect007For our industry, we have seen several bullish market announcements over the past few weeks, including one this week by IDC on the massive growth in the global server market. We’re also closely watching global trade and nearshoring. One good example of successful nearshoring is Rehm Thermal Systems, which celebrates its 10th anniversary in Mexico and the official opening of its new building in Guadalajara.
Hon Hai Education Foundation Continues to Promote Quantum Education
07/04/2025 | FoxconnHon Hai Education Foundation has long been committed to promoting forward-looking technology education in Taiwan's high schools, and held the "High School Quantum Teacher Training Camp" in Tainan City on July 1.
Incap UK Achieves JOSCAR Zero Accreditation
07/04/2025 | IncapIncap Electronics UK has been accredited under JOSCAR Zero, a new sustainability-focused extension of the defence and aerospace sector’s supplier assurance system.
Kitron Secures Contract for Components Supporting Unmanned Aerial Systems
07/04/2025 | KitronKitron has received a contract with an estimated value between EUR 4 and 8 million for the production and supply of advanced electronic components used in unmanned aerial systems (UAS).
NOTE Receives Order Worth 132 MSEK and Expands Collaboration with Customer within Security & Defense
07/04/2025 | NOTENOTE has received an order worth SEK 132 million from one of its existing customers operating within Security & Defense. NOTE thereby strengthens its long-term collaboration with the industry-leading customer.